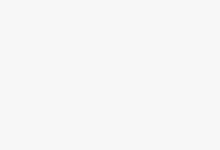
Case analysis of RFID technology application in hazardous area management
[ad_1]
With an increasing focus on safety coupled with cost-cutting goals and aging assets, at-risk industries are facing the need to improve the way they work to show that equipment located in hazardous areas is still suitable.
The traditionally prevalent practice, using paper-based forms, is now seen as an inefficient and ineffective method to capture detection results and accurately manage device registers.
fromInternet of ThingsThe benefits achieved by RFID solutions for many hazardous area industries show that the innovative use of today’s proven technologies, such as RFID tags and PDAs, opens the door to higher quality, lower cost, and more efficient ways of working. door.
What is RFID Technology
Aircraft originally used to identify “friend or foe” in World War II. With the gradual improvement of technology and the reduction of costs, the use of RFID has also been explored more. RFID, or Radio Frequency Identification Device for short, provides a unique way to identify the item it is attached to. For example, electric motors drive pumps in hazardous areas.
RFID technology has two separate parts, RFID tags and RFID readers. RFID tags are usually attached to identified materials. In our case, our pump. Included in the RFID tag is a unique identifier associated with the pump. The second part is the RFID reader, the portable is usually integrated into the current palmtop computer, and the fixed reader is the door, entrance/exit next to the physical connection.
Most RFID tags in use today are passive devices – they have no on-board power supply but derive their power from the signal they receive from the RFID reader. When you “scan” an RFID tag with the reader, the radio signal sent from the reader is enough to make the RFID tag operate and send back a signal containing data back to the reader, for example, sending back a unique identifier to identify our pump .
RFID tags are now available in many shapes and sizes – from shapes and sizes as small as a centimeter implanted into a device, to embedding a robust tag into a protective metal case that can be welded to the device, RFID tags are ATEX certified, used in hazardous areas.
Many RFID tags also provide visual identification, allowing the identification code to be read even when the RFID tag does not respond.
The latest global RFID identification standards now provide RFID users with the ability to easily identify devices anywhere, even in the supply chain, at a lower cost than was possible before.
RFID and Barcode
So isn’t RFID the same as barcode? Both technologies can provide a unique identifier to identify our pump. However, unlike barcodes, successful scanning of RFID tags is not affected by weathering or when covered with oil, salt, mud, dust, and other contaminants. Likewise, many RFID tags are very robust and can meet the longevity requirements of the connected equipment and have replaced barcode identification in more severe and challenging environments such as electrical and mechanical on oil and gas platforms equipment.
Another important difference in RFID technology is the ability to store static and dynamic information on RFID tags associated with our pumps. Details on the pump’s nameplate such as manufacturer, model and serial number can be stored on the RFID tag. Likewise, dynamically changing data, such as who the pump was last checked for, can be stored and rewritten simply by “RFID reader scan” RFID tags.
Dangerous Zone Challenges
Maintaining an accurate register of all equipment installed in a hazardous area can be an ongoing challenge, but it is a task that is essential to ensure that equipment is always safe for use and fit for purpose.
Periodically check and maintain device drivers whose information is held in registers, but these are often inaccurate or incomplete, leading to inefficiencies, and in the worst case, the wrong type of checks are performed on the device, or the wrong device is logged inspection results.
When the device is new, the nameplate and device identifier are easier to read. As an older asset, the nameplate has fallen off or is obscured by rust and becomes difficult to read.
Changes in maintenance management software can also affect the effectiveness of inspection and repair processes. Rarely are label name changes to the equipment maintenance system that are reflected immediately on the physical label of the device itself, resulting in discrepancies between the “software” label and the “hardware” label for the same item of equipment, causing inspectors to attempt to Potential confusion and waste of time when finding equipment for inspection, .
Inspections are also often hindered by the inspection method chosen and have the potential for human error and delays. Traditional methods require investigators to complete a paper-based form as they walk through the factory to conduct inspections. The end result is often difficult to read, requires manual entry into a computer database or Excel spreadsheet, visual results often drag on for weeks, and provide little opportunity to correct problems in person, or be subject to experience between different verifiers.
In inclement weather, there may also be a record of inspection results that allows the inspector to sit on a coffee break without looking at the equipment.
As production operators seek to extend the lifespan of their assets and reduce the cost of operating and maintaining these assets, traditional methods will be challenged and a new way will make it easier to maintain the quality of records and inspection history, and to improve work efficiency and effectiveness inspection and repair process.
RFID Rescue
Combined with a handheld computer (PDA), a device that scans RFID tags, device identification becomes fast and easy. The old way, scrubbing the nameplate with a wire brush to see the details is no longer necessary.
Consistently accurately identified equipment guarantees that even if the “software” label does not match the “hardware” label, it at least proves that the inspector has inspected the equipment.
Accurate identification ensures that the PDA’s screen displays the correct device type details and a checklist that automatically validates the results entered. Combining this knowledge with the inspector’s experience allows the PDA software to satisfy different levels of inspection experience.
After inspections are complete, results are automatically saved for the correct item of equipment, pending transfer to the inspection database – in this case, Arnlea’s “Inspect-EX” software – eliminating the human error and delays typically associated with inspections using traditional methods. Likewise, check for accurate records of dates and times to ensure that inspections are qualified for maintenance, and any overdue inspections mark actions to be taken.
When to add RFID
For installed equipment, RFID tags are simply added for the next inspection. However, the sooner RFID tags are installed, the greater the potential cost savings.
As a result, IoT RFID tags are becoming more commonplace during device manufacturing or when initially installing a new device. When a new asset is under construction, RFID tags are inexpensive to install and allow for a complete history from equipment “birth” to “decommissioning”.
Future RFID business opportunities
Many equipment manufacturers in other industries have quickly seen the benefits of using RFID tags in the Internet of Things to store important information about their products. For example, storing “shelf life” data highlights when items should not be used. Likewise, the stored user instructions and regulatory standard information on the RFID tag informs the user how and where the product should be used. There are even RFID tags used to limit who can use the product – for example, RFID is used on many car key fobs.
Is it beneficial for ATEX equipment manufacturers? These manufacturers can attach RFID tags to their equipment during the manufacturing process, storing important information such as manufacturer, model, serial number, ATEX certificate number, concept of EX protection, etc.
This data is stored on RFID tags, and forward-thinking manufacturers can help their customers – installers and users of their equipment – in their processes, to increase efficiency and therefore expand their competitive advantage.
RFID tags containing this type of information can be used to easily identify equipment that has been replaced and ensure inspections are performed on the correct grade and type of new equipment. Likewise, EX equipment registers can be easily kept updated without the constraints of effort and cost.
[ad_2]