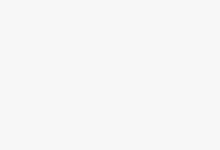
RFID speeds up the coal weighing process
[ad_1]
SCG Logistics Management Co., a logistics and transportation company in Ayuthaya Province, Thailand, uses an RFID system in its coal import business to track the amount of coal on trucks. This system realizes the automation of the previous labor-intensive trucks and their coal-loaded weight tracking process, reduces the time that trucks wait in line for weighing, and charges more accurately. So far, SGC claims that the RFID system has reduced the operating time of floor scale workers by 30-40%.
The company sells imported coal to third-party companies. These companies send trucks to SCG warehouses to load coal, and then transport it to all parts of the country. Truck weighing is an important part of the coal import business, that is, charging is based on the weight of the coal loaded on the truck. Every truck that arrives at the SCG warehouse must be parked on a ground scale and tare (empty truck weight).
Before adopting the RFID system, the driver showed a loading document to the operator of the weighing station, and the staff of the weighing station entered the data on the PC to record the truck weight and the truck license plate number. Then the truck drove into the warehouse and returned to the scale to weigh again after loading the coal. The staff at the weighing station manually enters the loaded weight in the weighing software of the company’s back-end system, then prints the file, indicates the weight, and gives it to the driver. The weight data is stored in the company’s back-end database.
The biggest disadvantage of this manual system, the company says, is that it consumes a lot of labor: every time a vehicle enters and exits the factory, the staff must check the license plate and enter the number repeatedly. Moreover, if the driver provides the employee with an incorrect license plate number, then the billing will be wrong-or, in some cases, if the data is false (for example, if the license plate number is invalid), the company cannot even count Fees and charges. If the truck cannot be identified correctly, the worker cannot be sure that the truck weighed before and after loading is the same. According to Wirote Ngamsukkasamesri, general manager of Identify RFID, an integrator of Thailand’s RFID solutions.
Other technical solutions cannot be as effective as RFID systems. For example, although the CCTV camera of a floor scale can obtain the license plate number, employees need to spend a lot of time checking the belt every day. And RFID can simultaneously improve operating efficiency and accuracy. “When a truck with a permanent electronic tag arrives on the scale, the number will be automatically displayed on the program,” Ngamsukkasamesri said.
For each truck that enters the warehouse, SCG Logistics will distribute a TagMaster active 2.45 GHz RFID tag, which is affixed to the windshield. The unique ID code of the tag corresponds to the data entered into the SCG Logistics back-end data system, such as the license plate number. When the truck is parked on one of the company’s three floor scales for pre-loading and weighing, the TagMaster RFID reader at the gate can obtain the tag ID code 10 meters away, and send the information to the Identify RFID hosting WEB server through a cable connection-with the company’s SAP System integration. The scale staff then saw the license plate number and other data on the computer screen. Employees can compare the loading documents submitted by the truck driver with the data on the computer. The weighing scale measures the weight, which corresponds to the RFID number and the corresponding vehicle data stored in the back-end system.
There are approximately 200 weighing transactions per day per scale. With the RFID solution, the floor weighing process time has been reduced by 50%, the company said, because employees do not need to re-enter the license plate number. The company also does not need to enter the details of each weighing transaction, such as the identity of the truck, the company and the weight of the truck, before leaving get off work every day.
Now, Identify RFID is working with floor scale manufacturers to integrate the RFID system into the floor scale hardware to develop a non-manual weighing system-that is, without the need for employees to manually enter the weight. “Our goal is to reduce the working hours of employees at the weighing station while ensuring accuracy,” Ngamsukkasamesri said.
[ad_2]