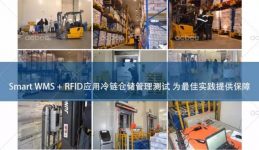
RFID applied to cold chain warehouse management integration test
[ad_1]
Recently, Tianjin Xiaobee Computer Technology Co., Ltd. (abbreviated as Xiaobee Company) completed the pre-implementation test of RFID cold chain warehouse management application. The customer is a large cold chain warehouse logistics enterprise, which is a typical third-party warehouse logistics and cross-border For border e-commerce suppliers, the application of RFID technology this time is to improve the efficiency and benefits of warehousing business. Through the seamless connection of middleware technology and Smart WMS smart warehouse management system, it can achieve more efficient management of business processes and inventory management, and improve Modern, informatized, and intelligent warehouse management level realizes intelligent cold chain warehouse management.

The Smart WMS team of Little Bee Company adheres to the rigorous working style of “getting a sense of the last thing on paper, and knowing this matter must be practiced”. Our Smart WMS team not only provides customers with a simple plan document, but also before the project is implemented. Through testing, customers can truly understand the application effects, practice with customers, and be responsible for the results to meet customers’ expectations and hopes.
The main goal of this project test is to integrate RFID technology into the customer’s Smart WMS smart warehouse management system, go deep into every business process, improve the accuracy and efficiency of daily warehousing operations, solve current business problems, and overcome severe low temperature and condensation , Complex cold chain storage environment, eliminate the uncertainty of RFID applications in different scenarios, verify the recognition effect and accuracy of the actual application of RFID fixed readers, vehicle-mounted RFID readers, and handheld RFID readers, Use the software’s intelligent algorithm and actual application process to determine the best solution in combination with the business process to provide guarantee for the overall RFID project implementation and realize the best practice of RFID application.
Customer Profile
As a leading cold chain warehousing and logistics service provider, the client mainly provides third-party warehousing and logistics, cross-border e-commerce, commodity inspection, customs inspection services, imported food international market transaction services, and provides overall supply chain services. Customers have Its professional and high-quality cold chain warehousing and logistics service capabilities. In terms of warehousing, there are multiple warehouse types such as fully automated, semi-automated three-dimensional warehouses, flat warehouses, etc. The application of RFID must combine the different characteristics and processes of each warehouse to develop different solutions.

Summary of the test process:
The Littlebee Smart WMS team has conducted many field investigations on the project, and communicated with customers from different angles to understand the needs, committed to in-depth understanding of the customer’s warehousing environment, business processes, and customer expectations, and then formulated corresponding solutions plan. The purpose of the test is to verify the effect of RFID technology in complex and different business scenarios to achieve the best solution.

Core business process-warehousing

Core business process-delivery
The warehouse management system based on RFID technology is an integrated system, which is the extension and application extension of the Internet and communication network, and is a highly integrated and comprehensive application of a new generation of information technology. It is mainly composed of two subsystems, a software system and a hardware system.

Smart WMS+RFID system topology diagram
Test Plan:
First of all, a project team was established within the Smart WMS team of Little Bee Company, and an organizational structure for project management was set up. There were multiple roles of project manager, software, hardware, and support personnel to formulate test goals and specific plans. On the listed test plan, there are nearly 200 items in chronological order.
We always believe that the application of this new technology of RFID, in the RFID industry warehouse management solution provided by the Little Bee Smart WMS, we will work to redefine the meaning of RFID applications and provide a simple and easy-to-implement software and hardware integration Solutions to provide the most effective service in the simplest way. Based on RFID technology, it can optimize the business processing, workflow and inventory control of warehouse management, and bring customers productivity, accuracy, profitability and customer service improvements. In the test plan, we will closely focus on the customer’s core business process and seamlessly integrate RFID into the customer’s daily warehouse management business.
Test preparation:
During the test preparation period, develop vehicle-mounted, handheld, and fixed specific RFID middleware and test Demo application software in accordance with the warehousing business process. The software development incorporates the intelligent algorithms and filtering mechanisms for RFID applications accumulated by the Smart WMS team of the Little Bee Company After coordination, we selected the read-write equipment and various types of tags from a number of hardware suppliers, and prepared various accessories for forklifts, automated warehouses, and pallets.
The main RFID equipment is selected from the top brands in the world. The low temperature and the complexity of condensation in cold chain warehouses pose challenges for the industrial grade and performance of the equipment. The anti-vibration and impact capabilities in vehicle applications have raised the issue of vehicle RFID reading devices. Very high requirements. The main equipment mainly includes: vehicle-mounted RFID readers, handheld RFID readers, fixed RFID readers, and antennas of various specifications.

RFID master equipment atlas
Due to the needs of forklifts, automated warehouses, and different processes in different warehouses, the requirements for project integration are very high. The requirements for accessories for this project are very high and the quantity is relatively large. In our list, there are as many as two hundred items, mainly including the storage battery on the forklift, the power supply for the tablet and the RFID reader, and the constant current and constant voltage automatic charger for charging the battery because of the high shelf. For forklift operations, we chose the Bluetooth solution for wireless communication.

Main RFID auxiliary equipment and accessories
It is worth mentioning that, in order to facilitate the physical integration of forklifts and automation facilities, we independently designed a load-bearing bracket made of aluminum alloy steel material. It is very flexible to use and configurable. It can realize fast and cheap reconfiguration to support continuous Changing application requirements, such as pallet label reading, shelf label reading, and conversion to box level reading, are faster and cheaper to install and deploy. It can be replaced quickly after damage, and will not cause problems during busy periods and will not affect work efficiency.
For this test, we have prepared many types of RFID electronic tags for different processes in automated, semi-automated, and flat warehouses, and they must be affixed to different positions such as pallets, floors, and shelves. There are labels in PVB, paper, plastic, and ceramic packages. The installation method requires screws, rivets, super glue, cable ties, or double-sided tape.

