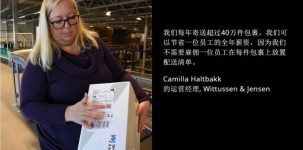
The shipping label of the QR code improves the delivery process
[ad_1]
Wittusen & Jensen, a Norwegian office supplies and consumer goods wholesaler, prints a QR code on the Consignor shipping label. This allows them to save time and costs when sending packages, while providing a better overview of the consignment.
If QR codes and parcel processing can be more efficient and cost-effective, then Camilla Haltbakk and Consignor, operations managers of the Wittussen & JensenIT department, will discover how the two can be unified in a smarter solution in a feat in 2015.
“We are already using Consignor to print shipping labels, transmit data to carriers, and add QR codes to existing labels. Now, when customers receive our packages, they can scan the QR code and see Electronic delivery notifications with complete consignment information. This way, they can more easily track consignments divided into multiple deliveries,” said Camilla Haltbakk of Wittusen & Jensen.
But the QR code of the shipping label is not only an advantage for the recipient of the package. At Wittusen & Jensen, with the QR code label, they can save time and cost when sending packages.
“We send more than 400,000 packages every year. We can save an employee’s annual salary because we don’t need to hire an employee to put a distribution list on each package. We also save paper, toner and printers. Maintenance costs. In addition, the number of customers asking about parcel delivery has decreased because they can see the complete delivery process through the electronic delivery list, which goods are booked and delivered,” Camilla Haltbakk said.
Wittusen & Jensen automatically prints and uses QR codes through hydraulic printers on warehouse conveyor belts and forklifts during the sorting process.
Consignor and Apport automatically print labels
At Wittusen & Jensen’s central warehouse on the outskirts of Oslo, when they printed and used cargo labels with QR codes on consignments that were picked up by robots, packaged by warehouse employees, and ready for shipment, “Wiiifffsvushpuff” was the sound of a hydraulic printer.
“We also print labels on the forklifts that are used in the warehouse to collect bulky goods. In this way, they can save time because the goods will receive shipping labels when they are collected. Consignor can ensure that by retrieving transportation data from the order system The forklift printer printed the correct shipping label,” Camilla Haltbakk explained.
In addition to automatically printing shipping labels with QR codes, Wittusen & Jensen saw many other advantages of using Consignor as its delivery management system.
“No matter what distribution method we use, Consignor ensures that the transportation data we transmit to the carrier is of high quality. You can say that Consignor is a package of rules that track all the carrier’s regulations. In this way, we can ensure that every carrier is satisfied. It’s not necessary to track it on its own. In short, Consignor ensures our delivery to our customers,” Camilla Haltbakk concluded.
Instance
· Wittusen & Jensen was founded in Norway in 1897 and is headquartered in Oslo.
· Wittusen & Jensen already has 200 employees and operating income exceeds 600 million Norwegian kroner.
· Witussen & Jensen’s office supplies and sales products are exported to workplaces and offices in Northern Europe.
· Norwegian goods wholesaler Asko and e-commerce market komplett.no are customers of Witussen & Jensen.
· Wittusen & Jensens central warehouse is located in Berger on the outskirts of Oslo.
· The central warehouse has 22 employees, and the collection and packaging of goods are carried out by robots and staff.
· Wittusen & Jensen uses the Consignor On-premises interface to automatically print shipping labels with QR codes and transmit the data to the carrier. Consignor On-premises is integrated into their Apport WMS.

Camilla Haltbakk showed a QR code shipping label printed by a hydraulic printer on a conveyor belt just now.
[ad_2]