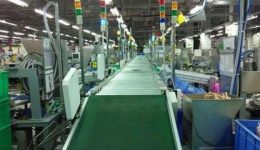
RFID digital smart factory realizes big data interconnection
[ad_1]
With the continuous and rapid development of intelligence, smart factories have gradually become a trend in the industry, and many companies will use RFID for management in their factories. In the manufacturing industry, bar code technology has been widely used, but due to its fragility and low scanning efficiency, RFID electronic tags have essential advantages compared to RFID technology. RFID electronic tags can automatically collect data wirelessly and remotely, and can be repeatedly used for reading and writing. General items can be read and written and collected. They can also be read and written in a mobile state, and the amount of stored data is larger. Obviously, RFID technology is not just a simple replacement of bar code technology, especially its application in discrete manufacturing, which has changed the production and operation methods of discrete manufacturing enterprises.
The RFID digital smart factory refers to a new type of production organization that simulates, evaluates and optimizes the entire production process in a computer virtual environment based on the relevant data of the entire product life cycle, and further expands the entire product life cycle. It is a combination of modern digital manufacturing technology and computer simulation technology, with distinctive features. Its emergence has injected new vitality into the intelligent manufacturing industry, mainly as a bridge between product design and product manufacturing.
Real-time data collection and interconnection are realized in the RFID digital smart factory. On the production line, the production equipment will be equipped with sensors to capture data, and then connect to the Internet through wireless communication, transmit the data, and monitor the production itself in real time. The data generated in production is also quickly processed, transmitted, and fed back into the production process. The factory is upgraded to an intelligent network, which can be managed and adapted, enabling industrial control and management, and limited use of limited resources. Thereby reducing the cost of industry and resource allocation, enabling the production process to proceed. Based on cloud computing technology, such as industrial manufacturing cloud services and industrial data analysis. Through computer networks, radio frequency identification, smart wearable devices and other Internet of Things technologies, we can realize the “interconnection” and “perception” between people, machines, materials, and rings, and create “transparent production and digital workshops” for customers. “Digital Factory” reduces human intervention. Thereby improving the overall coordination efficiency of factory facilities and improving the consistency of product quality.
How to use big data for equipment management? In the past, in the field of equipment management, the wear and tear of equipment during operation will affect the quality of products. Using information technology and Internet of Things technology, through real-time perception of data, identification of product failures, accurate control of all factors in the production process, to achieve intelligent production.
Therefore, the massive data of the MES system directly determines the digitization level of the digital equipment required by “Industry 4.0”. In this regard, the “equipment management suite” can be used as a good reference in the digital factory management solutions for cattle farms. The aspects involved include equipment asset management, equipment maintenance management, equipment preventive maintenance management, equipment performance statistical analysis, equipment output rate analysis, etc., and monitor the operation status and performance of equipment through real-time billboards, and use smart terminals to prompt and alert in advance for maintenance; repairs Work, and carry out statistical analysis and evaluation of equipment performance.
In addition, the use of big data to monitor the production process of all equipment can continuously optimize and reduce production energy consumption in real time during the production process. Big data is the basis for the realization of a digital factory. The RFID digital smart factory uses big data, including data collection, data management, order management, smart manufacturing and customized platforms. Help manufacturing companies improve marketing goals, reduce logistics costs and inventory costs, and reduce production resource investment risks. In addition, the analysis of big data will greatly increase storage, distribution, sales efficiency and reduce costs, and will greatly reduce inventory and optimize the supply chain.
The application of big data in smart factories will bring a new era of innovation and change for manufacturing companies. Based on the information and data of traditional manufacturing management in the past, through the physical data perception brought by the Internet of Things, etc., a private cloud of production data in the “Industry 4.0” era has been formed, and the business innovation of R&D and manufacturing enterprises has been formed. Marketing and management methods. These innovations have brought faster speed, higher efficiency and clearer insights to manufacturing companies.
Deploying the RFID data collection system through the assembly line allows the visualization management of the production line to discover in-progress products and the operating status of the production line in real time. RFID electronic tags are added to each product in production, and the RFID reader installed on the assembly line collects data and uploads it to the system platform for processing in various links after arriving at the station. RFID technology has been widely used in supply chain management, warehouse management, and material management in the discrete manufacturing industry. According to the specific needs of the production line, RFID technology performs visual management of production links and production process control in production control.
[ad_2]