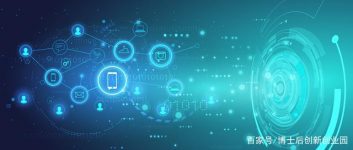
With the help of RFID technology, the workshop-oriented digital twin application focuses on the whole process control of production
[ad_1]
The digital twin refers to the objects in the physical world, and uses digital means to construct an identical entity in the digital world, so as to realize the understanding, analysis and optimization of the physical entity. Since 2019, there have been two hype around A-share concepts. One is edge computing, and the other is digital twins, especially when the Boeing 737MAX8 aircraft suffered a serious crash and the Notre Dame Cathedral was burned in France. Discussions about digital twin technology became more intense. It is a climax. The top ten strategic technology trends released by Gartner in 2019 also include digital twins. IDC predicts that by 2020, the world’s top 600 companies will use digital twins to provide product innovation. MarketsandMarkets predicts that by 2023, the digital twin market will reach $15.7 billion, and will grow at a compound annual growth rate of 38%. The future development prospects of digital twins are broad.
Digital twin drives smart manufacturing
The advantages of digital twins in manufacturing are significant. There is a “1% revolution in the industrial sector” in the industry, that is, global industrial production efficiency will increase by 1% and costs will be reduced by 30 billion. According to Gartner: “By 2021, half of large industrial companies will use digital twins, thereby increasing the effectiveness of these organizations by 10%.”
Through design tools, simulation tools, Internet of Things and other means, the digital twin maps the various attributes of the physical equipment into the virtual space to form a detachable, reproducible, modifiable, and deleteable digital image, which improves the operator’s understanding of the physical Entity understanding. This will make production more convenient and will shorten the production cycle. Of course, digital twins can calculate and summarize some unmeasurable indicators through real-time understanding of target perception data, with the help of empirical model prediction and analysis, and through machine learning, it can also greatly improve the understanding and control of mechanical equipment and processes. And forecast.
Therefore, digital twins can improve the efficiency of design, operation, control, and management by achieving a deep understanding, correct reasoning, and precise operation of objects in physical and logical spaces.
The product-oriented digital twin application focuses on the optimization of the entire product life cycle. For example, AFRL and NASA cooperated to build the F-15 digital twin, based on fighter flight test flight, production, maintenance and repair life cycle data to modify the simulation process mechanism model, and improve the accuracy of aircraft maintenance early warning.
The workshop-oriented digital twin application focuses on the entire production process control. For example, by installing RFID on key tooling, materials and parts, Airbus has created a digital twin of the A350XWB final assembly line, making industrial processes more transparent, predicting workshop bottlenecks and optimizing operational performance.
Virtual verification can simulate products/production lines/logistics in the virtual space to improve the operating efficiency of real scenarios. For example, ABB launches PickMaster Twin, customers can test the robot configuration on the virtual production line, so that the picking operation can be verified and optimized in the virtual space.
Opportunities and Challenges
Digital twins can help us re-examine the potential flaws and innovation space of traditional business models from a new data-driven perspective. Especially with the further integration of traditional modeling and simulation technology with Internet of Things, big data, and artificial intelligence technology, in the industrial field, the use of digital twin technology will greatly promote product design, production, maintenance and repair. change. Based on the advantages of models, data, and services, digital twins are becoming a key technology of the industrial Internet. At the same time, the industrial Internet industry has also become an incubator for the extended application scenarios of digital twin technology, gradually extending from the manufacturing industry to more industrial Internet spaces.
But at present, digital twin technology is still in its infancy in the world. Only some large companies try to use digital twin technology to transform some equipment and processes in some fields and links, such as General Electric, Alibaba, and Microsoft. At present, China’s digitization in industries, cities, and other fields is still relatively weak, and lacks the data foundation and technical support required to build a digital twin. For enterprises, the step-by-step promotion of the digital upgrade of enterprises and opening up the data flow at the business and management level will be the main theme of the current development stage.
[ad_2]