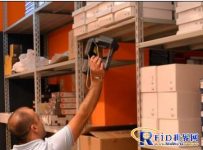
Sicily high-end jewelry supplier uses UHF RFID tags to manage inventory
[ad_1]
Italian fine jewelry retailer Matranga used RFID technology for inventory management in its stores in Palermo and Trapani, Sicily, reducing inventory count times by 96 percent. In addition to the above two stores, there is an underground secure warehouse in Palermo to store additional products.RFIDThe inventory management system tracks each product with RFID tags, which not only improves the efficiency and accuracy of inventory management, but also automatically creates new registration records.
Matranga workers use Nordic ID handheld RFID reader for inventory count
Matranga’s products mainly include high-end watches, jewelry, silver jewelry, porcelain, etc. Its customers include wealthy Europeans including the royal family. The inventory of the two stores in Palermo and Sicily includes 5,000 Rolex watches, 3,000 rings, necklaces, wrists and other jewelry, fine silver, tableware, ceramics, etc., with an average of 4,000 items in the counter, with annual sales of 680 Ten thousand U.S. dollars. Due to the high value of goods sold, it is not surprising that inventory builds up.
In order to prevent the loss of goods and the occurrence of out-of-stock phenomena, retailers need to count all inventory every quarter. Usually, it takes 24 male laborers to complete a single inventory. The traditional inventory counting method is not only time-consuming, but also prone to errors. Furthermore, the manual inventory method has certain internal risks. Because the inventory time is too long, it is easy for employees to take away items without authorization.
In order to improve the management of nearly 12,000 products in stock and prevent out-of-stocks, the company uses RFID tags for tracking. The software system in the RFID inventory management solution is developed and designed by Dynamic ID, and the hardware is provided by RFID Global by Softwork.
The solution includes Dynamic ID’s Jewel-ID software, which records inventory data and associates it with the ID code of the RFID tag, manages all read data, and updates the status of items in real time.
A fixed Feig Electronic MRU200 RFID is installed in each retail storeReaderand a Nordic ID Merlin PDA. The passive UHF RFID tags used in the solution use Alien Technology Higgs-3 chips.
The teller uses a handheld RFID reader to read the information of the jewelry tag
Before the goods are put into storage, RFID tags must be pasted first. The labels were printed and encoded by a Toshiba Tec B-SX4T printer fitted with a Feig MU02 UHF read/write module. The worker stores the batch number and the detailed description of the item in the database of the Jewel-ID software and associates it with the ID code of the RFID.
After adopting the RFID solution, the inventory count can be completed within 2 days. A built-in Feig reader is generally installed in the counter, which reads the tag information and forwards it to the Jewel-ID software. Handheld readers are generally used to read commodities in warehouses or cabinets.
The sold goods need to remove the RFID tag, and at the same time use the fixed reader on the cashier to read the tag information, so as to update the database information.
This technique is also used in the registration of gifts. Newcomers enter the store and set up registered accounts, recording their names and other information in the database. The items they pick will all be recorded in the database to ensure they are not buying the same product.
After the system is installed, under the condition of reducing labor costs and eliminating the phenomenon of out-of-stock, inventory management has achieved a better return on investment.
Passive EPC UHF RFID tags are installed in the goods
After the RFID system was installed, the inventory count time was reduced from 24 hours (three employees, 8-hour workload per person) to one-hour workload per person. With less time for staff in the warehouse, the corresponding commodity risk is reduced. Previously, the company carried out an inventory every three months; after the RFID system was installed, an inventory inventory was carried out every week.
The installation of RFID tags on iron tableware and silver ornaments has certain challenges to ferrous cutlery, which affects the transmission of UHF RFID signals to a certain extent. Therefore, the labels for iron cutlery were chosen to be affixed to the box rather than the cutlery itself.
[ad_2]