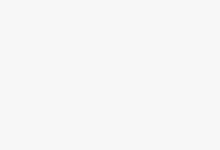
Successful Cases of Ling Frog Wireless Warehouse Management System
[ad_1]
User: Nabisco Foods (Suzhou) Co., Ltd. (Fortune 500 companies)
Nabisco Foods (Suzhou) Co., Ltd. was established in November 1995 with an investment of 50 million U.S. dollars in Suzhou for Nabisco, a Fortune 500 company. Advanced production equipment and technology have laid a solid foundation for it. The main products are cookies and other baked goods. Several main products occupy a leading market share in China. Now more than 300 employees are working hard and confident to become the number one in China.
Our company started to implement barcode-based wireless warehouse management system for Nabisco’s warehouse in the second half of 2004. The project was completed within the year and is now officially put into operation.
The product of an enterprise determines the complexity of its raw materials. Unlike general enterprise warehouses, the materials stored in this warehouse include both box-type packaging and fluid-type raw materials stored in tanks, and there are also conventional pallets in and out of the warehouse. And the pipeline in and out of the warehouse in two ways.
Before the implementation of WMS, warehouses were simply partitioned, and materials of various types and forms were not stored in a fixed area. Warehouse employees were often unable to accurately find and distinguish materials, and materials were not strictly processed in batches after they were put into the warehouse. Management, some raw materials have not been used for a long time or even expired and deteriorated, resulting in a certain amount of waste of resources.
There are many types and specifications of materials used in production. Traditional manual entry and exit records and inaccurate storage locations limit the speed of entry and exit operations, which form a strong contrast with advanced high-speed production lines and become a bottleneck for enterprise internal logistics.
There is also an important problem in the warehouse. The production in the workshop is three shifts and it is rotated 24 hours a day. This requires the warehouse to work synchronously. Therefore, the warehouse cannot carry out accurate inventory at all. It can only use the inventory during the break of the production line or the employees in and out of the warehouse. A rough inventory is carried out at the same time as the operation, and the warehouse inventory data and the actual value have always been large deviations. Inventory data is the basis of the ERP system and is an important data. Inaccurate inventory data has also caused some ERP functions to be useless. Leaders at all levels of the enterprise are also troubled by it.
In view of the specific situation of the warehouse, after nearly two months of on-site investigation by the Shanghai Lingfrog implementation personnel and many discussions between the two parties, it was finally determined that two material forms (box type, fluid) are compatible, unified zoning codes, and wireless for dynamic inventory. Warehouse management system solution.
The system has customized some customized functions on the basis of the Lingfrog warehouse management system LINX-WMS2.0. It uses wireless data collection terminals and barcode printing equipment to unify the barcodes and formats of materials, and establish batches for raw materials and finished products. The comprehensive bar code management of materials, the materials are strictly according to the batch first in, first out.
The warehouse is divided into locations, materials and warehouse locations are strictly corresponded, and management is standardized. Access and inventory operations are carried out by wireless handheld terminals. At the same time as the actual operation, the data of access and inventory is also automatically entered into the system to increase the operating speed. The system designates the batch and location of the materials to be issued according to the material issuance form, which not only increases the speed of material distribution, but also reduces the errors of material distribution.
Integrate with ERP to establish a continuous logistics system from procurement to production. Warehouse inventory data, inbound and outbound, and transfer data are fed back to the ERP system in a timely manner, and inventory early warning is established, so that the functions of the enterprise information system can be fully utilized.
The system has designed a sophisticated algorithm to realize the dynamic inventory of the warehouse without shutdown. The dynamic inventory function based on automatic identification technology makes the inventory operation no longer need to be stopped, but at the same time as other warehouse operations. The warehouse has actually achieved 7 *24 continuous operation is consistent with the rhythm of the production line.
For the materials in and out of the pipeline, the equipment data automatic collection function was established in the implementation, and corresponding solutions were designed according to the characteristics of the pipeline fluid.
After the implementation of the system, the company’s inventory accuracy rate increased to 99.8%, and through the interaction with the ERP data, the accuracy of the implemented inventory data in the ERP was ensured. Barcode scanning is adopted for in and out of the warehouse, which is fast and accurate in data. After more than a year of use, there has been no error in materials in and out of the warehouse during manual operations. At the same time, after adopting batch management, it has realized first-in-first-out, accelerated inventory turnover rate, and reduced the occupation of inventory funds.
[ad_2]