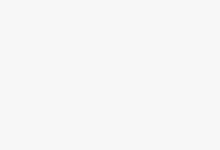
Mengniu Phase VI’s highly automated logistics system
[ad_1]
Mengniu Dairy Group was established in 1999, headquartered in Shengle Economic Park, Helinger County, Hohhot, Inner Mongolia, with total assets of 7.6 billion yuan and an annual production capacity of 5 million tons of dairy products. With the continuous expansion of production scale, since 2002, Mengniu Dairy Group has adopted automated three-dimensional warehouses to improve storage capacity and logistics management. Accompanied by more than 20 three-dimensional warehouses nationwide. Among them, the logistics system project of the sixth phase of the factory, which was put into use in 2007, has received extensive attention from the industry due to its huge scale and high degree of automation.
In 2006, Mengniu Dairy Group made the decision to invest in the construction of the sixth-phase production project at the headquarters, and proposed the “eight modernizations”, namely, internationalization, intelligence, scale, three-dimensional, display, individualization, differentiation, and system. It is prepared to adopt advanced design concepts and technical equipment to build a large-scale modern liquid milk production plant with the largest scale and the highest technological content in China, integrating production, scientific research and training. The main project of the project has an investment of 1 billion yuan, a main workshop of 47,700 square meters, 22 production lines, with a daily output of 2,000 tons of fresh milk. The central control system instructs various equipment to automatically complete the entire process from milk collection to product delivery. The completion of Mengniu’s sixth phase marks that my country’s dairy processing industry has entered the world’s advanced level and narrowed the gap between China’s dairy industry and the world’s dairy industry.
The logistics system supporting the Mengniu Phase VI project integrates automatic warehouse system AS/RS, aerial suspension conveyor system, palletizing robot, circular shuttle, linear shuttle, automatic guided transport vehicle AGV, automatic shaping machine, automatic film Many automated logistics equipment, such as winding machines, hydraulic lifting tables, rack shuttles, continuous hoists, and various types of conveyors, are the most advanced and most automated logistics systems in the domestic dairy industry so far.
System Requirements
Taiyuan Corundum Logistics Engineering Co., Ltd. is responsible for the overall planning and implementation of the Mengniu Phase VI logistics system project. Due to the long-term and good foundation of cooperation between the two parties before, the project took only half a year from the tender to the completion, and the speed and efficiency are amazing. The general contractor of the project, Taiyuan Corundum Logistics Engineering Co., Ltd., has withstood the severe test of large-scale solutions, large-scale integration, and service, demonstrating its strong comprehensive strength.
The Mengniu Phase VI logistics system mainly serves the production, storage, and delivery of liquid milk at room temperature. It is divided into production area, inbound area, storage area, and outbound area according to functional design, and the entire logistics process is automated and managed by a computer. There are 22 production lines in the sixth phase of the project, including 10 Tetra Pak 22 machines (3 slim type, 7 standard type) and 12 combi machines (5 slim type, 7 standard type), with a production capacity of 1,800 tons /20 hours, the outbound volume is 5000 tons/22 hours. According to regulations, the daily volume of products from the bottling workshop is about 110 pallets/hour; the volume that needs to be split out of the warehouse is 30 pallets/hour.
In the process of logistics system planning, Mengniu Group not only put forward high requirements for the processing capacity, but more importantly, required the realization of unmanned operations in the whole process from milk production to finished product delivery, loading and delivery, including finished products in and out. All logistics operations such as the transportation of warehouses, raw materials and packaging materials. At the same time, the entire system must meet the requirements of economy, flexibility, safety and ease of maintenance.
System Components
In order to realize the unmanned operation from production to delivery, the logistics system of Mengniu Phase VI consists of an automatic three-dimensional warehouse and conveying system for finished products, an automatic three-dimensional warehouse and conveying system for inner packaging materials, an automatic conveying system for auxiliary materials, and the three subsystems. The computer management system is composed.
