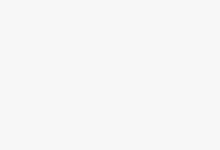
Intelligent Management System for Automobile Transportation of Shandong Rizhao Port Co., Ltd. No. 3
[ad_1]
1. Background
At present, the GPS freight management system and the reverse transportation management system of the three companies lack effective system integration, and the system functions are scattered. Some functions cannot meet the actual operation process and actual field operation requirements, which have great limitations on operation efficiency; due to some historical reasons, GPS The types of hardware platforms are different, the compatibility is very poor, and the software platforms are not unified, independent and scattered, and the business is relatively independent, and cannot be effectively integrated. It causes a lot of troubles for the staff and obstacles to the further integration of other systems in the future. Therefore, , We use the existing software and hardware resources and the technology we have mastered to integrate the system to make the GPS hardware equipment independent of the software platform, and the staff only need to use a set of software. In view of the shortcomings of the above systems, we added loaders tracking management and area closed management, as well as the upgrade and transformation of the weighing room management. The system requires that the driver does not get off the car, the weighing room is unmanned, the area is closed, and the field operation is automated. We propose A new business technology program.
Two, business process
The existing automobile transportation system uses bar code dispatch forms to connect all links of operations in Hong Kong in series. In order to improve work efficiency, reduce work accidents, and protect cargo safety, new equipment and technology (focusing on RFID radio frequency card technology) are introduced on the basis of the existing system to realize the adjustment and optimization of the entire work process and work methods.
The automobile freight management system can be broken down into several links: vehicle assignment, port entry and exit verification, room inspection, enclosed area verification, and yard operations. The overall flow chart is as follows:
2.1 Port entry and exit management
Inbound process Outbound process
1) Before the vehicle arrives in Hong Kong, the barcode dispatch form must be printed on the e-commerce platform in accordance with the original mode as a proof of delivery for the arrival in Hong Kong. Install radio frequency card scanning equipment at a fixed position on the entrance of the port gate to read and write the radio frequency card.
2) When the vehicle comes to the entrance, the driver will hand the dispatch ticket to the guard, scan it with an infrared scanner to obtain the dispatch ticket information. The guard checks the information of the dispatch order, and if it is legal, perform the association operation between the radio frequency card and the dispatch order; if it is not legal, check the vehicle.
3) After the doorman completes the association of the dispatch ticket and the radio frequency card, the card is issued to the driver. The driver puts the card in a fixed position. The doorman let it through.
4) Install radio frequency card scanning equipment at the fixed position of the gate. When the vehicle leaves the port, scan the radio frequency card to obtain the current operating status of the vehicle. The system judges whether the weighing has been completed. If the vehicle has been weighed, the system will give a release prompt and the guard will retrieve the radio frequency card and dispatch order; if it has not been weighed, the system will give an alarm and prohibit the release. The security personnel can check the vehicle before leaving the port.
2.2 Enclosed area inspection
Entrance to closed area Exit to closed area
1) The third company re-planned the entire operation yard to form several closed areas. Each area has a specific entrance and exit.
2) Install barrier gates, LED display screens and radio frequency card scanning equipment at the entrance of the enclosed area. After weighing the vehicle, it came to the entrance of the enclosed area to scan the radio frequency card. The system judges whether the stack location corresponding to the vehicle plan number is in the area based on the obtained information. If it does not meet the requirements, the gate will not be turned on and the LED display will give a text prompt. If the conditions are met, the system judges whether the vehicle has been weighed once. If it has not been weighed, the LED display will give a prompt and the vehicle will return to weighing.
3) After the vehicle passes the verification, the barriers are automatically opened and the vehicle passes.
2.3 pounds house check
One-time weighing process
Second weighing process
1) After the vehicle enters the port, go to the weighing room to carry out the weighing operation. The weighing room is equipped with radio frequency card scanning equipment, LED display screens, infrared reflectors and other equipment to ensure the legality and safety of the weighing operation.
