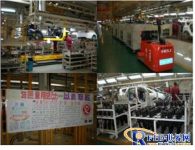
Anhui Jiangqi Logistics Co., Ltd. Vehicle Warehousing and Dispatching System Application
[ad_1]
1 Company profile
Anhui Jianghuai Automobile Logistics Co., Ltd. was established in January 2003. It is controlled by Anhui Jianghuai Automobile Group Co., Ltd., and is an independent legal person affiliated to Jianghuai Automobile Group. Its registered place is Jiangqi Industrial Park, Zipeng Road, Hefei Economic and Technological Development Zone. The company has a registered capital of 68 million yuan and achieved operating income of 680 million yuan in 2012.
There are 164 self-owned transportation vehicles (including passenger cars), 5 parts and complete vehicle storage and distribution centers, self-owned storage area of 32,000 square meters, leased storage area of 32,534 square meters, and entire garage area of 247,000 square meters. The company has 580 employees. , There are about 2,200 registered personnel participating in the company’s daily operations.
The company’s key business affiliates: Anhui Jianghuai Automobile Group Co., Ltd., and its core customer is Anhui Jianghuai Automobile Co., Ltd. It covers almost the entire logistics process of JAC’s product line, including a series of services such as raw material in and out logistics, warehousing and distribution, production logistics, finished product logistics, vehicle management and maintenance, passenger transportation and leasing services.
2 Problems before the implementation of informatization
2.1 Difficulty in tracing system problems
Before the implementation of the informatization project, our company had only a simple dispatch dispatch (S system for short), which was only used to implement simple dispatch management functions. At that time, our company did not have its own system operation and maintenance capabilities, and the software and hardware of the system were managed and managed. Once a problem occurs in the main engine factory, it is difficult to find the root cause of the problem, and to solve the problem, the relevant personnel of the main engine factory must be asked for support. The processing efficiency is low and the authentic control of the system cannot be realized.
2.2 Unable to conduct overall control over the company’s existing vehicle business
Before the implementation of the company’s informatization project, all vehicle warehousing and outgoing operations need to be operated in the OEM of the OEM, and data query and other tasks need to be carried out with the help of ERP. In addition, the dispatching system used by the logistics company itself has a relatively single function, and the lack of management and control of each node of the shipping process makes it impossible to realize the real-time tracking of each node of the logistics business, and lacks the foothold of management.
2.3 Lack of system support for accounting business
The company’s two vehicle divisions have an annual shipping volume of more than 400,000. The cost and revenue calculations must be timely and accurate. Without system support, they can only be sorted and confirmed manually in the form. , The workload is huge, and the accuracy is not high, resulting in heavy tasks for the accounting department.
2.4 System automation is limited
Since the warehousing system is the ERP system of the main engine factory, customized development cannot be realized, and operations such as warehouse entry and exit cannot be realized by automatic code scanning. It is necessary to manually enter the location number and other information, which is not only inefficient, error-prone, but also has a certain lag. .
3 Problems in the implementation of informatization projects
This project is the most powerful information construction work implemented since the establishment of the logistics company, but because of this, the problems and difficulties in the implementation of the project are also proportional to the scope and investment of the project.
3.1 The problem of mismatch between physical logistics and information flow
Since the previous business process of passenger vehicles is relatively stable, there are fewer problems in the process of combing, so the physical logistics and information flow can be basically achieved after the system is online; but the commercial vehicle part is the same due to the new delivery site relocation and the system launch. Time, that is, the implementation of the system’s online work before the process is stable, and a more obvious mismatch has occurred, which once affected the delivery efficiency of the site;
3.2 Interface data transmission problem
There were many data transmission problems during the system launch of the two vehicle projects. Since the logistics company’s warehousing and delivery business needs to interact with upstream OEM ERP, DMS and other systems to ensure that the data between the systems can be shared in real time, more intermediate tables are used as the transmission method during project implementation. In the interface, there is a partial delay in the data transmission process, and even manual intervention is required to complete the transmission of some abnormal data, which is inefficient and causes complaints from on-site operators.
4 Problem handling mechanism
In order to solve the various problems arising from the advancement of the informatization project, the project team took a series of measures to ensure the effective advancement of the project.