1. The composition and characteristics of the finished product automatic three-dimensional warehouse and conveying system
The system starts from the product sealing in the production workshop to the roller conveyor (before loading) of the shuttle car in the outgoing area, and realizes the storage and outgoing operations of finished products, as well as the storage and storage of empty pallets. The main equipment includes:
1. Hoist
22 elevators are connected with the corresponding number of box sealing machines, with a lifting height of 2 meters, responsible for sending the finished milk box to the pallet robot
2. Robot automatic coding system
In order to improve the degree of automation of the overall system, pallet palletizing adopts robot operation. The pallet robot can palletize goods from two production lines at the same time. The manipulator is a six-axis type and can work continuously for more than 20 hours a day.
3. Circular shuttle
The circular shuttle is used to automatically transport the fully loaded pallets from the conveyor line after the robot is palletized to the stations at the inbound end of the finished product warehouse, and complete the automatic transportation from the empty pallet group at the inbound end to the disassembled empty pallet.
4. Conveying system
(1) The palletized goods are transported to the entrance of the inbound circular shuttle through the conveyor line, waiting for the transporter to enter the warehouse.
(2) There are 24 conveying lines at the outbound and inbound ends, corresponding to the 24 lanes in the three-dimensional warehouse.
(3) There are 20 roller conveyors (with slope) at the outbound loading place, corresponding to 20 cars.
(4) The empty pallets left after loading are sent back to the palletizing place, splitting place or three-dimensional warehouse through the conveying line.
(5) The remaining products after the split are also sent back to the three-dimensional warehouse via the conveyor line.
(6) The replenishment of empty pallets in the warehousing code panel is automatically completed by the system, which can ensure that there is always an empty pallet for standby when the robot is palletizing. After the empty pallets needed for palletizing are taken out from the three-dimensional warehouse (8 pieces are a stack), they are sent to the empty pallet conveyor line by the circular shuttle for unpacking, and then are allocated to the robot palletizing area.
5. High shelf
The total construction area of the finished three-dimensional warehouse is 102×106 meters. The highest point of the warehouse roof is 24 meters, and the lowest point is 20 meters. The shelves are distributed in 24 rows, 76 rows and 12 floors, 24 rows, 76 rows and 13 floors, with a total of 45,600 cargo spaces.
6. Single reach stacker
(1) There are 24 unit type linear tracked roadway stackers, and the maximum lifting weight of a single machine is 1200 kg.
(2) The frequency conversion speed control method is adopted to complete the inbound operation of the goods from the workshop or the outbound operation of the foreign goods.
(3) The stacker and the computer management and monitoring system adopt infrared communication.
(4) Stacker operation mode: online operation, stand-alone operation, manual operation.
2. Composition and characteristics of inner packaging materials and conveying system
The system starts with the manual palletizing of the inner packaging materials and the forklifts to transport the pallets to the inbound conveyor line, to the point of use where all the inner packaging materials are sent to the production workshop (including empty pallets back to the warehouse). The inner packaging material inventory contains packaging materials (including paper rolls and cartons) that are in direct contact with milk. Therefore, there are certain requirements for the cleanliness of the warehouse, so an automated three-dimensional warehouse is used for storage. In addition, the inner packaging material warehouse also has the functions of packaging materials and empty trays to go out. It is mainly composed of the following equipment:
1. Drive-in racking system
(1) The total construction area of the packaging material warehouse is 102×30 meters, the net height of the warehouse is 9 meters, and the total number of goods is 2,400. Since the pallets of the two packaging materials are of different sizes, the shelf is divided into two areas, each accounting for 50%. The size of the tray for placing Tetra Pak packaging materials is 1200×1200mm, and the weight of the tray and packaging materials is 1200 kg/pallet. The size of the tray where the Kangmei packaging material is placed is 1240×1000mm, and the weight of the tray and packaging material is 780 kg/pallet.
(2) The shelf adopts shuttle plate type cargo space and bolt connection type, and the height can be adjusted.
2. Single reach stacker
(1) Adopting two rotary stackers, the maximum lifting weight of a single machine is 1300 kg, which can meet the requirements of the purchase volume of foreign packaging materials and the shipment volume of packaging materials sent to the workshop, and can also meet the needs of different shelf sizes .