2) When the LED display prompts the vehicle to weigh, the vehicle can be weighed. If the vehicle is not fully weighed, or the following vehicle deliberately weighs, the infrared reflector detects the signal and prevents the system from proceeding to the next step, and the system issues an alarm.
3) After the vehicle is fully loaded, the system automatically scans the radio frequency card to obtain operation information, and the system automatically analyzes whether the vehicle operation is legal. If the vehicle is weighed once, the system judges whether the vehicle has been verified when it enters the port. If it is not verified, the system will give an alarm to prevent the vehicle from continuing to weigh, and must return to the gate to re-verify. If the vehicle is weighed twice, the system determines whether the vehicle has been verified and loaded in the yard. If it is not verified, the system will give an alarm to prevent the vehicle from continuing to weigh, and must return to the yard to re-verify. If the vehicle is no longer loaded due to special circumstances, the system will give an alarm and the duty inspector will perform the operation of invalidating the tare weight.
4) If the weighing data is legal, the system automatically saves the weighing data, and the system displays the weighing information on the LED display and controls the barriers of the gate where the weighing is to be raised. The driver can drive the vehicle away from the weighing scale to complete the weighing operation.
5) If the weighing data is illegal, such as abnormal wagons, insufficient planned volume, etc., the system will issue an alarm and the weighing software will not be executed. On-site duty inspectors or central monitoring personnel handle the corresponding alarms; if on-site drivers have any questions, they can communicate with on-duty personnel through the intercom system.
6) If the weighing data is illegal, such as abnormal wagons, insufficient planned volume, etc., the system will issue an alarm and the weighing software will not perform weighing operations. After receiving the alarm, the on-site duty inspector or central monitoring personnel will conduct manual intervention to deal with the problem; if on-site drivers have any questions, they can communicate with the on-duty personnel through the intercom system.
2.4 Yard operations
1) The operating vehicle receives the radio frequency card.
2) The central control room sends operation instructions to the loader according to the issued plan.
3) The loader arrives at the designated job stacking position and waits for the job. The dump truck receives the operation instruction and enters the designated starting point for loading.
4) The loader automatically scans the radio frequency card remotely before loading the dump truck. After success, start loading. (As long as it is a coming car, it is considered legal).
5) The operation of Jishu Port has been matched with the operation plan at the entrance. Reverse operations are matched to the relevant plans only after scanning at the loading location.
6) After loading the truck, the trucks from Jishu Port will go to the weighing room to weigh the trucks, and the yard operations will be completed. If weighing is required for the backhaul operation, go to the weighing room for weighing, and proceed to the next step after weighing.
7) The dump truck arrives at the unloading point and unloads the truck. At this time, it is judged whether the unloading is legal according to the plan information, stamping position information and real-time position information bound to the vehicle during loading. If it is legal, a legal unloading record is generated, and if it is illegal, an illegal unloading record is formed.
8) After unloading is successful, return to the loading location to continue loading.
2.5 Operation process of vehicle terminal
1) Detailed explanation of the backward transportation process:
This information is triggered by the touch terminal. After the driver logs in, the background monitor will issue work instructions to him, and the terminal will receive plan information and related dispatched vehicles. The driver scans the corresponding vehicle for loading during the operation. After the confirmation is successful, the server returns a confirmation message, which represents the beginning of loading (the voice prompts the number of vehicles in a certain fleet to start loading). After unloading the truck, judge whether it is in the stacking position. If it is successful, add the vehicle to the waiting vehicle list again (voice prompts can be made, and the number of vehicles in a certain fleet unloaded successfully), which means that the loading and unloading of the truck is over.
a. During the driving of the dump truck, when we use GPS vehicle speed to control the misoperation of the weighing equipment, the equipment does not send weighing data.
b. When unloading a truck, the server first judges whether the received unloading data is valid, and first judges the unloading interval according to the time interval (due to the need to send multiple data when unloading a nickel mine, etc., take the maximum value). It is judged whether it meets the unloading weight according to the type of goods in the plan. If it does, it will be completed in the end stack position in the plan. If it is correct, it will be inserted into the database and continue to wait for loading; if it is wrong, then To unload the truck abnormally, human intervention is required, and the second truck cannot be loaded again. The process is as follows:
Loader driver login system
After successful login, wait for the job instruction
Receive the operation instruction, draw the operation stomping position
Arrived at the designated stomping position
After successfully reaching the stamping position, scan and load the arrived dump truck
After the dump truck is successfully unloaded, continue to the designated stomp for scanning and loading
After the plan is completed, the loader continues to wait for instructions
2) The process of collecting and dispersing ports is as follows:
The loader receives the instruction to reach the designated area, scans the incoming vehicles, and after success, displays the information of the vehicle and loads it.
