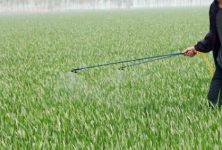
Bayer AgroSciences tests pesticide active ingredients with Turck RFID
[ad_1]
In their research laboratory in Monheim, Germany, scientists at Bayer AgroSciences are constantly exploring new active ingredients with the help of new modern equipment. After a long process, these active ingredients are developed into highly effective pesticides for use around the world.
One of the first steps in this process is the so-called preliminary screening. In the process, the newly developed substance is tested for its effectiveness by automatically spraying it onto the plants. Depending on the effect of the application, further research is done in the laboratory, then into greenhouse trials and finally outdoor trials.
Fully automatic preliminary screening
Bayer AgroSciences has developed a fully automated spray line for the initial screening process that can perform more than 25,000 spray operations per year. In each spray cycle, three plant groups were sprayed simultaneously with three different test compositions. These plant groups contained host plants for 8 diseases. “During the initial screening process, we sprayed 100 new substances on the plants at different concentrations on a day-to-day basis,” says Bernd Schulten, application engineer at Bayer AgroSciences. “To avoid losing control and getting the big picture, we use software support in our experiments. We get the trial series designs from the Data Processing Service. Enter it here, run the experiments, and send the results back,” Schulten said.
The most important factor in this process is the clear identification of groups of plants and their association with the substances sprayed on them.Originally used bar code stickers, but the machine has recently been updated to use a non-contactRFIDTechnology. “We worked with Tetrion, the industrial supplier responsible for maintaining and updating all of our machines in Monheim, to update our machines with a third booth and the entire system with the new SPS. Previously there were only stand-alone processes such as booths, conveyors and The aspirator was able to exchange signals, but now we can control and monitor everything via SPS,” explains Schulten. “Here we wanted to get rid of the bar code stickers because they don’t quite fit the corrugated design of the plant troughs, and they also don’t suit the environmental conditions they are subjected to. Also, the printers are very maintenance-intensive.”
During the search for the ideal RFID solution, the technical project team considered many different systems and suppliers. The decision was made to use Turck’s BL ident RFID system. “We wanted an RFID system that was easier to handle, more robust and cost-effective than other products. We found it all from this system from Turck,” says Schulten.
Easily handled with the CoDeSys system
For Volker Bachmann, the control specialist at Tectrion Robotik, the BL ident also has an unrivaled advantage: “Turk’s RFID system can be programmed with CoDeSys, making it possible to transfer complex tasks to the controls in the field. This allows us to This reduces the load on the computer that controls the test program.”
In the process of converting to an RFID system, Tetricon’s technicians needed to label nearly a thousand plant troughs, sticking the tags to the center of the plant troughs. Each tag can store 128 bytes, containing all the information about that particular plant. “Originally we wanted to omit the identification number on the label, but that didn’t guarantee enough flexibility. Now, as long as the label has all the information stored, the machine can work on its own, and each plant slot is identifiable. , even without a central computer,” Bachmann said.
Turck’s Q80 incorporates an RFID read/write head that reads and writes data directly when the plant trough leaves the spraying unit. Another read/write head is located where the plant trough leaves the machine. If the machine fails, or for some other reason the plant tank needs to be identified, Bayer employees can read the current state of the plant tank with a handheld RFID reader. The read/write head sends RFID signals to the BL20 modular remote I/O system. The data can be collected by means of a dedicated RFID disk and passed to the gateway for local RFID communication, so that only the reference data has to be sent to the host computer via Modbus TCP.
“It is very comfortable to operate Turck’s system,” continues Bachmann. “It’s not difficult to program, we can rely on established standards, like Ethernet, so we can easily integrate the system with the machine. Thanks to the modular concept, we can also set up everything we want just right.”
“Turck’s RFID system can be programmed with CoDeSys, so it is possible to transfer complex work to the control in the field. In this way we relieve the load on the computer that controls the test program.” Volker Bachmann, Tectrion.
[ad_2]