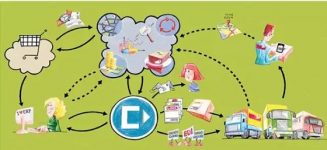
RFID simplifies the distribution process of Hatstore.se
[ad_1]
It was difficult for us to send small parcels in the form of letters before, because small parcels are untraceable. But now that RFID technology is applied to shipping labels, we can track large packages like packages sent in the form of letters. In the following, the Hatstore.se online store will explain the advantages of using RFID shipping tags.
Since 2011, Hatstore Scandinavia AB is located in a warehouse on the outskirts of Kalmar in southern Sweden and has been supplying hats to customers throughout Europe. In November 2016, they started using Bring’s product “Pakke i Postkassen”[信箱中的包裹]Send packages with RFID tags to Norway. With “Pakke iPostkassen”, packages can be delivered to the customer’s mailbox, and with RFID, consignor can obtain all the tracking processes from the whole process to the final delivery.
“The RFID we chose allows us to deliver packages faster and on time, and, unlike before, we can track small packages. Customers are involved in the transportation process and can track delivery throughout the process”, Filip Klasson, vice president of HatstoreScandinavia AB Said, and continued: “RFID printers and labels with RFID microchips are more expensive than general label printers and labels, but they are worth the money.”
Hatstore uses the delivery management software Consignor’s web version of Consignor Ticket to print RFID labels. Through Consignor, no matter how many carriers they have, Hatstore can book and print all shipping information in one system. On Consignor, Hatstore can also track their shipments and send notifications to customers to inform them that the delivery is in transit.
This is how Hatstore uses RFID and Consignor
“Consignor Ticket is integrated into Hatstore’s online store system, so as to realize the connection between the customer system and Consignorticket and automatically return to the printer. In this way, our customers can automatically obtain delivery management through the web version,” Consignor AB’s national area Manager Carl-Henrik Hällöf explained.
“Integration into Consignor is easy. Our online store suppliers only need to create an XML file and then integrate this file into Consignor. Consignor reduces the number of label printing steps to a minimum, which makes the entire transportation process more smoothly,” Filip Klasson said.
Hatstore’s customer service department has also improved.
“The problems related to package tracking have been reduced from about 10 per day to only one,” said Dardan Drini, the customer service supervisor, and continued: “When customers call to inquire about the delivery status, we can use the order number and receipt on the Consignor Portal. The name or phone number of the shipper found the package.”
Consignor Portal is a service included in all Consignor versions. ConsignorPortal continues to update the carrier’s package tracking information so that Hatstore can track their packages. Hatstore recently activated email notifications to customers through Consignor’s Mailback feature. In this way, the customer will receive an email with a tracking link to check the delivery status.
Joel Lindskog, Hatstore’s warehouse manager, concluded: “In addition, RFID tags are smaller and more suitable for our small packages.”
RFID example
RFID, or radio frequency identification, is a wireless technology that transmits data through electromagnetic fields, which makes it possible to identify and track objects. When it comes to distribution, RFID chips can be implanted into shipping labels. When the package is close to the carrier’s RFID scanner, the chip in the tag is automatically registered and updated wirelessly during shipment through EDI data. In this way, the carrier does not need to manually scan the package. When the RFDI label is scanned, the carrier can add events to the shipment, such as sending an email or text message “Your package has been shipped”, and at the same time sending a notification to the customer.
Hatstore
Hatstore was founded in 2011 and now has 9 online stores in multiple countries.
Hatstore has 13 employees, 9 of whom work in warehouses.
Hatstore’s warehouse on the outskirts of Kalmar sends 150,000 packages a year.
Hatstore not only sells various brands of hats, but also has its own brand “Bearded Man”.
Hatstore has approximately 5,000 products in its online store.
The RFID chip is embedded in the shipping label, so it is larger than the average label. This requires a special printer that can program the RFID chip in the label.

Hatstore vice president Filip Klasson (right), warehouse manager Joel Lindskog (middle), and customer service supervisor Dardan Drini (left) in a warehouse in the suburbs of Kalmar in southern Sweden.
[ad_2]