Further strengthen the project management mechanism, and output the daily plan of the project team every day. Weekly plan and monthly plan. Regular weekly meeting of the project team will be held every week to report on the progress of the project and the progress of problem solving to ensure that the project can be controlled as a whole during the progress of the project;
For the situation that the existing system process of the commercial vehicle system cannot be completely matched with the actual business logistics after the commercial vehicle system is online, the project team organizes a special process team to reorganize the commercial vehicle process and confirm the information, and arrange for the project team to conduct a second time after reporting to the company’s leadership for approval. Software development to ensure the consistency of information flow and actual logistics;
Due to the lag of the interface method of the intermediate table and the difficulty of tracing problems, the information department of the upstream OEM negotiated to change the existing interface method to webservice to ensure the timeliness of data interaction and the traceability of interface problems sex.
5 Benefit analysis
5.1 Technical level
5.1.1 This project is based on the operational requirements of multi-base, multi-platform, multi-warehouse, and multi-transportation combined transportation, which achieves the purpose of integrating available resources and reducing logistics operation costs to a greater extent.
5.1.2 The TMS system interacts with the GPS platform for data, which can track the status of the cart in real time, and replay the trajectory to view the trajectory of the vehicle. When the vehicle enters the 20km range of the destination, the system can automatically determine the arrival and reduce the overdue rate.
5.1.3 The vehicle storage management system is the WMS system, which automatically allocates and releases storage spaces for commercial vehicles through the system’s actual vehicle scanning code entry and exit.Sync throughRFIDRadio frequency identification technology binds the circulating driver to the commercial vehicle and realizes the traceability of the process.
5.1.4 In terms of loading site management, implement the management measures of the carrier’s reporting of capacity resources in the system, requiring that the capacity be reported one day in advance according to the shipping plan, so that the three-day rolling is carried out, and the time axis of the check-in and out-of-warehouse operations is integrated. Optimize the order of loading and unloading of dispatching pallets, and realize the reduction of management difficulty by means of system solidification.
5.1.5 BMS, or billing management system. In the logistics industry, there are generally weak sites where the business is completed first, the invoice is issued the next month, and the third month is settled. How to accurately and timely verify the cost and benefit of logistics enterprises and provide a basis for business decision-making has always been a common problem that plagues logistics enterprises. BMS realizes the pre-settlement management that starts to calculate the cost and profit as soon as the commodity truck is out of the warehouse, combined with the control of management index items, can provide company decision makers with more intuitive and accurate business index data. In addition, in response to the need for refinement and sinking of the company’s financial management, with internal secondary accounting as a breakthrough point, a series of accounting statements have been developed, which greatly reduces the workload of accounting personnel and effectively improves the accuracy of accounting data. Sexuality and timeliness.
5.1.6 Realized the recovery and redistribution of idle orders. The overall OTD is guaranteed. In terms of order management, vehicle logistics companies have always had problems. Due to the lack of effective means, the carrier’s pressure plate at the front end of the order, the disorder of the order distribution of logistics scheduling, the tracking of the carrier’s response after the order distribution, and the corresponding assessment The problem has always existed, which directly led to the low efficiency of logistics companies’ order OTD. According to this, a special solution was established. Through a variety of management methods, including the automation of order distribution carriers, the logistics company’s scheduling was established under the carrier’s puzzle business model. The review and return mechanism includes the push of early warning information for urgent or near-expired orders through the means of reports and messages. Under a variety of business models, it provides companies with a variety of relatively effective management methods and IT solutions.
5.1.7 Realized real-time query of key nodes based on orders from multiple parties such as OEMs, carriers and distributors. Reached the leading level. The rapid and timely sharing and transmission of information is the basic demand of logistics companies. For vehicle logistics, OEMs, carriers, distributors, and logistics companies pay attention to different points. OEMs pay more attention to the two ends of the business chain ( Warehouse storage and dealer collection), carriers pay attention to the stowage, route and arrival of vehicles, dealers pay attention to quality and delivery time, and logistics companies as a whole guarantee the smoothness of the entire business chain. After detailed investigations and visits, the project team refines the nodes that each role focuses on, and conducts targeted IT planning and design to ensure that each management role can receive effective information and effective support and reasonable suggestions for management changes.
5.1.8 Help the OEM to transform from a pure logistics manager to a fourth-party logistics manager. To achieve an innovative transformation in the operating model. With the rapid development of the logistics industry, the limitations of the third party will become more and more obvious, and the transition to the fourth party role has become a new topic. Logistics companies not only need to focus on themselves, but also need to focus on a wider range of industry chains. Companies, OEMs, third-party logistics companies, and IT information centers solve current problems from multiple perspectives. According to this trend, logistics companies actively promote the vertical integration of business chain information, and IT product chains cover the entire vehicle transportation. The comprehensive business platform and supporting solutions covering all links such as component inbound transportation, spare parts transportation, spare parts warehousing, vehicle warehousing, and vehicle transportation can greatly support the transformation of third-party logistics to the fourth party.
