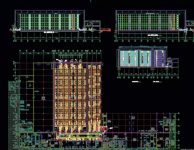
Jilin Zhengda Cold Chain System Construction
[ad_1]
In recent years, as the domestic market demand for meat processing and quick-frozen food continues to expand, the demand for food cold chain logistics by Zhengda Foods under the Zhengda Group has continued to increase.
At the beginning of 2017, several automated cold storage and cold chain logistics systems of Zhengda Foods constructed by Beijing Institute of Machinery Industry Automation (hereinafter referred to as “Beijing Institute”) were put into use successively in Jilin, Zhanjiang, Nantong, Xuzhou, Xiangyang and other places. Among them, the cold chain logistics system of Jilin Zhengda Food Co., Ltd. (hereinafter referred to as “Jilin Zhengda”) has a large scale of investment, a wide coverage, and is the most typical.
1. Project overview
Jilin Zhengda Food Co., Ltd. is located in Huancheng Industrial Zone, Yushu City, Jilin Province. It is invested and built by Thailand Zhengda (China) Agriculture and Animal Husbandry Co., Ltd., which integrates meat food processing, animal husbandry, and feed industry. “A set of dragons” is a large-scale modern agricultural and animal husbandry food enterprise. It can process 100 million broilers every year, with a total investment of 1.5 billion yuan, and an annual output value of up to 4 billion yuan.
According to Jilin Chia Tai’s requirements for raw food/cooked food not to be mixed, raw food/cooked food processing requirements in separate workshops, and the annual processing capacity of 100 million chickens, the entire system consists of an automated raw food cold storage, a cooked food cold storage, and a temporary storage of stainless steel miniload boxes. It consists of 5 flat warehouses, trays and circular shuttle conveying, cooked food stainless steel bin conveying, computer management and control, network communication and other subsystems. The cold storage system covers an area of 5118 square meters, with 5 lanes and 8 shelves in the raw food cold storage, 2 lanes and 8 shelves in the cooked food cold storage, and the unit cargo compartment carries 1100kg.

Automated cold storage and circular shuttle system layout
The system involves high-rise shelves, stackers and forks with double-deep structures and material selection calculations, processing and manufacturing technology research and development; low-temperature selection of circular shuttle conveyor systems and electrical equipment, energy-saving power supply; stainless steel bin racks and stackers The first R&D, manufacturing and control of the company; the reliability of the computer management system; the thermal insulation of transitional switching between different temperature environments; a series of key technologies such as product warehousing traceability, shelf life tracking management, etc., have been well applied in Jilin Zhengda, ensuring that The system and equipment operate safely, stably and reliably in a low temperature environment. This greatly saves the cost of land resources and human resources, and improves the efficient ability of Zhengda’s warehouse automation operations.
2. Automated cold storage and circular shuttle conveying system
The automated three-dimensional cold storage system of Jilin Zhengda’s slaughter and food processing plant consists of two independent double-deep, cross-beam combined high-rise three-dimensional shelves to form a raw food storage area and a cooked food storage area, forming two independent storage areas for raw food and cooked frozen products. Cold storage, raw food storage space of 63,400 cubic meters, cooked food storage space of 25,000 cubic meters.

The internal shelves of the cold storage are empty
The architectural structure of the two cold storage areas is characterized by: conjoined steel structure, independent of each other. The entire building is located on the south side of the central part of the main craft workshop. Each storage area of the automated three-dimensional cold storage is composed of high-rise shelves, key equipment stackers, and conveying systems.

