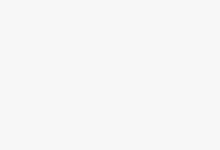
Intermec barcode system helps Nippon Paint improve finished product inventory management efficiency
[ad_1]
On January 18th, Nippon Paint (Thailand) Co., Ltd. has two factories in Samutprakarn Province and Amata Nakorn Industrial Zone in Thailand. The company has deployed barcode systems for 7 finished product warehouses in these two factories to manage product inventory. , Goods delivery from warehouse to customer, inventory management, and real-time online monitoring of shelves.
Since Nippon Paint’s product categories are rich, and each category contains a variety of colors, the daily flow of products in and out of the warehouse is very considerable. The barcode system can replace the manual recording system, speed up the work process and prevent human error. In addition, it can support the management quality assurance system, follow the first-in-first-out principle, and ship in accordance with the actual conditions of the products. This is because most products are chemical substances and are restricted by the validity period, the use period and the product recovery storage system. The recycling storage system is used to classify the products and complete the necessary processing steps for the recycled products. The entire barcode system relies on 25 Intermec mobile computers 730 and 730 i-Safe to complete the task.
Surin Pramchuen, Manager of Information Technology Department of Nippon Paint (Thailand) Co., Ltd. said: “We spent 7 months in 2007 to deploy a barcode system. This system was integrated with the existing SAP warehouse management system and read from the SAP system. Get data records. Product operation includes 5 aspects, namely warehousing, picking, inventory transfer, inventory overview, and on-site inventory. All previous records need to be filled out manually before being sent to the SAP warehouse management system. This process is very It is complicated and may cause human error. Real-time monitoring is a fantasy, because the data can only be updated after all entries are recorded in the system.”
After the barcode system is recorded, all work processes are simplified by shortening the process of the SAP warehouse management system, because some unimportant procedures will be automatically completed by the system, and the data of all online shelves can be recorded, and in Before transferring all data to the SAP management system, it will be transferred again through the paperless transfer system (from the office control to the outside control).
Paper records are no longer needed in the office. The data shows that the process from counting the shipping product list to issuing invoices is 70% faster than the original paper records. Using Intermec 730 and 730 i-Safe mobile computers, all logins will be automatically recorded in the SAP management system to reduce human errors, and all data can be updated on the basis of real-time connections. In addition, when the product is delivered to each consumer, the corresponding invoice of the invoice can be confirmed immediately by scanning the bill.
In the warehouse, the movement and transportation of all goods will be clear, specifying the type, location and quantity of the goods in detail. Because chemical products cannot be shipped once they expire, the remaining inventory space in the warehouse will be checked in time. For shipped products, their quality will be guaranteed through the FIFO rule (first in, first out) processing method, quarterly inventory clearing house The time required is also shortened.
Surin said: “Before choosing Intermec barcode system, we have used Intermec PD4 barcode printer. When we decided to deploy barcode system, we purchased more barcode printers of PD4 and PX6i series to make more This saves 80% of the cost compared with ordering product labels from printer shops. Therefore, we decided to use the barcode system on a larger scale and determined that Intermec’s solution could meet the requirements of our system. We finally chose Intermec 730 and 730 i-safe series mobile computers. The 730i-safe series is specifically designed for the chemical industry, which is a risky industry. It has the characteristics to meet all our needs, so it is the best choice. “
After the implementation of the barcode system, Nippon Paint (Thailand) Co., Ltd.’s related workflow efficiency has increased by 70%, and human errors in data entry have been reduced by almost 100%. Therefore, data such as the location of each product group, remaining inventory, and storage space that can be checked are more accurate. The performance of employees has also improved. Quality assurance can be made before the goods are shipped. In addition, the main advantage is to change the follow-up mode of data input only after ordering, to record data to the automation system in real time on the spot.
In the near future, Nippon Paint Coatings (Thailand) Co., Ltd. plans to implement RFID systems in raw material warehouses and finished products in the production process. RFID will replace some work links, especially in the product production process, monitor the flow of the product on the production line, clearly grasp which work center it belongs to, what machine it uses, how much time each process takes, and how much time it is used. What chemical raw materials are used to confirm when all processes can be completed and the final inspection results. All these results will be used to calculate various operating costs, such as time, color, and machinery, in order to improve production efficiency.
[ad_2]