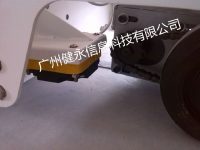
Application scheme of RFID technology in AGV site positioning navigation and dispatching system
[ad_1]
To understand the application of RFID in AGV automatic transport vehicles, we must first understand what AGV is. AGV trolley refers to a transport vehicle equipped with electromagnetic or optical automatic guidance devices, capable of traveling along a prescribed guidance path, with safety protection and various transfer functions. As an unmanned industrial handling vehicle, high-speed, high-efficiency and accurate positioning are very important for the AGV trolley transportation system. RFID has the advantages of non-contact and non-line-of-sight. The use of RFID to control the positioning of the AGV trolley, compared with other positioning methods (inertial positioning, ultrasonic positioning, laser positioning, etc.), is not only simple in structure, low in cost, and easier to achieve accurate positioning.

Figure 1 Installation diagram

Figure 2 AGV card reader
The specific application of Jianyong RFID technology in the AGV site positioning navigation and dispatching system
Automation, informatization, and intelligence have become the needs of the development of the times. Since the beginning of the 21st century, wireless technology and computer technology have continued to develop in depth, and the Internet of Things industry is booming. RFID radio frequency identification is a non-contact automatic identification technology, which automatically recognizes the target object and obtains relevant data through radio frequency signals. The identification work does not require manual intervention and can work in various harsh environments. With these characteristics of RFID, the use and value of RFID positioning technology integrated in AGV are very great.
1. How to use RFID in AGV
The AGV is controlled by PLC, and the car has a wireless communication system that can communicate with the upper computer wirelessly, report its running position and working status, execute the instructions of the upper computer, and transmit the working beat and workload to the upper computer in time; the AGV uses RFID Read the ground signs and make corresponding actions (change speed, steering, positioning and parking, etc.); AGV card reader JY-L8900 is installed on the bottom of the AGV body, and RFID landmark card JY-T330 is installed at the node position on the ground, and given The landmark card on each node has an ID number and definition. For example, node A represents the AGV turning, which is represented by ID number 00001. Once the transport vehicle passes by A, the AGV reader will read the electronic tag ID at A According to the read data, PLC makes the trolley make corresponding actions, so as to realize the function of AGV dispatching system and station positioning function. As shown in the figure:

Figure 3 Schematic diagram of the application of RFID positioning technology in AGV
The PLC can control the car according to the pre-set program, or upload the data to the upper computer, and then control the car according to the instructions of the upper computer.
2. The advantages of applying Jianyong Technology’s long-distance and high-speed RFID positioning technology
(1) Strong penetrability, can easily penetrate the object to read the tag without affecting the reading distance;
(2) Strong anti-interference. Other frequency band technologies are susceptible to environmental humidity, noise, oil pollution, electromagnetic fields, strong vibrations and other factors. It is easy to read the unstable card and cause data packet loss or inability to read the label, and Jianyong AGV card reader It is not easy to be interfered, and these problems can be avoided well;
(3) The card reading distance is moderate and stable. To achieve accurate parking, the AGV sensor (ie card reader) must have a stable and reasonable card reading distance. Reading distance too close means that the AGV chassis needs to be very low, which undoubtedly increases the equipment failure rate; too far reading distance means inaccurate positioning, the robot has read the tag and stopped before the station, and Jianyong AGV card reader JY-L8900 can be accurately controlled at 5-10cm. For some special requirements, the card reading distance can also be set to 15-20cm;
(4) The card reading speed is fast, and the stable reading speed of the label is more than 2 meters per second. When the AGV is accelerating, the reading of the label will not cause the ordinary RFID reader to read the electronic label.
[ad_2]