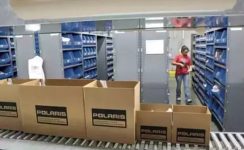
Polaris’s new distribution center introduces new technologies such as RFID"Sit down"
[ad_1]
Polaris Industries Inc. was established in Minnesota, USA in 1954. It is the founder of snowmobiles. After nearly 60 years of development, it now focuses on the design, manufacture and promotion of innovative, high-quality, high-performance sports vehicles. To meet the needs of customers for field work and leisure and entertainment, the products include All Terrain Vehicles (ATV), snowmobiles, and American cruise motorcycles. At present, Polaris has grown into a multinational company with operations in more than 140 countries and regions on six continents around the world.
Polaris was once called the American off-road version of Mercedes-Benz by the well-known American media “MacNeil/Lehrer”, thinking that it redefines off-road culture. With its excellent quality and outstanding performance, it has become a loyal partner of outdoor terrain workers including the US military. “Polaris” is a brand of snowmobiles and all-terrain off-road vehicles. It represents the highest level of quality and performance in the field of power sports. In North America, Europe, and Oceania, Polaris has basically become synonymous with high-end all-terrain off-road vehicles as the world’s number one all-terrain vehicle. Since the supplier of terrain off-road vehicles officially entered the Chinese market in 2010, Polaris has always been the leader, leading high-end and experienced off-road outdoor experiences and promoting the culture of dynamic sports. It is in line with the brand spirit of “the more no way, the more forward” advocated by Polaris.
1955: Polaris invented the world’s first snowmobile. Since then, the legend of Polaris has begun…
1960: Under the weight of the economic crisis, Polaris was on the verge of bankruptcy, but with the help of many parties, Polaris was retained and moved forward steadily.
1970: Polaris’ snowmobile team won championships in many competitions around the world, making the brand of Polaris famous in North America.
1980: With the introduction of the Polaris all-terrain vehicle (ATV), Polaris thrived in the 1980s.
1990: Polaris launched RANGER, jet skis and VICTORY brand motorcycles, Polaris entered a “all win” situation.
The 21st century: the more there is no way, the more forward. Polaris strives to do better…
In order to meet the requirements of dealers and ensure fast and accurate order processing, Polaris needs a set of efficient solutions to optimize the picking, packaging and delivery processes. Paul Eickhoff, Director of Operations at Polaris, said: “The key to our success lies in our culture of innovation, speed and flexibility of operations, and passion for continuous improvement of parts logistics.”
Previously, Polaris delivered parts, apparel and accessories to distributors through the South Dakota Distribution Center in the eastern United States. To improve service levels and shorten order response time, Polaris needs to build a new distribution center to support the company’s future business development. In terms of the effectiveness of the logistics network, Ohio is the best location. After the new distribution center is completed, the existing distribution center will continue to operate.
System composition and operation process
The new distribution center uses a strategic inventory plan to optimize layout and operational performance. Among them, the parts picked by box are concentrated in the whole box picking module; the goods picked by piece are concentrated in the zero picking module; the large goods that are not suitable for transportation are unified on the pallet. Polaris distributes goods of different specifications to different areas for storage in accordance with the turnover rate.
Picking
After the regional dismantling and picking module sends the order container to the pickers, the pickers do not need to find the goods in the warehouse, but only move around in the designated area to pick the goods. The operation method of this module is that the order container is only sent to the area with picking task. In order to support the regional picking system mode, the conveyor system controls the entry and exit of order cartons in the picking area. Arrange a picking staff in each area; during peak hours, the number of operations will increase; when the order volume is small, one operator can be responsible for multiple picking areas.
The conveying line is equipped with accumulation conveying equipment, covering the entire outlet and branch lines of the zero-dismantling and picking module. Each exit is equipped with a barcode scanner and a right-angle turning machine, which can sort the order cartons to the designated picking area. After the current picking task is completed, the operator pushes the order carton back to the central conveyor line; if it is necessary to continue picking, the order carton will be transported to other areas; if all the picking tasks have been completed, the order carton will be sent directly to the packing area.

Do a good job of dismantling and picking order cartons
The order originating station is set up upstream of the conveyor line of the dismantling and picking module. The staff sticks the unique barcode on the carton to make the order carton, and then sticks the tape on the inside of the carton. The cartons go through the conveyor line to the area with order tasks.
Pickers fixed in some areas hold RF terminals to obtain picking instructions. When the order carton reaches the picking area, the pickers scan the barcode of the carton, and the screen of the RF terminal will display the picking instructions. The picker scans the barcode on the picked goods to confirm that they have taken the correct product specifications, puts the picked goods in the order carton, and then pushes the carton back to the conveyor line.

Product specification scan to confirm accurate picking
After each order carton is sent to the packaging table and the delivery system, after confirming the product specification information and calculating the shipping cost, the sorting shipping label is printed out and the box is sealed. The completed order boxes are transported to the delivery area, and the sorter automatically allocates them to the appropriate delivery port for loading. The shipping boxes are automatically sorted to the manual palletizing station.
FCL picking
The goods in the FCL picking module area use pallets as the storage unit. The staff obtain instructions from the handheld RF terminal, and after walking to the pallet position, take the whole box of goods from the pallet and place them on the conveyor located in the center of the area, and paste the pre-printed labels on each carton. The carton is Send it to the delivery area and automatically sort it to the appropriate truck loading port or send it to the manual palletizing area for delivery.

Picking to the full box picking module of the belt conveyor line
Warehouse Control System
The Warehouse Control System (WCS) manages the automatic operations of the conveying and sorting system, and guides the flow of the zero picking cartons to the appropriate picking area. Using barcode scanning data, WCS can activate right-angle turning equipment to automatically sort cartons to the picking area.

Lifting wheel sorting system
WCS also directly manages operations including the full box picking module conveying system, packaging station and delivery sorting system. The system will generate relevant real-time information such as carton position, sorting data, barcode reading speed and carton circulation volume. The system can also display the information of each subsystem, such as the operating status and performance of the system such as picking, packing, packaging merging, garbage collection conveyor line, and delivery.
Application effect
The new distribution center can support 1,100 dealers, the design storage capacity reaches 20,000 product specifications, the order processing accuracy rate is maintained at more than 99.9%, and more than 99% of orders can be completed within one day. Paul Eickhoff, Director of Operations at Polaris, explained: “We carry forward the spirit of perfect order, so that the order goods, quantity and related documents are accurate and delivered in time.”
Modular system design improves warehouse operation efficiency, order processing speed and order accuracy rate, while flexibly responding to changes in demand. From the change in the number of operators in the zero picking and FCL picking modules during the peak order period, it can be seen that the order processing capacity of the distribution center has been significantly improved. During the low order period, too many staff will not be arranged. Not only that, the work stations and delivery crossings can determine whether they need to provide services based on the daily workload. The logistics system currently processes about 500-700 orders (6000 order lines) every day, and 150 re-stocked orders. The processing capacity of the entire system is 25,000 order lines.
In addition, there is no need for pickers to travel throughout the warehouse to find goods. The clever system design fixes the staff in a compact area with high picking frequency to minimize walking distance and improve picking efficiency. In addition, the area picking system can instruct the order cartons to only go to the area with picking tasks, thus shortening the order processing time.
The modular layout combined with the automatic conveying and sorting system has greatly improved the efficiency of picking, packaging and shipping operations. The logistics system design can meet the future business growth needs of Polaris. For example, the sorting crossing can be installed in the delivery area in advance; if the processing capacity needs to be expanded, the modular inclined conveyor line can be added, and the software pre-configuration function can also be activated.
[ad_2]