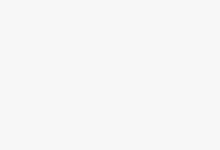
Schweppes distribution center in Australia adopts voice sorting system
[ad_1]
company profile
The iconic brand Schweppes has been providing high-quality non-alcoholic beverages to Australians for 150 years. The outstanding bubble bottle technology was pioneered by Mr. Jacob Schweppes in Switzerland in 1783 and brought to Australia in 1850. Schweppes’ first factory was established in Sydney in 1877.
Today, Schweppes Australia has become a beverage giant, with 1,800 employees, 11 production bases and 12 distribution centers nationwide. The company produces some of Australia’s favorite and popular beverages, including Schweppes, SOLO, Cottee’s, Spring, Valley, Pepsi and Gatorade.
Schweppes distributes beverage products to more than 30,000 customers in Australia. One of its largest distribution centers, the Archerfield site, is located in Queensland and serves most of the state’s markets. Every day, more than 40 employees pick 16,000 boxes of products and ship them to more than 5,000 customers.
challenge
Accurately locate products and eliminate repetitive work
Until recently, the Schweppes Archerfield distribution center still used a paper picking system, and it was planned that each loading process would take an employee up to 15 minutes. Because the descriptions of many products are similar, it is easy for employees to misread the information and lead to errors in delivery. Because each picking location stores multiple stock keeping units (SKU) and pallets, inventory tracking is also difficult.
In order to prevent errors and inefficiencies caused by the original paper picking system, Schweppes Australia decided to implement a fully integrated voice-guided solution.
According to Danny Murphy, Executive Manager of National Logistics of Australia Schweppes, what Australia Schweppes has to do is more than just replacing the paper system.
“Our goal is to establish a fully integrated system that eliminates repeated handling of pallets and avoids repetitive tasks without added value, while providing managers and supervisors with visibility into the workplace and creating a safer working environment for employees.” Murphy said.
solution
Automation brought by Vocollect voice
In the Vocollect voice solution, the system provides employees with pallet labels, and employees speak to the system and receive voice prompts to guide them to the correct picking location. When walking to the location, the check code will be used to verify whether the location is correct or not-to eliminate employees’ doubts about the location. Then, the voice system prompts the employee how many boxes of goods to pick, and the number of items that the employee needs to pick repeatedly to the system.
The automated features of Vocollect voice solutions enable Schweppes employees to complete training in a relatively short period of time. Now, it only takes 10 minutes to set up a voice template for new employees, and it only takes 20 minutes to train new employees on the product series. In contrast, when using the old system, employees need to spend up to two weeks training to be confident to complete the task of picking independently.
result
The seamlessly integrated system delivers customer orders more accurately and quickly
The implementation of Vocollect’s voice solution establishes an automation that can reduce 90% of the error of picking by box, and at the same time solve the problem of product identification, which was a major challenge for Archerfield warehouses. When using a paper system, employees need to identify 400 different products in the warehouse—some of which have very similar packaging, such as Pepsi® and Pepsi Max®.
The productivity of Schweppes employees has also been improved, especially in the product replenishment process, where the picking rate has increased by as much as 20%.
The real-time visibility provided by the Vocollect voice solution enables viewing of each employee’s shift. Based on the accuracy and productivity data provided by the new system, management can now clearly determine which product each employee is picking, the rate of picking, and how much it has completed Work. Managers used to manually check the paper orders completed by each employee every day, but now they only need to press a button to access any employee’s comprehensive productivity report at any time.
Nathan Lucinsky, manager of the Archerfield Distribution Center, also witnessed greater accuracy during the order fulfillment process.
“We can now calculate the workload requirements at the beginning of the day, and then allocate free labor based on this information, instead of waiting until the end of the day to know how much work remains unfinished and still need to continue. The new system allows us to It is more accurate when delivered to customers,” Lucinsky said.
Schweppes believes that the biggest benefit of Vocollect’s voice solution is its seamless integration with the warehouse management system. As a result of the implementation of voice, they can activate a more efficient and accurate real-time replenishment system, perform stronger batch control on the picking surface, and provide employees with a safer working environment.
Safety first
Voice is very suitable for the operation and operation of Schweppes distribution center, because voice can free hands and allow operators to pick freely. In contrast, paper technology requires paper, scanner or label to be handled by hand, and drivers do not need to check and pick while driving. List, but receive all instructions through the wireless Bluetooth headset, without distraction.
“Safety in the workplace is paramount-we need to ensure that employees work in a safe environment. Under the old system, forklift operators often looked down at the picking list when driving in the warehouse. Under the new system, There is no paper, so they raised their heads and looked around to ensure safety before driving through.” Nathan Lucinsky, Manager of Archerfield Distribution Center, emphasized.
Schweppes fully automated
The Schweppes Archerfield Distribution Center is not the only winner in implementing the Vocollect voice solution. Improvements in efficiency, productivity, visibility, and safety have enhanced the overall performance of the site’s supply chain-this advantage is ultimately passed on to customers, and customers also benefit from faster and more accurate delivery.
The employees of Schweppes Archerfield are also very satisfied with the solution. They believe that the manager’s investment is very valuable, allowing them to use the most advanced technology, thus making work easier and safer.
Future plan
In view of Archerfield’s success, Ian Gatenby, general manager of logistics and customer service at Schweppes Australia, plans to roll out Vocollect voice technology nationwide.
“We hope to extend the advantages we saw in Archerfield to our entire network. Ideally, the picking standards at the Archerfield site will become the picking standards in Australia. We have seen a series of productivity, quality and safety Sexual improvement. More importantly, we have also seen the benefits for customers. At Archerfield, our experience is great, and I strongly recommend using this technology in all our distribution centers. I think it’s us Become another milestone on the road to best practice workplaces.” Gatenby said.
[ad_2]