(2) There is no overload and loose rope protection device, rope break protection device, fork action interlocking protection device, fork torque limiter, cargo position detection and cargo detection device.
(3) The stacker crane and the computer management and monitoring system adopt infrared communication.
(4) There is no loading device on the stacker, which is convenient for personnel to maintain and manage the highest shelf.
(5) Stacker operation mode: online operation, stand-alone operation, manual operation.
3. Automatic handling system for outbound robots (AGV system)
At the end connected to the production workshop, the AGV (unmanned moving vehicle) automatically sends the packaging materials directly to the designated location of the aseptic filling machine, and the empty trays are returned to the packaging material warehouse by the AGV. The AGV adopts laser guidance and is composed of an AGV trolley with a conveying transfer mechanism, a ground navigation system, an online automatic charging system, a peripheral conveying system, an AGV console, and a communication system.
Third, the composition and characteristics of the auxiliary material automatic conveying system
The system starts from manually placing the auxiliary materials on the automatic handling suspension vehicle until the auxiliary materials are accurately delivered to the auxiliary material location in the workshop. The auxiliary material warehouse is located on the opposite side of the road outside the production workshop. It is a drive-in warehouse for storing cartons and straws. The elevation of the bottom of the aerial promenade of the auxiliary material warehouse is 5 meters, and the length of the air is 30 meters.
The carton demand for each production line is: Tetra Pak 834 pieces/hour and Combibloc 500 pieces/hour. The cartons and straws are transported to the cartoning machine and tube sticking machine in the production workshop by using an aerial unmanned automatic transport suspension vehicle. The aerial unmanned automatic transport vehicle adopts a single-track suspension mechanism and runs on a circular main track.
Four.Computer monitoring and management system
The entire computer monitoring and management system can realize the unified management of the finished product automation library, the inner packaging material automation library and the auxiliary material library. The finished product automation warehouse and the packaging material automation warehouse require the realization of online and online automatic control, monitoring and management, which mainly include three parts: warehouse storage logistics information management system, automatic warehouse control and monitoring system, and automatic warehouse control execution system. Among them, the warehouse warehousing logistics information management system has inbound management, outbound management, inventory management, data collection, quality inspection management, batch management, query statistics, system management, storage location management, human resource management, early warning, correction, and humanity Functional modules such as the operation interface.System Features
1. Complete the three-dimensional warehouse operation under the unified command of the computer, realize the automatic management of the goods in and out of the warehouse, automatically complete the data maintenance, query, modification, clearing report, inventory analysis, report printing and other operations of the goods, and dynamically display the equipment status , Location and completed work status, failure status reminder, alarm information, and the distribution of inventory goods, etc.
2. When warehousing, the system freely allocates cargo locations. According to the bottom-up principle, any cargo location can also be specified; when leaving the warehouse, in principle, it is based on the warehousing registration order (stock-in date and batch number), that is, first-in first. Out of the principle.
3. The computer monitoring system adopts a full-Chinese graphical interface, which has good openness, and the system functions are easy to modify and redevelop.
operation procedure
According to the three different materials of finished products, inner packaging materials and auxiliary materials, the logistics operations are as follows:
1. Finished product logistics
From front to back, the Mengniu Phase VI logistics center is composed of production area, inbound area, storage area, and outbound area. The specific operation process is as follows:
(1) Production area
22 carton sealing machines are connected to the pallet robot through the conveyor chain, and the conveyor chain is lifted to 2 meters above the ground when palletizing the cartons of Qianjiang belt products. The cartons are neatly stacked on the pallets on the downstream conveyor belt by the pallet robot according to the size requirements of the shelf layer spacing.
(2) Inbound area
1. The pallets of the packed products are transported by the circular shuttle to the conveyor connected with the lane stacker outside the automatic three-dimensional warehouse. Trays containing slim products need to be wrapped with plastic film before being put into storage.
2. There is a double-station high-speed circular shuttle in the warehousing area to distribute the goods to the warehousing entrance. The pallet goods must pass through a qualified appearance inspection device before being loaded onto the vehicle. Those who fail to pass will be transported by the trolley to the shaping device for reshaping before being put into the warehouse.
