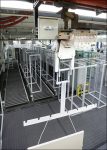
RFID provides visibility of work-in-process for painting factories
[ad_1]
Rittal, a manufacturer of servers, IT equipment, and climate control and power distribution system enclosures, is using RFID technology at the Rittershausen assembly plant to manage the flow of products in the painting process. Through the use of RFID technology, the company can understand the location of the product in the painting process, the amount of paint remaining, and the estimated paint addition time. In this way, the company can obtain the latest information on finished products, solve delays in the painting process and replenish paint in a more timely manner. The technology is provided by the German company IdentPro and uses Xerafy metal tags.
The painting process is carried out in the company’s 85,000 square foot environmentally friendly paint factory. The factory is equipped with a 10 km long conveyor belt to convey products in all painting processes including pretreatment, dipping, and powder coating.
Before installing the RFID system, Rittal did not track specific products during the painting process. This is due to the large number of products on the conveyor system and the long conveyor belt itself. Rittal found it very difficult to track the product being painted at any given time, the estimated completion time, and the amount of paint used. Michael Wack, founder and manager of IdentPro, said that because the company does not track individual products, raw material orders are determined based on historical data rather than actual conditions. In addition, the company does not know the true inventory levels.
In October 2012, Rittal began to cooperate with IdentPro to develop automation solutions and conducted a proof of concept in February 2013. In August of that year, the company began permanent deployment and was put into use in June 2014.
Wack said that some difficulties were encountered during the development of the solution. For example, tags are attached to products hung on conveyor belts on hangers that are exposed to high temperatures and chemicals in the cleaning process. At the same time, the label needs to work in a metal environment, and the software has also encountered some problems. Rittal hopes to manage these RFID location data on the existing SAP system, so the IdentPro software also needs to be integrated with the SAP system.
Wack said that in addition, to prevent production shutdowns, IdentPro also needs to install the technology during normal production at the factory.
During the trial run, the company used a reader and 100 hangers, each of which was equipped with a Xerafy MicroX II RFID tag. The IdentPro software collects data and evaluates to determine whether the reader and tag can operate normally in the harsh environment of the factory. Wack said that the results are very satisfactory.
The final permanent RFID system uses 22 IdentPro identMX readers with integrated antennas. These readers can be installed overhead to read the tag’s unique ID number. These data are interpreted by the IdentPro RFID Control Unit middleware and then sent to Rittal’s SAP system, so that the production stage of each product can be confirmed.
All readers are connected via Ethernet, and the RFID Control Unit middleware is placed on the IdentPro RFID enterprise server to run. The RFID server uses a web-based front-end, can manage and monitor readers, has a reminder function, business logic implementation, and provides information to employees through the SAP system.
These products are moved on a suspension frame under the conveyor belt. Each MicroX II tag of the suspension rack has a unique electronic product code (EPC). Whenever a new product is hung on the suspension rack, employees need to read the tag and link the product serial number to it. These labels can be used in metal environments, with a heat resistance of 250 degrees Celsius, and can withstand the harsh environment of the painting process. These labels can be reused multiple times.
Xerafy’s CEO and founder Dennis Khoo said: “MicroX II’s paint factory RFID tags are customized for the painting environment and have been widely used in this field or similar processes in the automotive industry. In this project of Rittal, general-purpose resistant High-temperature tags are not up to the task. They need RFID tags that can withstand high-temperature environments and be exposed to caustic liquids through multiple cycles.”
The company screwed MicroX II tags onto 1,600 hangers in the factory to ensure that they did not loosen. When an employee places a product on the hanger, he needs to scan the bar ID number on the paper production order and read the hanger RFID tag. In this way, the suspension EPC number is bound to the two-dimensional ID number and uploaded to the SAP software. In this way, when the product moves along the conveyor system with the hanger, the reader will read the tag EPC number. Based on the ID number information read by a specific reader, the Identro software can identify the product location and transfer the data to the SAP system.
SAP software uses these systems in a variety of ways. Rittal can know not only the products being produced, but also the estimated completion time. This information can prevent delays and be shared with customers.
In addition, by understanding the number of products passed in each production stage, Rittal software can also track paint usage and replenishment information. In this way, paint replenishment information can be automatically created to ensure that there is never a shortage of materials during the production process.
The factory has also installed a web-based display (displaying the content of the IdentPro software) so that employees can know the next production order information, and they can make preparations in advance.
If the software detects that there is a delay in the painting process or unexpected product removal from the hanger, the SAP system can also send a reminder to the factory manager.
Wack said: “In terms of work-in-process tracking, the solution performs perfectly. The use of integrated antennas and PoE minimizes costs and installation difficulties. At the same time, the system requires no maintenance, which also reduces TCO costs.”
[ad_2]