Loader driver login system
After successful login, wait for the job instruction
Receive the operation instruction, draw the operation stomping position
Arrived at the designated stomping position
After successfully arriving at the stamping position, scan and load the arriving vehicles
After loading the vehicle successfully, the vehicle entering the port will leave the enclosed area for a second weighing
The above two processes will be integrated in a system terminal for easy operation and use.
Three, system design
3.1 Port entry and exit management
1) Existing port entry and exit management is verified using bar code dispatch orders. Now the introduction of radio frequency card technology in conjunction with the bar code dispatch form will simultaneously verify the legality of the vehicles arriving in Hong Kong.
2) The software and hardware involved in port entry and exit management are as follows:
Radio frequency card scanning equipment. Radio frequency card scanning is used to identify the identity of the vehicle, and to mutually verify the information of the bar code dispatch order to ensure the legitimacy of the vehicle.
Infrared scanner. Scan the barcode to dispatch the car to get the job information.
LED display. Give text prompts to the vehicle.
Barrier gates. The barrier gate is associated with the host and automatically controls the opening and closing of the railing.
Software function. Transform the management software, add the radio frequency card identification function on the basis of the bar code management, and automatically associate the radio frequency card and the bar code information to complete the subsequent operation process.
3.2 Closed area management
1) Closed area management is a new management link added to the automobile transportation system, mainly to achieve cargo safety and improve the order and efficiency of the operation site.
2) The software and hardware involved in closed area management are as follows:
Radio frequency card scanning equipment. Radio frequency card scanning is used to identify the identity of the vehicle and obtain vehicle-related information.
LED display. Give text prompts to the vehicle.
Barrier gates. The barrier gate is associated with the host and automatically controls the opening and closing of the railing.
Software function.Obtain the information of the working vehicle and determine whether the vehicle is weighed to meet the conditions for entering the yard
3.3 pounds house check
In order to realize automatic weighing of the vehicle weighing, the following technical keys need to be handled:
Verification of the legality of truck operations
Identification and comparison of vehicle information
Collection and analysis of weighing data
Information interaction and guidance
On-site real-time monitoring
3.3.1 Overall architecture
The system is mainly divided into two parts: weighing room automatic weighing subsystem; central monitoring and management subsystem.
The weighing room automatic weighing subsystem is mainly composed of: electronic platform scales, infrared detection, automatic gates, RFID radio frequency card scanning equipment, barcode scanners, small dot matrix printers, LED display screens, voice prompts, on-site monitoring computers and other hardware devices .
The central monitoring management system is composed of hardware devices such as cameras, transmission equipment, data servers, video storage servers, and central monitoring computers.
Set up a monitoring computer for each weighbridge on site to interact with related equipment and collect equipment information and vehicle weighing information in real time.
Set up a central monitoring computer for the inspection team leader, switch the images of the designated weighing room at any time, view the live situation on the spot, and query and handle the problematic vehicles.
3.3.2 Function Module
The weighing room realizes automatic weighing by using computer, network, video monitoring and other software and hardware technologies to establish an automatic weighing system integrating image, sound, data, and field equipment control. The system can be divided into the following sub-modules:
1) Vehicle identification verification module
The vehicle identification and verification subsystem is an important part of the automatic weighing system. Whether the cargo safety and vehicle legality of automobile transportation operations can be realized is the most critical step.
