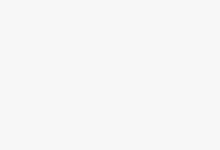
New experience of RFID integrated application ~ Formosa Plastics Network promotes the inspection plan of M-mode equipment in place
[ad_1]
Formosa Petrochemical refines 21 million metric tons of crude oil each year, 450,000 barrels of oil per day, and 3.8 million metric tons of light oil. If you have ever been to Formosa Plastics Mailiao Industrial Zone, you will be impressed by the reclamation project in Liuqing Park. . Looking around, you can see the spectacular industrial town scenery. Among them, there is huge production capacity in the well-organized oil tank pipelines! Formosa Petrochemical ranks among the top in the global market in terms of production capacity. It has a large number of production equipment and is responsible for the operation and management of oil refining equipment. There are up to 100 people. All production machines and equipment on site run smoothly 24 hours a day, and the responsibility to shoulder can be said to be very important.
Since the normal operation of machinery and equipment will directly affect the production efficiency, any abnormal situation must be dealt with at any time. Therefore, in order to effectively control the smooth operation of on-site production equipment, the management of production equipment is very important. The factory management personnel organize the patrol inspection operations of each factory area into several groups through task grouping, and three shifts of personnel conduct regular inspections every day to control the operation status of the on-site equipment at any time. In the past, during inspections, personnel used hand-copying methods to transfer the sensing records of various instruments to the book, and then “judged” whether the values of the instruments and equipment were normal based on experience values. However, the manual operation mode of operation and maintenance of machinery and equipment is complex, and the workload and pressure of management personnel are relatively large. “The inspection and inspection of personnel in place cannot be implemented, and it is impossible to confirm whether the personnel have arrived at the location for inspection. Secondly, the copying operation is complicated and time-consuming, and the book data cannot be effectively analyzed, which affects the work efficiency of personnel; moreover, equipment abnormalities cannot be detected and prevented in time, which relatively indirectly increases industrial safety risks and follow-up processing costs. 』ㄧ The on-site manager of the factory mentioned the difficulties in the early equipment inspection operation.
Inspection implementation management, process improvement results
In order to improve the efficiency of machinery and equipment maintenance and inspection operations and more effectively reduce the probability of on-site industrial safety accidents, Formosa Petrochemical entrusted Formosa Plastics Network Company to assist in planning the informatization project of equipment inspection operations. After an in-depth review of the operation process by the consultants of Formosa Plastics Network and the plant management personnel to understand the actual needs of on-site operations, Formosa Plastics Network believes that the first step is to start from the process side and replace manual labor with automated management operations, which is expected to effectively reduce the risk of human negligence. At the same time, after referring to the equipment inspection operations of major international manufacturers, Formosa Plastics Network recommends customers to use the three-in-one application service of “RFID + PDA + Information Management Platform”, and tailor-made a set of “Formosa Plastics Network RFID In-place Inspection System” for plasticization. .
RFID combined with PDA, managers applaud
“Formosa Plastics Network RFID In-place Inspection System” integrates mobile application devices PDA and RFID technology, and develops software operation interfaces according to customer needs, effectively exerting the functional characteristics of RFID short-distance and PDA mobile application, not only shortening the inspection operation time, and making Managers can keep abreast of equipment dynamics at any time, reduce the risk of equipment abnormalities and processing costs, and can effectively control personnel to conduct inspections in place. Taking into account the special needs of customers – the on-site personnel are in a working environment where oil and gas may float in the air, in order to prevent industrial safety hazards, PDAs that have passed the explosion-proof specifications of the Industrial Technology Research Institute are specially selected on the inspection device to ensure the operation of the system. Safe and sound.
“To implement the inspection operation, the most basic requirement is that the personnel are in place to inspect. The management functions that were lacking in the past were all obtained on the inspection management platform, which indeed saved a lot of trouble. 』『The abnormal interpretation of the trend of the equipment value is of great help to the annual maintenance, and it can also reduce the errors caused by the personnel’s experience judgment. 』The director of the plasticization Mailiao plant gave positive affirmation to the benefits of promoting the informatization management of inspection operations.
Eliminate the doubts of senior employees, and the seeds of the factory are paid
Although the “RFID in-place inspection system” has brought a lot of management benefits to the plasticizing company, the grass-roots employees were not able to accept such changes when it was implemented. Taken aback, some employees even feel that personal inspections appear to be monitored. In order to solve the obstacles encountered in the implementation of the system, the plastination company adopted the “seed player system”. The company found a group of employees who voluntarily used the new system, and took the method of on-site demonstration to teach these colleagues how to use it, and gave them the seed personnel. The roles are assigned to each inspection team and promote other colleagues in the way of “sharing”; at the same time, in the implementation, soft persuasion is the main way, rather than a strict punishment mode. In this way, through the peers among employees Influence and sense of honor serve as the driving force for employees to learn the new system. Gradually, the voices of the rebound become less and the system introduction effect is very good. Some employees even take the initiative to stay in the factory to study after get off work. A senior employee of a plasticizing company said: “I feel a great sense of accomplishment when I walk around the factory with a PDA for inspection!”
Seamless integration of back-end systems, more solid enterprise management
Since Microsoft .Net is used as the development platform, the system operation is very easy to use, and customers do not need to invest high maintenance and operation costs in terms of integration with internal systems or follow-up maintenance. It can be said that the “RFID in-place inspection system” is the largest One of the features; through the automatic management of equipment inspection operations, company supervisors can review the latest equipment operating status information at any time. If the on-site equipment and machines are abnormal, they can implement abnormal processing and maintenance through the automatic process sign-off mechanism. Tracking and auditing with fixes. Taking the plasticizing company as an example, the “RFID in-place inspection system” integrates data serially with the internal ERP and Lotus Notes to enhance the performance maintenance function of equipment and machines. “ERP and Notes are information platforms that are used every day, and the inspection data is integrated, so there is no extra workload. ‘ said a staff supervisor in the general manager’s office of plastination.
In addition, the “RFID in-place inspection system” uses RFID technology. Because RFID has the characteristics of non-contact, rewriting, and reading while moving, it has begun to attract many enterprises. For Formosa Plastics, the service project of the inspection system for plasticizing equipment can be said to be a stepping stone for the promotion of RFID application management technology. The outside world’s impression of RFID is mainly in the fields of warehousing, logistics and transportation management. However, RFID software can be used in a wide range of fields. For example, it can further integrate business intelligence functions (such as data warehousing, data mining, etc.) Managers do serve as the basis for decision-making.” In the future, Formosa Plastics also plans to promote the “RFID in-place inspection system” to other industries, not only in petrochemical or manufacturing industries. For example, in the telecommunications industry, the current patrol operation of telecommunications base stations in Taiwan can be completed by integrating geographic information system (GIS) with RFID. As for patrols in other industries (such as schools or transportation) Inspection jobs can also be imported with the same concept. Formosa Plastics has plans to continue to introduce M-based solutions for in-place inspection operations and provide more value-added services. In the future, it will integrate more mobile devices such as mobile phones, PDAs, GPS, Wi-Fi and WiMAX, etc., to provide customers with the most Perfect support and service.
[ad_2]