Various types of shelves, pallets, floor labels
In addition, the debugging of RFID hardware equipment, the development of RFID middleware and application software, and the debugging of communication methods are also required. After the management and coordination of the project manager and the efforts of the team members, all the tasks are in order. Unfold.
Summary of the test process:
After intensive test preparations, we began to enter the site for testing. The team members tested the low-temperature environment of the cold storage. The corridors of the warehouse were minus four to five degrees Celsius, and the internal temperature of the warehouse was minus 20 degrees Celsius. The continuous implementation of the test plan required four Five working days. The testing process is mainly the installation of equipment, deployment of scenarios, testing of different scenarios, different types of warehouses, and problems found in the process and solutions. Let’s give you a simple graphic introduction from the entry to the end.
(1) First of all, it is the scene of personnel and equipment entering the warehouse. We have prepared three lifting boxes to hold the main precision equipment. After arriving in the warehouse corridor, we will prepare for the equipment installation. The following picture shows the real shot scene:

Preparation after entering the scene
(2) Next is the integrated installation of RFID equipment on the forklift, which mainly includes vehicle-mounted readers, multiple antennas, tablet computers, power supplies, etc. The aluminum alloy brackets designed and manufactured by us are used to carry all important equipment, because The test part is wrapped with plastic film to avoid damage, and it is fixed in a simple and adjustable way.

Integrated installation of forklift RFID equipment
(3) During the intermittent period, the team’s colleagues in charge of video recording and photography circled the corridor of the warehouse. Today, the customer’s business is relatively busy. Now let’s take a look at some scenes in the corridor of the warehouse.

Warehouse corridor scene
(4) After the installation is completed, the fork pallet and unloading operations, and the loading operation are carried out first, and the RFID reading test is performed in the container, loading, and picking the fork pallet. We perform various situations in turn. Test the data, and adjust the software parameters, set the strategy and adjust the angle of the antenna accordingly.
RFID fork pallet test
(5) The next “exciting” RFID test in the library began, because here is minus 20 degrees Celsius! The team also put on gloves, hats, and thickened a layer of clothing. After entering the warehouse, the first thing to be done is to place RFID electronic storage tags on the shelves, which must be installed on each layer. According to our experience at different heights, the corresponding reading effect is definitely different.
Place RFID tags on shelves
After the RFID cargo location tag is installed, the loading and unloading tests are carried out. After the goods are put into the warehouse according to the process, the goods enter the stocking area first, and then the forklift loads the goods reading tags, and the location information of the goods is obtained from the Smart WMS and displayed on the tablet computer. Then carry out the shelf operation, scan the goods label first, and then scan the cargo location label. The data is communicated with the database through the wireless network, and the data is compared. After the accuracy is correct, the shelf is completed.
The removal operation is to find the location and the goods according to the task, carry out the scanning operation respectively, and then complete the removal operation. During the test, we adjusted the corresponding RFID middleware, parameter settings, and antennas for reading pallet tags and shelf tags. After a day and a half of testing, we completed this part of the test.

RFID reading and writing test on and off the shelf
(6) Later tests were carried out on a flat warehouse. This warehouse is mainly for goods without packing boxes, which are stored and stacked on iron frame pallets. The iron frame pallets are placed with anti-metal labels, and the cargo location labels are placed on the ground in front of the goods. Used as a landmark, and then carried out the bottom and high-level tray reading test and ground RFID tag test respectively. The effect of the test exceeded our imagination. The reading rate and effect under various conditions are satisfactory, and there is no misunderstanding. Phenomenon.

RFID testing of flat warehouse
(7) RFID testing of high-level forklifts, high-level shelves require high-level forklifts to work, and correspondingly, the forklifts need to be transformed with RFID equipment integration. For the RFID part of high-level forklift operations, we use two communication solutions, one is wired and the other is wireless. The wireless solution overcomes the challenge of this high-level operation cable. The forklift RFID system also extends the data collection. Mobility for maximum flexibility.

RFID integration test of high-bay forklift in high-bay warehouse
(8) Fixed RFID readers for automated warehouses, high-reliability products designed specifically for industrial environments, small in size, economical and efficient, and able to penetrate harsh industrial environments. Set up an RFID reading node at the gate node, and transfer the collected data to the computer background management software through the wired network, and direct the background server to feedback the status and data information changes of each operation node in real time to help the background obtain job site data information.

RFID fixed reader test
Test summary
This time, the Smart WMS team’s warehouse management test project based on RFID technology is different from conventional software and hardware testing. It is an application test centered on the customer’s industry and specific environment and needs, which is close to the actual application environment. To test the process and results of the entire program. In particular, the application of RFID, a new technology in a complex environment, needs to eliminate uncertainty, provide real help to customers’ business, and bring efficiency and benefit improvements.

Smart WMS + RFID test summary
The test process and results were very successful. The members of the Little Bee Smart WMS team encountered many problems during the preparation and implementation of the test, which were solved by our concerted efforts. In addition, in the haze weather and the cold storage of the cold storage In the environment, team members also showed outstanding professionalism and a strong sense of serving customers. At the same time, I am very grateful to our customers for providing us with a good environment. From leaders to employees, we closely cooperate with us in testing, providing delicious lunches and transportation assistance. In addition, I am very grateful to the partners who provided us with equipment and the experts who provided technical support. It is our close contact and collaboration with customers and partners that have achieved everyone’s common expectations, and even exceeded the expected results.
[ad_2]