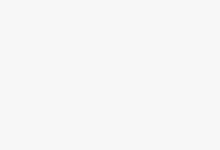
Hanford Nuclear Power Station adopts RFID technology to manage nuclear waste
[ad_1]
Along the Columbia River in southeastern Washington in the United States, there is a 586-square-mile Hanford nuclear power station, which was formerly a plutonium production plant. An environmental restoration team of about 700 people cleans up and transports the radioactive waste from the nuclear power station. The group is managed by a San Francisco-based engineering and construction company that has signed a contract with the U.S. Department of Energy to extract nuclear waste within 200 square miles along the Columbia River and transport it to a centralized landfill at the Hanford Nuclear Power Station, The average daily load is 200 vehicles, totaling 4,000 tons. Recently, the company used active RFID technology to automatically identify transport vehicles and steel containers, and combined RFID data with barcode systems and truck scales to accurately track the amount of transported waste.
A few weeks before the implementation of the RFID system, when the truck was driving on the truck scale, the operator had to manually input the ID number of the truck, and then use the ID number to call up the truck weight and the net weight of the container in the Oracle database, so as to calculate the weight of the coal truck material. Pure weight, cannot avoid the possibility of manual input errors. Julie Atwood, manager of the Environmental Task Force, said: “Waste management and transportation are the focus of our work, and the key is to identify the type of waste, determine its whereabouts, accurately record and track the whereabouts of the waste.”
Now, all AXCESS hardware in the entire RFID system is designed by AXCESS and produced by OEMs. The tags are mounted on trucks and on-board containers, using TI’s microprocessor, operating at 315MHz, and reading about 100 feet (30 meters). When the truck arrives at the metering station, the activator activates the tag with a 126KHz signal, the tag starts to transmit the signal, the antenna around the truck scale transmits the signal to the AXCESS reader, the reader transmits the tag data to the truck scale operating system, and the whole process is automatically completed , without manual intervention. Bechtel Automation’s IT department started the RFID project in January this year. The most difficult part was locating the best position of the tag on the steel container. The current AXCESS system has a read rate of 95% to 98%.
The staff of the Environmental Reconstruction Team input data into the barcode printing system, which will print the information of each vehicle on the barcode of the bill of materials, such as the level of radioactive elements, the location of discovery, etc. After the vehicle and container are identified, the scale station operator scans the barcode on the bill of materials with a scanner attached to the scale. The monitoring system on the truck scale can pass the barcode information to the processing program and alert the staff if the RFID tag was successfully read (if not, the ID of the truck and container will be manually entered into the truck scale system). Bechtel Automation’s IT department assisted scale manufacturer Cardinal in developing a software program that integrates barcode and RFID data into an Oracle database, clearly recording the type of nuclear waste each container is loaded with so that workers can take the correct measures before the next use. way to clean up.
At the landfill station, staff use handheld computers to perform final scanning of the barcodes on the bill of materials. At the end of each day, the data on the handheld computers is downloaded to a central database, producing a complete record of nuclear waste “from cradle to grave”. record.
Since the Hanford nuclear power plant does not transport its nuclear waste to other sites or receive waste from other nuclear processing plants, it will remain a closed-loop system in recent years.
[ad_2]