Internal shelf loading of cold storage
The high shelf height of cold storage is 19300mm. Among them, there are 10278 storage spaces in the raw food warehouse and 3,632 storage spaces in the cooked food warehouse. Each pallet cargo space can store 1.1 tons, the storage capacity is about 15,000 tons, and the installed power capacity of the equipment is 350KW;
There are 5 sets of key equipment double-deep stackers in the raw food storage area and 2 sets in the cooked food storage area. Realize the function of fully automatic handling and storage of inventory products;
Raw/cooked food storage system process: raw food products go through automatic packaging, robot palletizing, pallet palletizing and film winding, and then through the RGV shuttle car and the automatic cold storage warehousing conveyor to automatically dock, pass through the fire compartment and transition room to achieve automatic entry Library. At the same time, the information bound to the pallet and the product is transmitted to the central control room server through the Ethernet. The WMS automatically allocates and dispatches the lane stacker to execute the warehousing operation through the WCS according to the received pallet information, and it is collected by the bar code reader during the stacker operation. The information is verified, and the system keeps accounts after the job is completed, so that the accounts are consistent.
Raw/cooked food delivery system process: According to the user’s order, the WMS/WCS system sends out warehouse operations under the stacker, and the stacker transfers the pallets on the shelves to the outbound conveyor, and then passes through the transition room and two cold storage The insulation door is automatically docked with multiple circular shuttles for transportation, and then the nearest shuttle is dispatched to the outbound platform through the circular shuttle dispatching system. The corresponding delivery platform and the outbound platform are equipped with LED board information to prompt loading information. Leaky wave communication is adopted between multiple circular shuttles, and the system runs reliably.

Circular Shuttle System Equipment
Raw/cooked food pallet warehousing system process: manually stack the empty pallets that need to be put into the warehouse by a forklift and send them to the empty pallet entry port at the outgoing end. After size detection, the system is based on the needs and storage of the empty pallets in the raw/cooked food cold storage. Space permitting, the pallets are moved to the empty pallet storage port by the circular shuttle system; the WMS system performs real-time calculations based on the maximum number of storage pallets stored in the conveying buffer line, and dynamically supplements them to always ensure the pallet supply required by the robot palletizing in the packaging workshop.
Raw/cooked food pallet picking system process: the pallets that need to be picked are automatically delivered to the picking and exiting station through the circular shuttle according to the picking information issued by WMS to the warehouse end LED, and manually picked according to the prompt picking information, and the remaining items after the picking are completed Automatic accounting back to the library.
In order to ensure the low temperature environment of the automatic cold storage, the two storage areas are equipped with 26 sets of freezer doors, including 16 sets of raw food storage areas and 10 sets of cooked food storage areas. According to different transition room structures, different structures of sliding doors and lifting doors are configured. So as to realize the switch of different ambient temperature and ensure the effective energy saving of the automatic cold storage refrigeration system.
All equipment and status detection of the automated cold storage and circular shuttle system can be viewed in real time, remotely operated and fault diagnosis can be performed on the WCS screen.

Automatic cold storage and circular shuttle system WCS screen
3. Miniload stainless steel cooked food temporary storage and bin conveying system
According to the process requirements, the Jilin Zhengda Food Deli Processing Workshop temporarily stores the products to be processed in the bin warehouse, and then according to the processing needs of each production line in the deli workshop, the corresponding processed products are transferred from the bin warehouse through the bin conveying system. Put it on demand, and return the empty bin after putting it back to the previous production workshop or back to the warehouse for temporary storage.

Miniload bin stainless steel rack/stacker
The complete set of all equipment including racks, stackers, conveyor systems and other auxiliary devices are all made of stainless steel. The high-speed stacker adopts a full-servo, stainless steel, dual-station, synchronous belt, and dual-drive structure mode. The horizontal running speed can reach 240 meters per minute, and the elevator fork can reach 60 meters. Among them, stainless steel high-speed stackers and stainless steel shelves are the first research and development and manufacturing in domestic enterprises. There are 5,096 material bins storage space, 1 set of double-layer material bin conveyor line, 7 feeding ports and 15 elevators, which can be washed with water.