The vehicle identification verification subsystem mainly realizes the collection and comparison of vehicle information through radio frequency card scanning. After the vehicle is weighed, the radio frequency card device automatically recognizes the vehicle number corresponding to the vehicle radio frequency card and the vehicle dispatch information corresponding to the vehicle, such as the plan, consignee and consignor, and vehicle number, and the system judges the legality of the vehicle operation based on this information. If the conditions are met, proceed to the next step. If not, an alarm will be given and the relevant personnel on duty will deal with it.
2) System monitoring module
The system monitoring module is divided into on-site monitoring layer and central management layer. The on-site monitoring layer guides and intervenes in the vehicle weighing process by collecting on-site equipment status information and real-time images; the center management layer uses the status information returned by on-site monitoring to query, verify, and process the weighing data to ensure the correctness of the operation data.
The system monitoring module uses the multi-angle camera installed in the weighing room to monitor the entire weighing process of the operating vehicle; monitor whether the driver has illegal operations on the spot.
The image screen of each weighbridge is integrated into the software interface of the corresponding on-site monitoring computer. The duty inspector can monitor the operation of the vehicle according to the screen; integrate all the images of the weighbridge into the software interface of the central monitoring computer, and the inspector can always Switch the scene operation image of any weighing room, view and process the operation process.
3) Boot interactive module
The guiding interaction module is mainly to play the function of the weighing service window, provide a friendly interactive interface for the truck driver, and give the driver a clear reminder of the current operation situation and information.
The guiding interaction module is composed of LED display, voice intercom, loudspeaker, etc. The LED display screen displays the relevant prompt information to the driver in accordance with the prescribed weighing process, such as: the vehicle weighs on, the driver please get off, the current weighed weight, the abnormal tare weight, etc. At the same time, the system cooperates to give certain voice prompts.
Set up an intercom system to facilitate information communication between drivers and on-site personnel.
4) Weighing control module
The weighing control module can control the actions of the peripherals (LED screen text prompts, voice device prompts, the lifting of barriers of the gate, etc.) and collect the status of the peripherals through the communication interface and I/O control interface between the on-site monitoring computer and the peripherals And information (collecting vehicle operation information through infrared barcode scanner, collecting weighing data of truck scale control instrument, obtaining license plate number, infrared beamer status). The system processes and judges the collected information, and guides the vehicle into different weighing procedures according to different judgment results.
After the vehicle is weighed, the weighing control module detects whether the operating vehicle has been fully weighed through the infrared beamer, and gives an alarm when there is a weighing condition; the system automatically collects the weighed weight of the vehicle, and then analyzes the weight category (tare weight or gross weight) , And carry out the corresponding illegal weight judgment processing; if the tare weight is abnormal, the LED display clearly prompts the driver that the tare weight is abnormal, and the weighing is checked; if the vehicle operation information is all legal and the vehicle weight is collected, the system will automatically save the weighing data. The LED display prompts that the weighing is completed, weigh down and leave, and at the same time the barriers of the barriers are raised, and the operation is completed.
5) Document printing module
In the current vehicle weighing mode, after the vehicle is weighed, the weighing inspector needs to print a triplicate measurement sheet as a voucher for leaving the house and completing the work.
After the automatic weighing is realized, the printing method of the metering list needs to be changed. You can consider picking up the measurement sheet at the gate exit. A small dot matrix printer or thermal printer is installed at the gate, and the driver scans the radio frequency card before leaving the port, and the system judges the state of the vehicle. If the vehicle operation link is complete, the weighing data is extracted and the measurement sheet is formed and printed out automatically. Give it to the driver to leave the port.
If you still need to print the measurement sheet in the inspection room, you can consider the following solutions: First, the driver does not get off the car, the printer and the radio frequency device are integrated in the same location, and the car window is the same height, and the driver automatically takes it away. This method is quick and efficient. However, it is difficult to implement. Second, the driver gets off the car and takes the metering sheet, sets the printer at the weighing window, and after printing the metering sheet, the driver comes to the serial port to pick up the metering sheet. This method is easy to implement, but it affects weighing efficiency.
The format and specifications of the measurement sheet have been redesigned and adjusted. The change and promotion of the measurement list can be coordinated by the inspection team and the business department with the customer.
