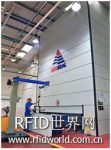
British mechanical seal manufacturer AESSEAL’s RFID technology test results are good
[ad_1]
British mechanical seal manufacturer AESSEAL has been paying attention to the development of RFID technology in the past few years. They are considering using RFID technology to track the process of products being shipped from Asia to distribution centers in the United Kingdom and the United States. Last month, AESSEAL established a new EPCglobal RFID test center in Winsford, UK to evaluate the application of RFID technology. AESSEAL tested EPC Gen 2 RFID tags and readers in a warehouse-like environment to determine whether RFID can speed up product reception and positioning. During the test, the successful tag reading rate was 95.5%. Stuart Welsh, IT director of AESSEAL, said that the result is very encouraging.
The center was established on November 15 and is managed by Intellident. The purpose of the center is to help British companies (such as AESSEAL) understand the commercial benefits that RFID can bring, including cost savings, increased accuracy and efficiency.
The seals and parts produced by AESSEAL are sold to major chemical plants around the world. The vast majority of products are low-margin, and the price range is between $10-$20. These products have large volumes and quick turnover. A distribution center can handle thousands of pieces every month. Welsh said that if employees are unable to locate a certain type of product, they may think that the product is out of stock, and customers who are unwilling to wait will turn to their competitors.
AESSEAL currently uses barcodes to identify and track products. In China, product manufacturers affix a barcode on each product, and the barcode corresponds to the serial number of the product in the AESSEAL back-end database. When the product arrives at the distribution center, the employee scans the bar code and creates a product record. However, the line-of-sight scanning required by barcodes makes the entire scanning process time-consuming; checking a large order can sometimes take several weeks.
To this end, Welsh spent three years looking for a system, hoping to improve the visibility of the product’s circulation between manufacturers and distribution centers, while also improving the efficiency and accuracy of supply chain management. RFID applications can eliminate manual scanning. Welsh explained that workers only need to pass a forklift loaded with RFID-labeled products through an RFID portal reader, and the system can record all products.
AESSEAL Logistics Distribution Center
In the test, AESSEA sticks RFID tags to metal blocks similar to the company’s seal products. These metal blocks are placed in cardboard boxes, and the center researchers stack these cardboard boxes together and pass through a series of RFID door readers to imitate typical practical application scenarios. “In addition to testing the speed and accuracy of reading, we also test the direction (in or out of the warehouse),” he said, “all reading rates reach 100% accuracy.”
According to Welsh, the laboratory environment is similar to the transportation environment of AESSEAL products. “The temperature in the laboratory is very low, there are liquids and metals; the staff uses actual products to make the application more intuitive.”
The goal of the measurement center is to assist the operation and technical staff of the British company to choose the best way of RFID application in order to obtain the expected results; the center will help any organization in any industry to develop RFID applications in the most effective way.
Welsh said that the center experts provided realistic application methods, suggesting that they should not expect RFID to be a panacea, but should adopt more practical application steps.
AESSEAL plans to analyze the current cost of using barcodes, including labor costs, lost parts and losses caused by out of stock, to compare the investment costs of RFID systems. With the results of the test center, AESSEAL can return to the warehouse to discuss the feasibility of using RFID tracking in a real environment.
If AESSEAL finds that RFID technology is cost-effective by reducing labor and lost item costs, the company is expected to install this system in two distribution centers in the UK in 2008.
In the end, AESSEAL hopes to use RFID to track assets in the supply chain and distribution centers. Not only will labels be applied to product packaging, the company also plans to apply labels on the shelves of the distribution center to help employees quickly locate products. AESSEAL is also considering using this technology to identify warehouse staff.
[ad_2]