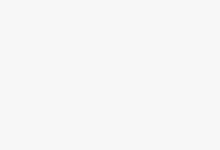
Shuanggou Winery Zhenbaofang Liquor RFID Anti-counterfeiting System Application Case
[ad_1]
The research and development of Shanghai Jijia’s “RFID Second-Generation Liquor Identification Anti-counterfeiting System” and its successful application on the Shuanggou Liquor Jumbofang series of liquors have made Shuanggou Liquor the first in China to complete the production, sales, and circulation of liquor. Companies that use RFID technology for comprehensive management. The launch of this system provides a model case for the innovative application of RFID technology in the anti-counterfeiting and sales channel management of liquor and the entire food industry. It not only represents the development direction of liquor anti-counterfeiting technology, but also represents the application of RFID in liquor and the entire food industry. New breakthroughs and new heights of development. The launch of this product has strongly promoted the transition of RFID applications from closed-loop applications to open-loop applications, and provided an important reference and reference for the advent of the Internet of Things era.
“RFID Liquor Second Generation Identity Recognition Anti-counterfeiting System” is a set of combined computer technology, based on the investigation of production management and RFID technology application status of similar enterprises at home and abroad, in order to meet the needs of production, storage, transportation and sales management in the liquor industry. Network communication technology, automatic control technology and RFID technology are integrated to realize a set of integrated production enterprise RFID comprehensive application program that realizes the automation, visualization, standardization and scientific management of liquor production, warehousing, distribution and sales operations.
The main construction contents of this project include:
1) Combining the characteristics of the main liquor bottle packaging to design an RFID wine bottle label that is easy to install, can not damage the packaging detection and achieve self-destruction when the bottle is opened.
2) Realize the RFID monitoring, detection and control of the main links of the production process, realize the automatic association of the RFID label information of the wine bottle and the RFID label of the box, and realize the effective recording of the information (person, object, time, location, etc.) of the single bottle of wine filling process .
3) Realize the paperless operation of warehouse management processes such as warehouse in, out, inventory, and transfer, and realize the online release of the above-mentioned operation process tasks and the real-time recording of operation results.
4) Realize the controllable production plan based on the combination of orders and actual needs, and realize the recording and tracking of shipments according to confirmed orders and single-bottle-level shipping areas.
5) Realize the online inspection, confirmation and statistical report of product sales channels, and realize the anti-counterfeiting query, information query and channel confirmation of product sales in mobile (mobile phone) and fixed (store terminal) methods.
6) Realize the information statistics, report analysis and online query of the above links, and provide scientific decision-making basis for the company’s raw material procurement, production plan formulation, sales strategy formulation, etc.
7) Realize the RFID system and service system in the liquor industry that meet the requirements of the EPC architecture.
Highlights:
According to the characteristics of liquor production process control, warehousing management and distribution and sales, the RFID field control system is designed in line with the characteristics of various sectors of the industry.
Combine industry characteristics and RFID technical requirements to design and implement RFID middleware system products featuring on-site control and data processing.
The physical network realized by the specific industry application process is refined and formed into a standard and standardized module assembly, and even self-designed and implemented modules are added to form the core system network components.
The methods and results of the specific process software for liquor production, warehousing and sales are modularized and standardized, and are fully in line with the EPC framework to construct comprehensive control and management software for RFID liquor industry applications.
[ad_2]