5.1.9 Achieved coordinated operation. Incorporate OEMs, marketing companies, warehouses and carriers into one platform to operate together. Simple third-party logistics management can solve limited problems. This system has designed an information platform suitable for each role in the relevant business chain. It makes the information channel more smooth through standardized interfaces or directly using the same platform. The IT design with industry-specific integrated business roles ensures the integrity and timeliness of the logistics information chain, and greatly improves the ability of enterprises to integrate upstream and downstream resources.
5.2 Benefit analysis
5.2.1 Optimize management
Through the implementation of the vehicle logistics information project of the factory logistics company, the management requirements have been implemented, the management specifications have been implemented, the entire process of the entire vehicle from warehousing to transportation is fully controlled, and the initiative to manage the entire business operation has been fully obtained. The responsibilities and requirements of each link are clear, the assignment of tasks is clear, and the business development is accurate and orderly. The previous unorganized situation due to unclear responsibilities was basically eliminated. A healthy competition mechanism was introduced in the project, which reduced management risks and also enabled the suppliers to give full play to their respective advantages, achieving a win-win situation for multiple parties and forming a work situation of unity and cooperation.
5.2.2 Improve efficiency:
With the help of project implementation, the business management process has been fully implemented, which has improved the overall vehicle storage and transportation efficiency. With the help of the information system, the business management department can conveniently, quickly and accurately issue various instructions, and at the same time can obtain the status of business operations in a timely manner and make adjustments to the overall operation, which greatly improves the operational efficiency of the management department. With the help of business processes and systems, suppliers operate in accordance with specifications and requirements to reduce ambiguity and repetition at all levels, which not only greatly improves the efficiency of on-site operations, but also completes various assessments that could not be achieved before. Require.
5.2.3 Reduced management and assessment costs:
Through RFID scanning and other equipment, all information points in the business process such as warehousing operations, sorting and outgoing operations are automatically collected, and assessment reports are formed, which constitutes effective data support for external and internal assessments, reducing or eliminating manual statistical processes A lot of cost wasted in the process.
5.2.4 Improve the accuracy of ready-made management:
Through the reorganization of the warehousing, picking, and outgoing processes, compulsory system scanning management is used in the warehousing, outgoing, spot inspection, and shipping links, distribution in the warehouse area, vehicle picking, outgoing, lane inspection, and shipping The scanning light business stage effectively prevents the occurrence of human error.
5.2.5 Improvement of accounting efficiency:
The system automatically settles income and costs, and supports a variety of different settlement methods, quickly and promptly provides various financial statements that support the company’s secondary accounting, and improves the efficiency and accuracy of financial accounting.
5.2.6 Reduce waste:
From the original passive repetitive investment and construction every year, it has been transformed into a one-time investment to benefit every year. The business management department can be freed from the increasingly complicated things, and have manpower and time to do more valuable work and other pioneering businesses. The number of workers used by suppliers is declining on the premise that they are qualified to complete the same amount of business.
6 Next work plan
6.1 Further improve system construction
Informatization work cannot all rely on technical means to support, and it is necessary to adopt corresponding management systems to jointly promote the improvement of the company’s informatization level. System construction will be one of the key tasks of Anhui Jiangqi Logistics Co., Ltd. in 2014 for informatization, and it will continue to establish and improve informatization management systems, norms and processes.
6.2 Strengthen informatization planning
In 2012, the company compiled the “Twelfth Five-Year Plan for Anhui Jiangqi Logistics Informatization” to guide the company’s informatization work during the twelfth five-year period. Today, two years later, Anhui Jiangqi Logistics Co., Ltd. basically carried out informatization work in accordance with the ideas in the “Planning”, but in terms of details, it is necessary to have a phased summary of the “Planning”, and the company’s current informatization work exists. A clear and objective understanding of the problems of the issue requires a further review of the “Plan”. On this basis, the informatization work plan for this year in the evening will ensure that the informatization work can be promoted more effectively.
6.3 “Unified Platform, Standardized Deployment, Standardized Application”
Although the vehicle informatization work has been implemented and is operating stably, there is still some work that needs to be followed up in the later period. The focus is on “unified platform, compliance deployment, and compliance application”, how to improve customer service levels and carrier logistics operations Efficiency, integrating logistics resources, reducing logistics costs, and establishing a unified logistics dispatch center is a challenge to the later information system.
[ad_2]