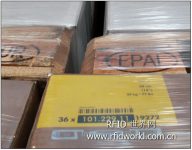
Lithuania’s first RFID project-Artilux NMF lighting factory successfully adopted RFID to track finished products and raw materials
[ad_1]
Artilux NMF, a Lithuanian-Swedish joint venture manufacturer of lamps and bulbs, is now using RFID technology to track the in and out of pallets of finished products or raw materials in its Siauliai factory covering an area of 11,000 square meters. This system is provided and installed by Autepra, a Lithuanian automation and telecommunications system integrator. UPM Raflatac’s RFID tags are used on pallets loaded with finished products, and Omnia Technologies’ reusable tags are used on raw material pallets. The software provided by Sprendimu idejos is integrated with the company’s existing Microsoft Dynamics NAV ERP system.
Artilux NMF produces approximately 6 million decorative bulbs and lamps each year, which can be loaded on 25,000 pallets. The vast majority of products are sent to distributors in Europe, which are then sent to retailers that sell lighting products. In the past, the company used a system that combined printing labels, documents, and pallet box barcodes to perform pallet tracking.
The finished bulbs and lamps that flow off the production line are stacked on a pallet with a piece of red paper on top of the pallet. The quality inspector inspects the pallet products to ensure that they meet the standards and can be sent to the warehouse for storage; then the red paper is removed, which means that the pallet has passed the quality inspection. Employees enter data about pallet goods in the company’s ERP system. Pickers then use a bar code scanner to scan the barcode of each item and record which items are loaded on the pallet or placed in the box.
However, this old system is extremely error-prone, because workers cannot guarantee that they will always clearly or correctly indicate whether the pallet has passed the quality inspection, or has been shipped out, or that the correct pallet has been shipped to the correct place at the correct time. There are often many errors in the entire process-the bar code of the item or pallet may not be scanned, the red paper may be placed on the wrong item (or forgotten), or the record of being inspected or shipped to the warehouse pallet can not be found.
When the pallet is filled with finished boxes, an RFID tag is applied to one of the boxes
Similarly, for raw material tracking, the old system also has similar problems. Goods such as wires and plastic components are delivered to the factory and loaded onto pallets and stored in the warehouse. The worker uses a barcode scanner to scan the serial number of the pallet barcode label, indicating that the material has been received. When the raw material is delivered to the production line, the worker scans the barcode again to update the material status in the system. But sometimes workers forget to scan the bars. Therefore, the company lacks a clear and precise understanding of the existing and used goods in the warehouse. In addition, barcode scanning is also time-consuming, and warehouse workers must leave the forklift to scan the labels of each pallet.
Therefore, Artilux NM needs a new way to track raw material inventory, to ensure the accuracy of the storage process of finished products from the production line to the company’s warehouse, and the shipment data is stored in its back-end system. In addition, the company hopes to reduce its labor costs. As warehouse workers have to manually enter data into the company’s ERP system, it has caused the phenomenon that high-paying personnel are engaged in basic computer work.
RFID systems can reduce errors and increase efficiency, says Tomas Girdzevicius, director of UAB Autepra. Artilux NM is one of the first companies in Lithuania to adopt RFID technology, and there is almost no successful experience to learn from, according to the company’s management director Aidas?etikas. Considering this reason, the company decided to gradually adopt the RFID system. After confirming the success of each stage, install the software and readers and label them in three stages.
In January 2009, Artilux began tracking the pallets loaded with finished products and shipped to the warehouse. With the new system, quality inspectors inspect each product. The production workers enter the relevant information about the product being loaded on the pallet in the ERP software, use a Zebra Technologies RZ400 printer to encode and print the ID code on the paper label containing the UPM ShortDipole UHF Gen 2 inlay, and then paste the label on the goods. Then use a handheld device (connected with a PC Bluetooth) to read the tag on a cargo box on the tray.
The pallet is then transported through a fixed RFID door reader (provided by CAEN RFID) at the entrance of the warehouse, which reads the pallet tag ID code again and sends this information to the back-end software via a cable connection. The RFID software upgrades the status of the pallet, indicating that the goods have been sent to the warehouse for storage. The employee then enters the ERP software to check which goods are stored in the warehouse and their history, such as production and storage dates.
When the pallet is sent to the warehouse, it passes through a door reader to read the pallet label and record that the pallet has been sent to the warehouse
The second phase started in mid-2009, when Artilux installed an RFID gate on the loading dock. Each truck is equipped with a LXE VX8 on-board computer, which communicates with the company’s back-end system via Wi-Fi connection. When the pallet passes through the portal reader, the company’s software compares its RFID code with the order to confirm the integrity and correctness of the pallet. If there is an error, the system sends an alert to the driver’s on-board computer screen to indicate that the pallet is wrong. This way the driver can return the pallets to the warehouse.
In the third stage, the company began to label the pallets loaded with raw materials, using Omnia Technologies’ reusable EPC Gen 2 UHF RFID tags. When the materials arrive at the warehouse, workers enter the material information (such as the serial number, manufacturer, and arrival date of each item) into the computer. Workers use adhesive tape to stick the label on the pallet, and use a Wi-Fi handheld reader to read the ID code of the label and match it with the material data. When the pallet is transported to the production site, it passes through another CAEN RFID portal reader. When the material is used up, the label is removed from the pallet and put into use again. The company began labeling 500 raw material pallets at the end of last year and has so far purchased another 4,000 labels to track raw material pallets.
In addition, the company installed computers equipped with handhelds on its 11 assembly line terminals. When loading on the pallet, the worker performs a quick inspection, reads a labeled box on the pallet, enters data, indicates that the pallet has been inspected and loaded, and then sends the pallet through the RFID portal The reader is sent to the warehouse.
Artilux requires that RFID readers (which can identify items within a fairly short distance-2-3 meters) will not read adjacent pallets. “The main problem with RFID gates is the reading distance” Setikas said, “The perfect reading distance we need is within 2-4 meters, but the reading distance of the gate has reached 7-8 meters, so we had to adjust the antenna to ensure The system will not read tags that have not passed through the gate”.
Since the installation of this system, the company has eliminated the errors that occurred during product loading in the past. Setikas said that the delivery process has been faster and the company has also saved warehouse space.
“As the first RFID project in Lithuania, it was very successful and we are very satisfied with the application results,” Setikas said.
[ad_2]