3. The pallets that have passed the inspection and palletizing are automatically placed on the cargo position designated by the computer system by the stacker.
(3) Depot area
1. There are 20 parking spaces in the outbound operation area, which can meet the loading and unloading tasks of 20 transport vehicles at the same time. The stacker takes out the pallets containing the products from the shelves and sends them to the circular shuttle outside the warehouse. According to the sales list, the product pallets are delivered from the roller conveyor to the loading truck.
2. Set up a product disassembly area at a certain part of the circular passing car, where the pallets that need to be disassembled are separated from the passing lane, manually sorted, and then returned to the passing lane.
2. Inner packaging material logistics
1. Storage
When the inner packaging materials are purchased from the outside, they are manually unloaded and placed on the pallet. The packaging materials are placed on the conveyor with a forklift and transported to the storage platform (an entrance). After receiving the instruction, the stacker puts the goods on the shuttle board nearby or according to the preset position, and the goods are placed on the shelves (two sizes of shelves) by the reciprocating motion of the through board.
2. Delivery
According to the production needs, the stacker will automatically take out the required paper rolls and carton trays and place them at the end communicating with the production workshop. The material handling from the warehouse to the production filling machine adopts a laser-guided automatic handling robot (AGV). The AGV sends the entire pallet of paper rolls or cartons to the designated station of the aseptic filling machine, and manually assists the loading of the paper rolls or cartons. The empty pallets are returned to the packaging material warehouse by the AGV. The system fully takes into account the problem of returning the remaining packaging materials to the warehouse after the end of production, and prioritizes the use of the remaining packaging materials in the next shipment.
Three, accessories logistics
Carton: At the designated station in the auxiliary material warehouse, after the carton is manually unpacked, it is placed in the loading mold of the truck according to the quantity and direction required by the production.
Straws: At the designated station in the auxiliary material warehouse, after unpacking the straws manually, put all the straws in the box in the turnover box on the truck.
The cartons and straws are transported to the packing and tube applicator in the production workshop by the aerial unmanned automatic handling suspension vehicle. The truck can automatically send these auxiliary materials to the boxing machine where the materials need to be loaded, and automatically put them into the carton buffer station on the boxing machine. After the end of production or when the product is changed, the truck can return the remaining cartons or straws to the auxiliary material warehouse.
Technology Highlights
The Mengniu Phase VI automated logistics system is a highly integrated high-tech equipment and control technology. It has attracted the attention of the industry for its large scale, many innovations, high degree of automation, and high operating efficiency. The project has many innovative technologies from information management control system to logistics equipment application.
In terms of the control system, the unified scheduling management of production logistics and multi-storage logistics is realized. The high degree of automation of the logistics center requires the unified scheduling and management of the finished product automation warehouse, the inner packaging material automation warehouse, and the auxiliary material warehouse, that is, the establishment of a warehouse logistics information management system, an automated warehouse control and monitoring system, and an automated warehouse control execution system, etc. Information control system; to realize the automatic control of production logistics and packaging, the unified management and scheduling of production logistics and storage logistics, and the overall management of multi-database storage and production logistics.
In terms of high-tech equipment application, the project covers a variety of advanced and efficient automation equipment, among which AGV and aerial suspension conveyor system are the biggest highlights of Mengniu’s sixth phase. In particular, the introduction of AGV in the outbound process of inner packaging materials has fundamentally realized true automated handling, which has become a major breakthrough in similar projects of Mengniu Group. It is understood that in the three-dimensional warehouses of other projects, the handling of inner packaging materials is mostly controlled by a computer-controlled stacker to remove the goods from the shelves and out of the warehouse by the track. In contrast, the application of AGV makes the transportation system of Mengniu Phase VI fully intelligent, which greatly improves work efficiency and reduces labor costs.
Judging from the operation over the past year, the Mengniu Phase VI logistics system has basically reached the original planning and design goals and achieved satisfactory results. Based on this, Mengniu Dairy Group is confident that its headquarters in Hohhot and Linder County will be built into a modern factory with the largest scale and the highest technological content in China, and a model for the dairy industry at home and abroad.
[ad_2]