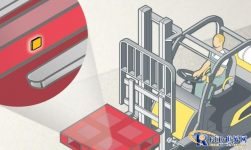
RFID case study: Japanese pallet rental uses sturdy tags to achieve accurate pallet tracking
[ad_1]
Customer: Using pallets to transport goods can reduce 90% of the workload in loading and unloading goods, reducing cargo damage, reducing inventory errors, and improving storage efficiency. However, there are still many companies that are reluctant to adopt this approach. The primary reason is cost. The large-scale use of disposable pallets is too costly and will cause environmental pollution, and reusable pallets will incur additional costs when empty trays are recycled.
Challenge: Pallets are often in harsh environments. They may be exposed to the outdoors for a long time, repeatedly hit or scratched by a forklift, or damaged during transportation. In these cases alone, it is impractical to use barcodes to identify each pallet, not to mention that such methods require additional labor costs. On the other hand, radio frequency identification technology (RFID) has great potential. If RFID tags can withstand harsh environments, Japanese pallet rental companies can easily identify and track pallets without having to pay expensive labor costs.
Due to the huge number of pallets circulating in various regions, pallet leasing companies often find it difficult to accurately track their assets, resulting in reduced revenue.
> Some companies lose up to 30% of their pallets every year-calculated at the cost of ordinary plastic pallets, the cumulative loss is huge. Since it is impossible to grasp the precise location of the pallet, it is difficult to provide customers with an accurate rental price.
Although Japanese pallet leasing companies have not suffered such severe losses, they have faced severe climate change and harsh transportation conditions. Even if the label is affixed to the inside of the pallet-which reduces the possibility of label damage-the label will still suffer a lot of impact. The built-in label can only be placed on the vertical support surface. However, the forklift tines also engage with the support surface, and therefore also exert a certain impact force on the support surface.
In order to create an inlay that can withstand strong impacts so that the tray identification operation can be performed smoothly, Mighty Card and Impinj turned to develop a packaged tag chip (Monza™ tag chip) soldered directly on the antenna. By using this chip, the inlay can withstand greater impact than the plastic packaging method.
The final production standard exceeds the design specifications and performance. In the pre-production test, Mighty Card put the label under various environmental pressures, including falling from a height of three meters to the concrete floor, performing a temperature cycle test of 20 oC-85 oC, immersing it to 1 meter underwater, and placing it on the concrete floor. An environment with a humidity of 95% is moderate. The label successfully passed all tests. In order to test the actual scene, the forklift operator deliberately hit the label fixed on the pallet containing 800 kilograms (about 1700 pounds) of water with the forklift tines. The impacted label still works well and fully meets (or exceeds) the performance specifications. Even when all the packaging plastic is melted off (placed in an oven at 200oC for 3 hours), and part of the label is removed (leaving the complete chip), the label can continue to work. Mighty Card is very pleased to meet customer needs with Impinj’s support.
[ad_2]