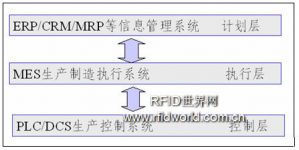
Hower Electronics realizes the production process control and quality traceability management of fire-fighting power supply through sincere MES and ERP systems
[ad_1]
I. Overview
Beijing Hower Group was established in 1993, mainly dedicated to the manufacturing and integration of fire fighting equipment. The products mainly cover fire power supply equipment, fire communication equipment, fire broadcast equipment, etc. Plan and orderly production, how to improve production efficiency, how to reduce production costs, how to ensure product quality, how to reduce inventory but not affect normal sales, etc. are all key issues faced by enterprises.
The group company has long foreseen the necessity and importance of information management, and has also applied UFIDA’s ERP production management system. Task planning has improved a lot of efficiency, but it still does not play a good role in management and decision-making in actual production and processing, item flow, work-in-process control, and immediate costs, especially in the process of completing processing under production tasks. The traditional manual management method based on experience is low in work efficiency and prone to some loopholes, resulting in confusion in production management and project management, resulting in indirect economic losses and waste of the company.
Beijing Jingcheng Zhibo Technology Co., Ltd. has put forward the overall solution of Howor ERP and MES production through repeated contacts with Howor production department personnel, meticulous market research, and summary of relevant successful cases implemented by Jingcheng in the past, which is the best way for Howor. Er Group effectively solves the problems faced by the current production department, and uses the organic and seamless combination of ERP system and MES production execution system to improve the status quo of production management, help enterprises reduce production costs, improve production efficiency, and indirectly ensure the sustainable development of the entire group. and increased competitiveness.
2. Demand analysis
The actual needs of Hower Group in terms of production management systems are as follows:
1. Integrate the resources of each project of the enterprise to achieve the systematization, humanization and processization of enterprise management, avoid waste of resources and improve the management level.
2. Based on barcode technology, the real-time data of feeding, production process (technical process) control, production data collection, quality management and other data that occur in the production line can be collected and uploaded in a timely manner, so that managers can quickly and intuitively understand the real-time production situation and master production. progress, improve project development and project management capabilities, and avoid project risks.
3. Solve the current situation of manual collection of warehouse management, such as warehouse management, inventory, allocation, return, etc., and improve the current situation of low efficiency and error-prone manual entry.
4. Collect the production process data of key processes and stations, record qualified or unqualified phenomena, count the productivity and efficiency of employees, equipment and production lines, and analyze process defects in the product assembly process to facilitate timely adjustment and early warning.
5. Through the workshop kanban, the work progress of the workshop, the quality status of the work-in-progress, the production status, etc., are constantly reflected in the workshop, and the workshop progress and product quality can be monitored in time, and the qualified rate and defective rate in a certain period of time can be generated, and the deviation map, Plato, etc. can be exported. .
6. Through packaging barcode scanning, establish the relationship between packaging and products, complete outbound scanning and after-sales service traceability, and associate all raw materials, components, suppliers, customers, and production processes through any barcode information on the packaging or the product itself. , quality inspection and other key information.
7. Establish a product after-sales service tracking system, recall and repair products with quality problems, record maintenance information, generate various after-sales service reports, and automatically query products with quality defects through barcode traceability.
8. The various accounts that occur in real time of the enterprise are formed into various accounting statements at the first time, so as to avoid various economic risks for the enterprise, reduce the phenomenon of dead debts and bad debts, and thus increase the operating income for the enterprise.
9. Form enterprise operation data into various statistical reports and intelligent charts in real time to provide data basis for leadership decision-making.
10. Reserve the data interfaces of other third-party software and hardware to facilitate the coordinated operation of various systems and equipment in the future.
3. Implementation plan
To cooperate with the informatization construction of Hower Group and the overall progress of the project, to implement the production management system, we follow the principle of overall planning and step-by-step implementation. After discussion, we believe that this ERP and MES integrated production system can be divided into two phases. Completed, the first-phase project is defined as the first-line MES production execution management, focusing on completing the assembly management of raw materials, semi-finished products, components, and finished products, enabling basic data collection and quality traceability. The second-phase project can be based on the first-phase project. The production system is expanded and optimized to meet the management function requirements of other departments, and finally achieve the level of group-based, platform-based and process-based management.
The first phase of the project focuses on completing the following basic functions:
System management, basic data definition, process and process route, production tasks and dispatch, picking and returning materials, warehousing, production execution (SMT placement, assembly, inspection, maintenance, debugging, aging, packaging, etc.), progress and follow-up Work inquiries, quality management, after-sales maintenance, barcode traceability, production reports, etc.
The second phase of the project completes the ERP management of the entire group. Combined with the foundation of the first phase of the project, it can realize a complete set of enterprise resource management such as office, personnel, planning, procurement, sales, production, picking and returning materials, barcode traceability, supplier evaluation, and customer analysis. system.
4. System structure
ERP, MES integrated production management system, as an enterprise integrated business management system, mainly includes control of all factory resources including materials, equipment, personnel, process instructions and facilities to improve manufacturing competitiveness, and provides a systematic integration on a unified platform. Functions such as plan management, document management, production management, quality management, etc., thus realizing the integration and integration of real-time EPR/MES/process control systems, which forms a bridge for information exchange, enabling enterprise managers to real-time Master production information and make production decisions.