6) Wagon exception handling module
The automatic weighing has stricter accuracy and verification of the tare weight of the weighed vehicle. The handling of vehicles with abnormal tare weight involves two departments: the inspection team and the security department.
Set a tare weight judgment range in the weighing system. If the difference between the tare weight of the vehicle and the historical tare weight is within this range, weighing is allowed, and the system automatically covers the tare weight recorded last time as the next tare weight. The criteria for determining the time. If the difference between the two tare weights exceeds the set range, the system will not weigh and send out an alarm. The duty officer printed out the letter of guarantee, and the driver went to the security department to inspect the car. If the inspection passed, the security department confirmed that the car could be weighed and the vehicle returned to the weighing room. A wagon modification module is added to the weighing software, and the duty officer fills in the reason for the modification of the wagon, and the system records it.
Regardless of whether the tare weight difference is within the judgment range, the weighing system shall record every passing operation of the vehicle, form a summary, and feed it back to the security department, so that the security department can track the problem vehicle.
In the current system, the weight of the wagon recorded last time is the comparison standard, and other wagon comparison standards can be considered, such as the average value in a certain period of time, the minimum value of the past few times, and so on.
7) Reverse transportation check
In the current system, no work receipt is used in the reverse operation. In the new system, the radio frequency card can be applied to the inspection of reverse transportation. Allocate a fixed radio frequency card to each diverted vehicle. Before the operation, assign the relevant vehicle to the corresponding operation plan number through the system software. After completion, the reverse operation will begin.
There are also cases of reverse operations. The system can adopt two modes of processing. The first is that the relevant personnel adjust the corresponding plan number in time and change it to the rollback mode to ensure that the data is saved in the rollback mode; the second is the new shipping plan of the business department and save the data under the new plan number.
For port operations in the current system, there are some plans that require manual intervention in gross weight operations. In order to improve efficiency, it is recommended to remove this operation.
There is also a plan that does not check the burden and only needs to issue a pass. It is recommended that this type of planned operation mode remain unchanged and still be operated manually by the staff on duty.
3.4 Scheduling software
Jishu port dispatching management software and reverse transportation management software are currently used independently, which has caused a lot of inconvenience to users. For this reason, we carry out the integration of the position in the system, the integration of vehicle display, planning information, instruction information, report integration, loading Machine touch terminal integration and so on.
1) Position integration: The systems all use the same electronic map, and the positions are in the same port, so the required positions of the two systems can be placed on one platform.
2) Planning integration: According to different types of plans, independent functional modules can be made and used in the same system.
3) Vehicle integration: All vehicles can be integrated on the same interface according to different permissions to display different working status and real-time information.
4) Report integration
5) Loader terminal integration: The two processes are basically the same, and different interface operations can be performed on different plans.
6) Command integration:
a) Reverse transportation instruction sending: according to the plan, send operation instructions to the dispatched loaders. Dispatch instructions for dispatching loader operations to the “dispatched” plan. It is divided into current instructions and historical instructions. The current instructions mainly include the planned “unfinished” instruction set. The historical commands include all “completed” command sets. The instruction to send requires each loader to have an “unfinished” plan on the job. The staff of the same plan can change shifts and count by piece. The same plan is operated by multiple loaders, and the same loader can only guarantee that one plan is in “operational state”. A planned operation time is uncertain. Before this plan is completed, each loader can be assigned to other plans to operate. Each loader completes the current operation of the released plan and needs to “complete this operation” before it can go to other planned operations. The dump truck under the same plan can operate back and forth N times.
b) Collecting and dredging port instructions mainly refer to land transportation instructions. In the land transportation operation instruction interface, the default is to select a single port dredging plan (“single selection” is selected), select the port dredging plan, select the equipment number and the stack number, and click “send” “Button to complete the sending of the job plan. When “multiple selection” is selected, multiple port dredging plans can be selected, but they must be the information of the same stack location. Select the equipment number and stack location number, and click the “send” button to complete the sending of the job plan. The statistics list can display some statistics of the selected port plan.
[ad_2]