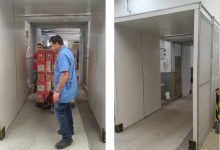
Porcelain manufacturer Oxford deploys RFID system to reduce errors in packaging delivery process
[ad_1]
Oxford, the largest manufacturer of ceramics and porcelain in the Americas, recently announced that the company will withdraw its investment in an RFID system within 12 months, which helps reduce errors in the delivery of goods to zero. Marcelo Correa, Oxford’s logistics and RFID project manager, announced the result to the company’s board of directors.
Oxford is located in Santa Catarina. The company has 2,500 stock-keeping units (SKU) and three manufacturing plants produce 6 million products per month. After the production is completed, these products will be packaged, and then separated and delivered according to customer requirements.
Oxford mainly supplies catering utensils (plates, cups, cups and sets of pots) to Brazil and the world. Some of these customers reported that the balls were packaged under their own brands, such as Starbucks coffee.
When leaving the factory, these goods will be packaged according to customer requirements, and then placed in a standard packaging box in a certain order. A standard packing box can put 12 shallow plates, 12 soup bowls, etc. Oxford’s RFID system helps complete orders by attaching smart tags to packaging areas and cardboard boxes.
Each packaging box will be attached with a label with built-in unit number, content and other information. These goods will then be transferred to the inventory area for stack storage. RFID readers are installed in the passage from the packaging area to the inventory area to read the tags. Correa explained: “Products are usually transported by trolley or forklift and are easy to locate.”
In addition to providing the exact location and identification of each stored item, RFID technology is also used to improve the efficiency and accuracy of order separation. Correa said: “Each order will be read by an RFID reader, and then directed to the correct warehouse dock. This technology reduces the delivery and distribution process errors to zero.”
(Left: Employees use trolleys to transport goods to the RFID channel for reading and identification; Right: The RFID channel uses a wave attenuator to attenuate the RFID signal at the entrance and exit of the channel)
Using this technology, Oxford reduces additional costs, including reverse logistics of misdelivered goods. Correa said, “These costs are enough to recover the system investment cost within a year. In addition, RFID has also improved the quality of the product.”
Starting next year, the company will extend the use of RFID technology to the transportation link to improve order efficiency.
Before using RFID technology, the company completed production tracking by scanning bar codes and a warehouse management system (WMS). He explained: “Using RFID technology, the delivery process is fully automated. Each batch of goods will be controlled by an RFID reader.”
The RFID project uses GS1 passive EPC ultra-high frequency (UHF) RFID standards, which is conducive to rapid deployment. Two fixed readers are installed in each channel, one is installed at the entrance and the other is installed in the shipping area.
In this system, the reader is provided by Impinj and Identix (Core Impinj), the antenna is provided by Laird and Identix, and the reader and printer are provided by Zebra. The label uses Impinj’s E52 Monza5Monza R6 inlay, manufactured by Brazilian suppliers such as CCRR. The RFID project met all expectations, improved production accuracy, and reduced transportation errors.
Engineer Roberto Cordeiro said: “This case shows that RFID technology is mature enough to provide companies with a lot of help.”
(The RFID real-time reading is displayed on the screen)
Cordesro said that Parson has developed a high-level RFID channel entrance. He said: “When the box passes through the channel, the RFID reader can read the tag and identify the items in the channel. To prevent misreading of things outside the channel, we have developed a wave attenuator to attenuate the RFID signal at the entrance and exit of the channel. “
Cordeiro said that innovation and learning are Oxford’s DNA, and the company will use RFID technology in other scenarios in the future. In addition, the solutions developed by Parson are also innovative and reproducible in other market areas. He said: “The adaptability of the process is the key to the success of this project. In this project, the company has hardly changed the existing operating process.”
[ad_2]