Stainless steel rack roadway

Miniload temporary storage and bin conveying and feeding layout
Material box storage process: the material box has its own RFID chip information, and the material box from the previous production workshop passes through the fire insulation door to enter the material box library. After conveying, pulling the distance, reading the RFID information, and weighing, it automatically uploads the WMS In the management system, WMS assigns tasks through WCS, the material box automatically enters the corresponding laneway entrance, and the high-speed stacker automatically forks and picks the material box into the warehouse. When leaving the warehouse, according to the order information of the cooked food processing line, WMS automatically issues the outbound operation command, and the material bins in the warehouse pass through the fireproof and heat-preserving door and then are transported to the multiple feeding production lines of the cooked food workshop. The material box conveyor line has two layers. The upper layer corresponds to the feeding port of the production line, and the lower layer is for the return conveying of the bins. Each feeding port is equipped with two elevators. Before each bin enters the feeding port, RFID chip information verification is required. Ensure that the food processing feed is correct. The feeding method is automatic clamping box flipping feeding, and returning after feeding.
The process of discharging the material box: WMS builds an order according to the demand and issues the operation. Before the outbound material box reaches each feeding port, it is read and verified by RFID to confirm that it is correct. It is assigned to the corresponding feeding port and the material is fed through the bin The turning mechanism throws the semi-finished chicken products to be processed in the feed box into the cooked food feeding hopper for subsequent cooked food processing.
The Miniload temporary storage and bin conveying system shares a set of servers with the automatic cold storage for raw and cooked food. The key equipment of the three warehouse areas builds a local area network through the high-power wireless base station and conveying system, the circular shuttle system, and the WMS/WCS system installed in the warehouse. The local area network covers the automatic cold storage and Miniload bin warehouse system, and the packaging and palletizing system. Wait for all the equipment inside and outside the library. At the same time, it also realizes seamless connection with enterprise ERP or superior information management system.

Warehouse end bin conveying system

Outer storage bin conveying system
4. Difficulties and highlights of the project
The first research design applied the low-temperature temporary storage and bin conveying system to the interior of Chia Tai Foods’ cooked food processing workshop. Realize the operation links such as automatic temporary storage of incoming materials, automatic feeding of materials out of the warehouse, and transportation of cooked food processing. Shelves and stackers are made of stainless steel, full servo, high-speed (240 m/min), and can be washed. RFID information collection and meeting the special requirements of users are the first cases in China, and the promotion and application prospects are promising.

Conveyor system for bins in cooked food workshop

Feeding system for cooked food workshop
For the first time, the circular shuttle system was introduced into the automated cold storage delivery system. Through the use of multiple shuttles to adopt the leaky wave communication method, the raw and cooked foods stored in different warehouses are simultaneously delivered and delivered, and the functions of picking and empty trays are collected and returned to the warehouse.
Adopt the latest cold storage design concept, large-capacity storage body, fully automatic stacking and handling, automatic conveying, no personnel in and out operation, computer system automatic management and monitoring of cold storage accounts and equipment operation.
With the integrated structure of double-deep and cantilever racks, the limited warehouse area maximizes the storage capacity, and the equipment for doubling the cargo space is halved; the land use is greatly saved on the premise of realizing the warehouse capacity required for operation.
The switching of different ambient temperatures is effectively interlocked through the freezer door set above the conveyor at the warehouse end to ensure effective and energy-saving refrigeration in the warehouse;
The entry and exit information, the destination of shipment and loading, and the equipment failure alarm can be displayed at a glance through the LED billboards installed at both ends of the three-dimensional cold storage;
The key equipment stacker drive, forks, address recognition, power supply and other devices are all imported from abroad. The forks are controlled by rotary encoder servo; horizontal walking and vertical lifting use BPS laser bar code identification macro, accurate control accuracy, positioning accuracy High; the system is reliable and easy to maintain.
The difficulty lies in the fact that the implementation of cold chain warehousing logistics involves multiple disciplines and multiple links, and pre-evasion is particularly important, requiring sufficient design capabilities and accumulation of construction experience.
Five, the final effect of the project
The Jilin Zhengda automated cold chain logistics system was successfully completed and officially put into use, realizing the automation and intelligence of the whole process from cold chain logistics product workshop to warehousing. The computer management system covers all the management (WMS) functions of the automated cold storage, real-time scheduling and monitoring (WCS) of all equipment on the site, and seamlessly connects with the superior ERP system; the system realizes the warehouse management, the informatization of the cooked food processing process, and the principle of first-in-first-out , Account management is paperless, data transmission networked, equipment monitoring is remote, reducing personnel, improving efficiency, saving land resources, facilitating slaughter companies to adjust the market, temporarily storing food storage capacity, and improving cold chain food logistics turnover The speed of the truck has been unanimously praised by domestic food processing and slaughtering companies and cold chain goods companies for cooked food processing.
[ad_2]