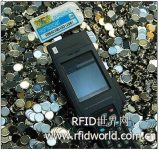
German Bavarian State Mint Adopts RFID System to Improve Production Management and Safety
[ad_1]
The Bavarian State Mint in Germany uses RFID to track the manufacture and transportation of euro coins (unprinted white coins arrive at the mint – finished products are shipped to the bank). The RFID system, which went live in 2005, greatly improves the mint’s security and more effectively controls the manufacturing process compared to the old mechanism that used paper sheets to identify containers during production.
The RFID system uses high-frequency tags, and the tag chip is NXP Icode SLI passive 13.56 MHz RFID chip, which conforms to the ISO 15693 standard. The tag is embedded in a plastic jacket, similar to a luggage tag, and attached to the container with plastic ties. Schreiner LogiData and smart-Tec provide labels and sheaths for the project.
Bavarian State Mint Adopts RFID System to Improve Production Management and Safety
In production, there are about 12 different types and sizes of containers to which the labels are applied, with the largest being able to hold 50,000 coins. The size of the container varies from 20*20 cm (length*width) to 1*1m. The coinage steps include stamping the coins, gathering coins of two different materials – such as 1 Euro and 2 Euro coins, and quality checking. Throughout the manufacturing process, each container goes through about 20 reads.
Before the finished product is loaded onto a truck for delivery to the bank, staff can remove the container label and put it back into service. About 3,000 tags are now in circulation, said Michel Dorochevsky, Chief Technology Officer of Softcon IT-Service. Softcon IT-Service designed and installed the system.
When a wooden, metal or plastic container with white coins is delivered to the mint, workers transfer the white coins into the mint’s container, and then use a Casio DTX 10 handheld with an RFID module to read the container’s RFID label and enter some basic information such as the ID number of the supplier and the container. This information, along with the tag’s ID number (only the ID number is stored in the tag), is sent to a database over the wireless LAN.
Every container of white coins must undergo quality control checks from time to time. When the worker receives the test command via the handset, he reads the label of the coin container that needs to be tested, and then reads the label of a thick plastic bag (used to transport white coin samples). Next, they took out a scoop of white coins and put them in a plastic bag. The database is immediately updated to the new location of these white coin samples, and the system confirms that the sampling process is normal.
When all the tests in the laboratory are completed, the staff uses a desktop reader to read the label of the sampling bag, notifying the system that the bag containing the white coins is to be returned to the production site. The results of each test are linked to the ID number of the sampling pack, allowing operators to track the quality of different batches of white coins. When the sample is sent back to the production line, the staff must scan the sampling package and destination container again. If the system informs that the quality is OK, the employee dumps the coins back into the container, a process that prevents mix-ups of different batches of white coins.
Workers use a forklift to lift the container, pour the coins into the machine, and begin printing and processing the coins. Employees must read the container label before any white coins or coins are poured into the container. Coins are not made in an assembly line, but are sent manually from one machine to another. The finished product is wrapped in paper rolls, loaded onto containers, weighed and placed in a safe room. When the coins are loaded into a dedicated shipping container and the card is loaded, the employee finally reads the Mint container tag and removes the RFID tag from the container for reuse.
Softcon IT-Service won the project in an open tender. The application system adopts the LogIDSoft platform of Softcon IT-Service, which can be used as middleware and production control software. The project was launched in 2006 and was carried out in two phases. Phase 1: Completion of the reading and quality control steps of the container when the white coins arrive at the mint. The second stage: Softcon IT-Service extends the RFID application to the entire production process. According to Dorochevsky, the biggest hurdles in the project were setting up the wireless local area network and training employees to use the system in a metal industrial environment.
The system cost $295,465, and Dorochevsky said the mint’s biggest benefit was improved security and production management, as well as transparency in production.
[ad_2]