The system adopts C/S (Client/Server) structure design, Microsoft SQL Server 2000 database, and the network topology is as follows:
Jingcheng ERP and MES integrated manufacturing execution system is based on a large number of network hardware equipment and barcode scanning equipment. The normal operation of these equipment ensures the stability of the system and is the premise for the safe, efficient and stable operation of the production workshop management system, including:
1. Server: HP/IBM server: Zhiqiang 2.4×2/1G/72G×2/Gigabit network card or above
2. Wireless mobile collector: (Casio DT930/Xunbao MC1000) used for logistics in and out links
3. Wired scanner gun in workshop: (SYMBOL-LS2208) for data collection of production line
4. Barcode printing equipment: (TSC-TTP243/Toshiba B-SX4T)
5. LED workshop kanban: (LED monochrome workshop display)
6. Station display: (9821SP LED industrial production line Chinese character liquid crystal display terminal)
7. Barcode label paper and related consumables, etc.
5. System function
The overall production management system is divided into two parts, one is the ERP enterprise resource planning system, and the other is the MES production execution system. Due to the difference of users, although ERP and MES use the same set of databases, they are divided into two operation interfaces. The ERP part is for the management of the entire enterprise business, such as: enterprise information, personnel, planning, warehouse management, expense management, etc.; MES Some are mainly used in the production workshop, and are mainly responsible for the management and control of the production process.
(1) ERP system part:
1. System management: Perform initial settings for system data, including user management, announcement release, etc., and provide data backup and recovery operations;
2. Personnel management: It mainly realizes the management of enterprise personnel and the definition of working hours;
3. Basic information: define, enter and maintain various basic information, such as warehouse information, commodity information, supplier, customer information, etc.;
4. Production management: Manage the materials, commodities, production documents, processes, procedures, etc. involved in the production process, formulate production plans, issue production tasks, and process materials for production, and process the entire production process. Automatic analysis and summary statistics of the data occurring in the system;
5. Warehouse management:
Manage the inventory of raw materials, semi-finished products and finished products, including the operations of drawing, inventory, picking and returning materials. In the warehouse management of this system, Jingcheng Software Co., Ltd. has introduced the latest bar code WMS management mode, using bar code equipment to replace manual data. The input work not only greatly improves the overall efficiency of warehouse management, but also reduces the overall operation error rate by 85%;
6. Procurement management: Realize the procurement process management of various raw materials and purchased products of the group, which is mainly reflected in the approval of various procurement documents, which not only ensures the quality and safety of the purchased products, but also reflects the various aspects of the procurement process for leaders in real time. In the processing of the links, the system automatically collects and summarizes the details of the procurement data and expenses of each process according to the procurement data;
7. Sales management: To realize the company’s management of customer sales, the principle is basically the same as that of purchasing management, but it is opposite to the business process of purchasing management;
8. After-sales management: If there is a quality problem after the finished product is sold to users, it needs to be dealt with through after-sales management, including maintenance notification, maintenance registration, maintenance parts replacement and other management. At the same time, the system forms after-sales product statistics for quality analysis and future corresponding Provide data decision support for process improvement;
9. Accounting management: The system automatically analyzes and summarizes various receivables and payables and various running accounts that occur in production and operation, and provides accurate and detailed accounting statements for enterprise leaders and related personnel;
10. Management analysis: conduct query and statistics on the data of the group’s daily business according to conditions, automatically summarize business data such as procurement, sales, production, quality and other links, and form corresponding columnar and pie-shaped smart charts, so that enterprises can operate The status of each link is clear at a glance, providing group leaders with real-time, accurate and vivid data reports and smart charts;
11. Financial management: In the Hower system, financial management is mainly realized through the interface with UF, here only the cost accounting such as production, invoicing, etc. is provided;
(2) MES system part:
1. System management: backup and restore management of MES system data, define and assign authority to MES system operators, and publish and maintain announcements of the production department;
2. Basic settings: define and describe information such as process parameters, process routes, process working hours, and unqualified phenomena in production;
3. In-process management: After the ERP system assigns the production tasks, the person in charge of the production department decomposes the tasks reasonably through the in-process management, and reasonably arranges production and shifts for the decomposed tasks. The system will use a large number of in-process management. The barcode equipment collects the data of the production line, such as: assembly, inspection, aging, repair until the finished product is packaged and put into storage. In this process, the barcode equipment not only automatically records the processing data of the in-process product, but also records the corresponding operator’s data. The operation information lays the foundation for the management of piece-record wages and performance-based wages, and provides a solid data basis for the future product quality traceability. It indirectly improves the work efficiency of production personnel, shortens the processing process of in-process products, and makes enterprises more competitive in the industry in the future.
4. In-process query: The person in charge of the production department and company leaders can query the comprehensive information of the current work-in-process production through a combination of custom conditions, so that the leaders can remotely and timely understand the processing status of the work-in-process, such as query with the work order, process pass rate Statistics, finished product qualification rate statistics, etc.;
5. Quality traceability: When there is a quality problem in the finished product, the relevant responsible personnel can use this module to automatically screen the product’s bill of materials, processing process, processing personnel, etc., and automatically trace the occurrence and cause of the defect according to the different phenomena.
6. Implementation Benefit
After Beijing Howor Group implemented the sincere ERP and MES production integrated management system, the overall informatization and management level of the enterprise has been significantly improved. The specific performance is as follows:
1. Realize the production mode according to plan, demand and product, reducing inventory and stockpiling
2. Real-time grasp of the production workshop and work-in-process production situation, and improve the work-in-process control of the workshop
3. Accelerate the progress of product production and improve workshop production efficiency
4. Eliminate the original manual data entry and data statistics work, and reduce a lot of manual repetitive work
5. Most of the data in the production process is automatically collected by bar code equipment, which greatly reduces the error rate of various data collection and station operation throughout the production process
6. Realize product quality traceability, supplier traceability, customer traceability, etc., to avoid unnecessary economic compensation disputes for enterprises
[ad_2]