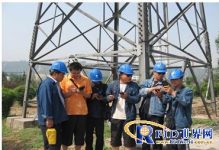
Jiurui successfully applied the equipment inspection project of China Southern Power Grid
[ad_1]
summary
Under the premise that the current information technology is relatively developed, at present, some power supply bureaus still use manual power inspection work, record the line inspection status on paper, and manually enter the defect management process after the inspection. With the increasing growth of line inspection business, the current manual recording method has been difficult to meet the needs of the increasing inspection business and new management needs. Moreover, for the inspection work of relatively far lines, it usually takes a long time for the staff to be in place, or even if it is in place, the staff in the relatively high or dangerous areas cannot collect information in time, which causes work problems. big mistake.
details
Jiurui successfully applied for equipment inspection of China Southern Power Grid
1. Analysis of power equipment inspection needs
Under the premise that the current information technology is relatively developed, at present, some power supply bureaus still use manual power inspection work, record the line inspection status on paper, and manually enter the defect management process after the inspection. With the increasing growth of line inspection business, the current manual recording method has been difficult to meet the needs of the increasing inspection business and new management needs. Moreover, for the inspection work of relatively far lines, it usually takes a long time for the staff to be in place, or even if it is in place, the staff in the relatively high or dangerous areas cannot collect information in time, which causes work problems. big mistake. Specifically:
1. The paper and pen input methods that have not changed for many years are backward and inefficient;
2. On-site inquiry of meter reading data is cumbersome and even impossible to check;
3. The computer input of meter reading data is like a bottleneck, which is time-consuming, laborious, and has a high error rate;
4. It is also the most important point: under the current new system of reducing personnel and increasing efficiency, there are usually only one or two people who go out for inspection, which means that there are no supervisors, but the substation equipment for inspection is not. Many, some inspectors with weak sense of responsibility work slack because they know that supervisors cannot follow them all the time
In order to realize the modern management of equipment inspection, ensure the safe and stable operation of power transmission and transformation equipment, reduce the labor intensity of inspection personnel, improve work efficiency, realize the standardization and institutionalization of inspection work, and make inspection personnel work in accordance with their work methods. specification.In view of the above reasons, the Power Supply Bureau draws on the advanced management systems at home and abroad, and with the strong support of relevant leaders and departments of the Provincial Electric Power Bureau, exploratively introduces barcode technology into the operation inspection management of power transmission and transformation equipment. Electric equipment and variables are encoded with different barcodes, using the standardized management of barcodes and the advantages of convenient portability, large data storage, and programmability of handheld collectors to develop a more practical and complete operating system.PDAThe inspection barcode data collection management system provides strong technical support for inspection and data management of power transmission and transformation equipment in the power grid.
2. Introduction of PDA inspection system:
The PDA industrial-grade mobile data terminal can help the inspection staff to easily realize real-time data collection during the inspection process for the relatively high or far areas of the substation equipment during the inspection process, and if the problem is detected in the same area during the inspection process. There are many problems that cannot be solved due to different descriptions. The inspectors can use the real-time data collection function of PDA to feed back to the system analysis background, and the background can quickly search for the same problems encountered in this area. In addition, the background system information center can transmit the information in the planning area of the inspection to the PDA before the inspection personnel go on the inspection, so that the inspection personnel can use the PDA to conduct online help inquiries if they encounter any questions during the inspection work. Improve work efficiency. In addition, the use of PDA can fundamentally eliminate loopholes such as insufficient inspection personnel, fabrication of job reports, and arbitrary modifications. Therefore, the organic combination of PDA industrial-grade mobile data terminal and management information system can ensure that the working status and quality of the production site meet the standards, truly implement the enterprise management requirements into daily work, and realize the scientific arrival of management personnel.
