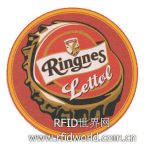
Norway’s largest beer and beverage manufacturer uses RFID to track freight containers
[ad_1]
Beverage manufacturer Ringnes uses RFID to track beer and other beverage containers leaving and returning to Oslo’s distribution center. This system improves the container management of the large freight yard in the distribution center and provides information on the movement trajectory of the products in the container. The system is designed and installed by IBM Global Technology Services, using Intermec hardware. In addition, Volkswagen of Germany adopted a similar system to track auto parts containers at its Wolfsburg assembly plant this month.
Ringnes, a subsidiary of the Carlsberg Group, is Norway’s largest brewery and supplier of soda and bottled water, selling approximately 1 billion liters (13,200 per year) of beverages. The company uses 200 trucks and trailers to transport beverages from the Oslo distribution center to retailers, and then returns empty or filled containers to the center. The company now uses an RFID system to track this process.
Ringnes is Norway’s largest brewery and supplier of soda and bottled water
Due to the huge product output and the number of retailers, it was difficult for Ringnes to track the process of product loading, delivery and return in containers before. Employees visually check which containers are available in the yard, and use paper records to understand where the containers should be located. Ringnes needed an automated system to understand the number and size of containers available and the time they took to load products and leave the yard. “We need more information, especially within the distribution center,” said Jon Kvande, Ringnes’ business process development manager.
As early as 10 years ago, Ringnes’s parent company, Carlsberg Group, discovered that barcode labels are prone to fall off or damage, and began to consider applying RFID tags on pallets. However, the price of RFID was too high at the time. It wasn’t until two years ago that Ringnes found IBM to consult with RFID labeling solutions for containers and pallets as the price of RFID fell. In December 2008, after a pilot test, the company decided to label 300 containers and track their entry and exit in the distribution center yard.
Because the container is loaded with various beverages, the RFID system has to work in a liquid environment, which sometimes interferes with RF signals, especially UHF. Moreover, another important issue is the durability of the label. Reusable containers are often subjected to high pressure washing, which may cause damage to the label. To this end, IBM chose Intermec Small Rigid EPC Gen 2 UHF RFID tags. According to Kvande, the tags work well and Ringnes uses two tags on each container.
The company has installed 11 Intermec IF5 fixed readers and 42 antennas at the entrance and exit of the container yard and the distribution center. When the truck enters the gate, an RFID reader reads the ID code of the container tag on the truck and sends this information to the company’s back-end system. IBM’s WebSphere Premises software stores the ID code on the company’s independent server and correlates it with the data and history of the container, such as the size of the container and its departure location, so that Ringnes knows that the retailer has returned the container Centered.
When the truck exits the gate, the container label is read again, prompting the staff that the container has been unloaded and the truck can perform other transportation tasks.
IBM’s DB2 Alphablox software allows Ringnes to view relevant reports, such as analyzing how long it took the container to return from the retail store, or how long it was empty in the distribution center.
The current running time of the system is not long enough for Ringnes to assess the return on investment, Kvande said, but the company has already received some valuable information. “One of the most interesting information is that we have too many containers.” Before, Ringnes had always thought that the company had too few containers, because the staff often couldn’t find the containers of the right size. After adopting the RFID system, the company found that the number of containers was not only sufficient, but possibly even too many.
According to Kvande, Ringnes will integrate the RFID system with the company’s ERP and warehouse management systems in the next step. After that, he predicts that this system will automate the loading of containers. For example, when the company receives an order, the system can effectively indicate the containers that can be used for loading. Previously, employees had to search the yard to see if the required containers were available.
“We also consider asset management applications,” Kvande added, adding that he envisions attaching RFID tags to refrigeration equipment (provided by the company to retailers to store beverages). If workers need to remove or repair a refrigeration equipment in the warehouse, they only need to use a handheld to scan the RFID tag on the equipment to create an electronic record. At present, workers visually read the serial numbers of the equipment and manually record them on paper.
At the same time, Kvande also stated that the company plans to put labels on the containers in the other two distribution centers.
In addition, Volkswagen used a similar RFID system designed and implemented by IBM to track 3000 reusable containers at the Wolfsburg assembly plant.
[ad_2]