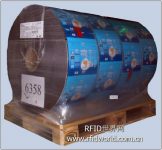
Coffee maker Lavazza uses RFID to track packaging material rolls to improve operational efficiency
[ad_1]
Italian coffee maker Lavazza and its packaging supplier Goglio Cofibox implemented an RFID identification system to automatically replenish packaging material rolls (used to produce Lavazza products) to improve the traceability of packaging materials.
According to the two companies, this system-using EPC Gen 2 passive UHF RFID tags-enables the just-in-time JII shipment of rolls of printed packaging materials produced by Goglio Cofibox and the Lavazza plant in Turin Automation of material roll reception. This technology reduces Lavazza packaging inventory and inventory space, and provides the company with real-time visibility of inventory, said Fabio Marzorati, an industry engineer at Goglio Cofibox.
Lavazza processes the packaging materials into bags, which are then filled with coffee. The law requires coffee companies to monitor the quality of packaging materials to ensure that customers buy high-quality coffee. Due to the limited life of the materials on the shelf, the company must use the materials according to the first-in, first-out principle. Therefore, companies need to track materials in a more efficient way than manual systems.
The company uses an RFID system to track pallets loaded with rolls of packaging material. During the initial testing phase of the project, the partners also tracked the packaging material rolls used by a specific coffee brand-Allegro. According to the company, the purpose is to test item-level applications. Each Allegro material roll weighs 135 kg and has a diameter of 60 cm. Four rolls are placed on one pallet.
Rolls of packaging material loaded on pallets, stretch film with RFID tags
Before implementing the RFID system, Lavazza was unable to understand the company’s order processing status at Goglio Cofibox. Conversely, packaging suppliers have no way of knowing whether Lavazza has received the material rolls they sent, or the coffee maker’s stock of material rolls. In addition, every time Lavazza needs additional materials, he has to place an order manually.
In order to solve these problems, the two companies installed an RFID system in April 2009 and fully implemented it in September. During the single product testing, when the packaging rolls were completed, Goglio Cofibox used a Toshiba RFID printer and encoder to print and encode RFID labels with UPM Raflatac inlays. Workers stick labels on the inside of the core paper tube of each packaging roll.
After a machine wraps the pallet with four label rolls with stretch film, the worker puts another two adhesive RFID labels on the plastic stretch film of the wrapping material roll, so that the pallet forms a rectangular package (another A label is directly attached to the short side of the pallet rectangle, so that the pallet can be identified when the labelled stretch film is removed). The company pastes the label containing the UPM Raflatac Hammer inlay on the roll and encodes a global trade serial number on the label. The pallet label adopts UPM Raflatac DogBone inlay and is coded with serial shipping container (SSCC) code.
Once the pallet is wrapped and labeled, workers drive a forklift to move it to the company’s storage area. When the pallet passes by an Impinj door reader at the gate of the storage area, the label is read, the SGTIN and SSCC codes of the pallet and the packaging roll are recognized, and the system automatically upgrades the Goglio Cofibox inventory level.
Currently, the company only uses labels at the pallet level and no longer applies labels to single rolls. Goglio Cofibox labels approximately 30 new pallets per day and will maintain an inventory level of 150 labelled pallets. Lavazza stores approximately 3000 wraps of stretch film. By mid-December, all inventory pallets were labeled.
When the material is loaded onto the truck and ready to be transported to Lavazza, the pallet RFID tag is read again. The green light is on, indicating that the forklift operator’s goods have been identified and the system has located the relevant bill of lading. At this point, the system can also send bill of lading data electronically via the Internet.
When the material roll arrives at Lavazza, the worker uses a handheld machine to read the RFID tag on the outside of the pallet’s stretch film, and then moves the pallet to the storage area. Lavazza chose to use a Psion Teklogix handheld in this step. Cargo and traceable information are automatically entered into the logistics dashboard-a web application shared by the two companies.
“It provides real-time visibility and tracking data of the cargo flow,” Rizzi said.
When Lavazza produces coffee and needs packaging, the company uses an RFID system to take out the packaging that has been stored for the longest time. An employee drives a forklift to take a pallet, and then uses a handheld to read the tag. The system recognizes the material rolls and changes their status to “sent to production”. The pallets are then placed on the connected carts and sent to the production area.
Sometimes, the Lavazza production line does not need to use all the material rolls on the pallet and sends the rest back to the warehouse. However, the stretch film and the RFID tags on the film have been removed and discarded. In this way, workers use handhelds to read the RFID tags returned to the pallet. Lavazza warehouse managers must manually enter the specific number of the volume before returning the pallet to the warehouse.
According to Rizzi and Marzorati, the system has provided Lavazza and Goglio Cofibox with nearly 100% inventory accuracy, which greatly saves time because the material rolls are no longer counted by hand. Moreover, Rizzi claims that Lavazza manages its inventory more effectively due to its real-time view of inventory, and in fact the company has reduced its overall inventory level. In addition, the shipping and receiving process is more reliable.
ID Solutions was responsible for project integration and developed a logistics dashboard specifically for the project. The dashboard formats the data according to EPCIS standards so that the two companies can share information.
[ad_2]