3. PDA software system design:
The PDA inspection barcode data collection management system is a computer-managed inspection operation management system that is managed by a handheld computer collector and a computer-run barcode data collection program. It is suitable for users of enterprises, independent substations and centralized control stations to customize and manage the equipment information, inspection tasks, inspection lines, inspection points and inspection items involved in power inspection. The mobile terminal realizes the standardization of inspection in place control and defect management, thereby improving the equipment management level of the substation.
The design of the system must first fully consider the equipment items that need to be inspected and the optimal line for inspection equipment, and then arrange the codes of the inspection items according to the determined inspection lines and inspection items, and paste the codes. All codes are unique to the relevant device. During the inspection operation, the inspectors carry out the inspection items one by one according to the preset inspection items. When using the handheld collector to inspect the running equipment, use the collector to scan the barcode code of the equipment, and then input the running data, or input the running data through the selection menu. The data collection time is automatically generated and cannot be modified manually, avoiding the need for inspection. Cheating by workers. During the operation, the operation of the next project can only be carried out after the data collection of the current project is completed, so as to avoid the omission of the work of the operators and avoid the slack of the operators.
The data stored in the collector can be queried, edited or deleted in real time when needed. During the operation data entry process, the data validity check will be carried out. If the data is illegal or the variable exceeds the limit, the operator will be prompted to confirm the input or modify it. Using WIFI, 3G, GPRS wireless communication methods or other communication methods (such as Activesyc real-time synchronization), the inspection data in the collector can be uploaded to the computer simply and quickly. Through the computer platform, the query and printing of the operating data can be realized, and the data can be edited if necessary. At the same time, the statistics and analysis functions of the operating data can be realized, and the required curves can be generated according to the requirements, which can be provided to managers and decision makers in time. necessary information.
The implementation of the inspection bar code data collection management mode avoids the previous work method of the inspector carrying a bunch of forms to the scene, and then entering the computer one by one after returning. The use of bar code technology and photoelectric communication technology not only reduces labor intensity, but also increases real-time performance. With strong technical support, it also provides convenience for the real-time operation data archiving of power transmission and transformation equipment. The specific advantages are as follows:
1. Get rid of paper and pen, through programming, can realize data illegal prompt, data omission prompt; data entry is accurate and fast;
2. On-site query, deletion and modification of transcription data, LCD display is clear at a glance;
3. The collector is connected to the computer, and the data transmission is completed instantly and accurately;
4. Avoid the phenomenon of slack work by the inspection operators.
4. PDA inspection software development plan and realized functions:
Our company will customize and develop PDA application software for users. The on-site business support system on the PDA data collector should meet the on-site business needs, various operations and provide human-machine interface design suitable for industrial on-site operations. Complete basic inspection work requirements and business processes, and give necessary prompts for barcode collection errors and errors.
development environment
This system will be based on Microsoft .NET architecture, with C# as the development language, on the PDA side, under the Microsoft Windows CE or Windows Mobile environment, a set of PDA power equipment inspection system based on .NET architecture will be customized and developed for users to realize the power equipment inspection system. The inspection friendly user interface supports users to collect data in the business process, and provides the operation of various functional modules such as data query, storage and verification in the field.
Approximate workflow
The PDA inspection software realizes the following 6 main functional modules:
4.1. Equipment operation inspection – equipment inspection personnel
4.2. Preventive work – professional supervisor
4.3. Corrective work – quality supervisor, professional supervisor
4.4. Quality inspection, professional inspection – quality supervisor, professional supervisor
4.5. Meter reading management – meter reading staff
4.6. CRM system complaints and repairs – managers, maintenance personnel
The software simulation interface is as follows:
4.7 Software interface data and parameter reference
1. Automatically count and analyze the work status of inspectors.
2. Permission settings to prevent unauthorized operations.
3. Parameter download
4. Data upload
5. Benefits after the implementation of PDA software:
1. Improve the efficiency of inspection lines and improve the management of inspection work;
2. Reduce labor and input costs, reduce work intensity and improve work efficiency;
3. Improve the inspection service level and defect management level;
4. Cooperate with the construction of power system informatization starting from basic data collection;
[ad_2]