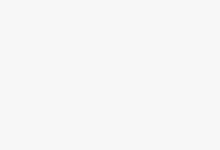
RFID technology makes photoelectric switches more intelligently controlled
[ad_1]
With the rapid development and popularization of industrial automation, there are more and more applications of intelligent automation in industry. Due to the rapid increase in the scale of production and labor costs in the manufacturing industry, the manufacturing industry is gradually undergoing transformation and upgrading. The most basic of building intelligent factories is to realize the unmanned automatic collection and processing of manufacturing information. The emergence of RFID (radio frequency identification technology) makes intelligence. Probability has become a reality, and it has become an important upgrade direction and development trend for the manufacturing industry. RFID technology makes photoelectric switches more intelligently controlled.
Although the photoelectric switch light has advantages such as small size and response time, its disadvantages also limit its development, and many users are troubled by this. The RFID industrial card reader just makes use of its own technical characteristics to make up for the lack of photoelectric switches.
Disadvantages of photoelectric switch:
1. The product information cannot be accurately read on the industrial production line, and it is greatly affected by the environment. Especially when there is a lot of dust, the photoelectric switch cannot obtain the information correctly.
2. It is not resistant to earthquakes, has poor corrosion resistance, and is greatly affected by the environment, so the scope of application is limited.
3. It cannot be used outdoors and in places where it is exposed to direct sunlight or without shading, resulting in harsh conditions when many product lines are produced.
4. Adapt to the environmental temperature difference should not be too large, otherwise it will affect its reading and receiving product information.
When users were troubled by this problem, the RFID production line card reader “grand debut” used its own characteristics of earthquake resistance, pressure resistance, and accurate reading to solve Nantong for users.
How does the RFID production line card reader use its advantages to open a more intelligent, automated, and technological path for industrial production:
1. It can be used in harsh working environments. It can be used in rain, snow, hail and other environments. It can be used normally in high and low temperature environments without affecting its reading speed and accuracy. Available ambient temperature: -20°~70°.
2. Dustproof, waterproof, shockproof IP60 protection grade, strong penetrating ability, stable reading, and extremely low error rate.
3. It can be widely used in various environments, and it is not affected by environmental factors. It can be used in strong light or dark environments.
4. Accurate reading to avoid missing reading when products on the production line deviate during transmission or when special scenes are turning.
The RFID transmission line card reader has fast response, high precision, small size, multiple functions, and strong anti-interference ability. And it can promptly and quickly reflect the information of each station and node to the management background during work, so that it is convenient for management to understand each link of production, the quantity and location of products during production and other information.
As intelligent production brings great benefits to an enterprise, it not only improves productivity and reduces labor input, but also introduces a new type of RFID technology management, which solves many troublesome problems, strengthens management methods, and increases revenue. With the rapid development of the Internet of Things, more and more technologies have emerged. RFID technology has realized the automatic control and management of the production line, breaking through the concept and scope of the traditional production line data collection and monitoring system, allowing the production line, logistics information interaction and intelligent identification, Processing and management, the establishment of an automatic control information database for the entire production process of the enterprise.
[ad_2]