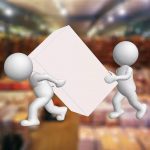
The process of electronic label picking in smart warehousing
[ad_1]
With the development of information technology, the production management methods of modern manufacturing enterprises are becoming more and more intelligent, and warehouse management is no exception. As an important part of enterprise management, warehousing management is an important means to ensure timely, accurate, and effective supply of materials in the production process, and it can help enterprises reduce costs and increase efficiency, and achieve refined management of warehousing.
In the scope of operations covered by smart warehousing, picking has always been a very important part of it, which often requires a lot of manpower and material resources. In traditional warehousing management, the company’s investment in picking operations accounts for a large proportion, almost close to half of the overall warehouse operating costs. However, the actual effect is not very satisfactory because the warehouse pickers spend a lot of time looking for the warehouse. In terms of position, the efficiency of picking is very low.
In order to continuously improve the efficiency of picking, increase production efficiency, and meet the individual needs of enterprise production management, choosing to introduce the Smail electronic label picking system can effectively solve the above problems. The electronic label picking system is a series of electronic display devices installed on the shelf positions to assist the pickers in the work. It is generally deployed based on the technical principles of orders or batches, which is the so-called “fruit picking” and “seed picking” “. Below we will explain how the electronic label picking system improves the efficiency of picking from the process and strategy of electronic label picking in smart storage.
The general process of warehousing and picking operations
The system places an order → generates a picking strategy → outputs a picking list → plans the picking path → picks → confirms completion and opens a new order
It can be seen from the above process that in warehouse management, each process of picking is initiated and driven by the production order of the company, and then the picking path is optimized according to the warehouse layout, and the whole process is scheduled according to the production organization mode of the company. After the warehouse receives the order instruction, the system will select the appropriate picking strategy according to the production scheduling requirements: order-based picking or batch-based picking.
1. Order-based picking (fruit picking)
This is the most basic picking method in smart warehousing. The system will decompose each customer’s order into picking lists according to the storage layout, assign them to pickers in different areas, and generate picking routes. After the pickers pick up the goods, they will be sent to the centralized area for consolidation. After rechecking and confirming, they will be handed over to the next delivery process. The pickers will continue to complete new picking orders.
2. Based on batch picking (seeding picking)
Seed picking is a common picking strategy, which can further improve the efficiency of picking and reduce the intensity of picking. After receiving new picking requirements, the system will summarize several orders, classify and merge the same items, and then compile picking lists according to the storage layout, assign them to pickers in different areas, and generate picking routes. After the pickers pick up the goods, they send them to the corresponding item area. In this area, according to the needs of the production organization, the combination can be picked again according to the order, or it can be directly reviewed and handed over to the next delivery process.
In general, the electronic label picking system is applied to the shelf, which can realize the intelligent picking operation, improve the picking efficiency, reduce the labor intensity of the operators, reduce the error rate, reduce the number of employees, and improve the delivery efficiency. It has the incomparable advantages of other sorting methods, so it has broad application prospects in the industries of commercial chain, medicine circulation, household appliances, electronic assembly, food and beverage, auto parts and other industries.
[ad_2]