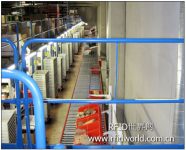
RFID system helps Wurth Group improve the picking process
[ad_1]
Wurth Oy is the Finnish subsidiary of Wurth Group, a global assembly and fastener supplier. The company now uses RFID on the 1.5-kilometer picking line at the Riihimaki plant. This closed-loop application uses a total of 40 fixed readers to read about 1,000 plastic containers of EPC Gen 2 passive UHF tags. RFID data is used to instruct the conveyor belt system to transfer the container to the correct picking station.
This system ensures that the container is delivered to the right site, not only saving time, but also reducing labor costs (by reducing manual steps in the picking process). According to Antti Kansala, business development manager of Vilant Systems, Vilant Systems designed it for Wurth Oy This RFID system.
As early as 15 years ago, Wurth had adopted a similar system based on low-frequency tags. However, the company could no longer purchase parts of this system, so it hired Vilant to update the old system without affecting normal picking. The company’s picking process is a two-shift format, where more than 70% of orders are processed every day.
The new UHF system is adopted. Like the old low frequency system, the command data of the conveyor belt is stored in the label. When picking starts, the system writes information to each container label. The reader then reads the container tags moving along the conveyor belt. When the container is close to the station that needs to be stopped (a total of 20 stations), the system moves the container off the main conveyor belt and sends it to a picking station next to it. There, workers load products into the container according to the printed picking list. After loading, the workers return the container to the mobile conveyor belt. Each container stops at an average of 5-10 stations, loading the company’s 30,000 kinds of goods, such as screws, bolts and protective covers.
Wurth installed 40 UHF readers on the 1.5km picking line
Wurth always uses 40 readers, installed at different points on both sides of the conveyor belt. However, Kansala stated that only 20 of these readers were installed near the picking station. Others are installed at the starting point of the conveyor belt, etc. These readers collect the data passing through the tags, so that the Wurth manager can view the flow path of each container on the conveyor belt in real time, and if necessary, give priority to specific containers to move forward.
“The manager can see the flow map of each container,” Kansala said.
According to Kansala, Wurth decided to install a system that stores the command data transmitted by the conveyor belt in the label instead of an external database, because the company is very satisfied with the way the existing system works and does not want to redesign the process. In addition, the old and new systems will run simultaneously during the technology transfer. In addition, Wurth also wants the picking station to operate independently of network connectivity-that is, it does not rely on WLAN or cable connections to the back-end system.
The system was designed and tested in the fall of 2009, and the first new reader was officially installed in January 2010. Vilant will gradually add new readers until the project is completed this month.
RFID reader identifies each container passing by
For Kansala, the challenge of this project is to implement the new RFID system while also running the old system, which delays the factory’s picking line.
“During the first period of operation of the new system, we did not affix UHF and LF tags to the containers at the same time. We replaced the old readers with new readers one by one,” Kansala explained. “We must also ensure the data consistency of the new and old labels of the container. If you design from scratch The new system will not have this problem.”
Manager Wurth plans to use the data collected by the new system to quantify how often each picking station is used, Kansala said. This type of information helps them maximize the use of various picking stations and eliminate picking bottlenecks.
Later, Kansala also plans to use an RFID system to eliminate all paperwork in the picking process. At present, the staff at each site check the picking list, put the goods in the container, and use a pen to mark the completion of the task on the list. After adopting the new system, employees can use handheld readers to complete this type of work.
Kansala declined to disclose the investment cost of the system.
[ad_2]