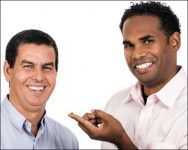
Campbell Soup uses RFID sensor tags to test cooking equipment
[ad_1]
Campbell Soup recently deployed a test of its RFID solution to test the operation of an aseptic cooking system. The system measures the temperature of vegetables and meat in soup cans as they are heated through heating tubes. The system embeds low-frequency RFID temperature-sensing tags in solid food, and wraps an RFID reader with an antenna around the heating tube. The technology, provided by Phase IV Engineering, is being used in Campbell’s headquarters laboratory to confirm the heating temperature of a continuous heating system (these sensors are currently only used on the heating system and do not track the temperature of batches of food ).
These products go through a number of processes before they can be sold to consumers. In some cases, some of Campbell’s products go through a process called continuous cooking. The ready-to-eat food goes through a long heating tube that extends to the packaging area. As the soup passes through the heating tube, the heating elements heat up, raising the temperature to a temperature that ensures sterile conditions in the center of the liquid and any solids. After heating, the soups are poured into sterilized packaging.
Ensuring that the heating tube heats the soup to the proper temperature requires some research and development. Insufficient heat will cause serious problems, but too much heat is also not ideal, it can affect the taste or consistency of the soup.
About four years ago, the Campbell Soup Company started looking for a technical solution to measure the internal temperature of solid food particles (the most difficult part of the soup cooking process). “The Campbell Soup Company was looking for a partner that could manufacture and provide RFID devices that measure the internal temperature of small-sized items,” said Rasheed Mohammed, the company’s senior program manager. He added that Campbell Soup needed a cost-effective temperature measurement device. In addition, the device requires the ability to measure food items that are moving at relatively high speeds.
Mohammed said: βIn the beginning, we approached Phase IV. Our role was to manage the project and relationships, and to help design and test the entire installation and system.β
Phase IV President Scott Dalgleish said, “Campel needs a very small sensor. It needs to have a small thermal mass to not affect the temperature of the meat. The sensor also needs to read the food in motion.”
The sensor tag is made of a low frequency 134kHz RFID chip with built-in temperature sensing. The size of the label is 6mm*5mm*4mm. The company also offers RFID readers and an antenna wrapped around a high-temperature plastic tube. The company installed a total of 6 readers.
When the soup food passes through the heating tube area, the reader will read the sensor tag embedded in the food. In this way, the reader can read the data including the temperature of the label.
Campbell and Phase IV chose low-frequency tags because low-frequency signals can penetrate liquids, Dalgleish said. In addition, the label can withstand high temperatures of 170 degrees.
Then, Phase IV software running on the PC will collect and analyze the read data. This way, Campbell Soup staff can tell if the food temperature is within an acceptable temperature range. In addition, engineers can adjust the heating tube settings to optimize the temperature of vegetables and meat.
In 2011, Campbell Soup adopted this solution. Since then, the system has contributed to the efficient operation of the cooking system. Mohammed Karkache, senior director of Campbell Soup, said: “The RFID system helps collect relevant data when new products and processes are introduced.”
As a next step, Karkache said, the company will use theRFIDThe system aids in the development of the next generation of aseptic continuous heating systems.
In the end, Rasheed Mohammed said, the system is optimized for the time employees spend on aseptic cooking systems and provides consumers with higher quality food.
γγ(The exclusive manuscript of rfid world network, please indicate the source author for reprinting!)
[ad_2]