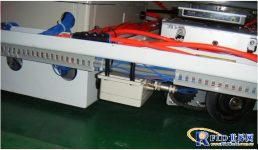
UHF RFID Automatic Guided Vehicle (AGV)
[ad_1]
◆Case introduction
AGV is the English abbreviation of Automated Guided Vehicle. Refers to a transport vehicle equipped with electromagnetic or optical automatic guidance devices that can travel along a prescribed guidance path, with safety protection and various transfer functions. AGV belongs to the category of wheeled mobile robots (WMR-Wheeled Mobile Robot) . Equipped with electromagnetic or optical automatic guiding devices, which can drive along the prescribed guiding path, have safety protection and various transfer functions, transport vehicles that do not require a driver in industrial applications, and use rechargeable batteries. Its source of power. Generally, it can be controlled through a computer to control its path and behavior, or use an electromagnetic path-following system to set up its path. The electromagnetic track is pasted on the floor, and the unmanned vehicle follows the electromagnetic track. The message moves and moves.
Compared with other equipment commonly used in material transportation, the activity area of AGV does not need to lay fixed devices such as rails and support frames, and is not restricted by venues, roads and space. Therefore, in the automated logistics system, it can fully reflect its automation and flexibility, and realize efficient, economical, and flexible unmanned production. Traditional AGV uses LF or HF for positioning, which has problems such as poor speed adaptability, inconvenient data modification and maintenance, and UHF technology can overcome these shortcomings.
◆Key Process
Labeling:Put an electronic label representing position information beside or below the guiding track, such as a workstation or intersection; install the reader on the AGV to communicate with its controller (such as PLC), and feedback the collected position information To the control system;
position: The AGV vehicle-mounted reader/writer recognizes the tag location information and sends it to the controller for processing, so that the AGV vehicle can transport the items to the correct location.
◆Equipment configuration
Reader: According to the on-site environment and the requirements of the controller communication interface, it can be equipped with a high-protection, integrated, high-performance SR-8300B (RS-485) or 8100B (RS-232) industrial-grade reader; or according to customer requirements Require custom reader kits to be integrated into its control system;
electronic label: Can be equipped with buried tags or thin electronic tags attached to the surface.
◆Implementation benefits
1. It can adapt to the positioning requirements of high-speed AGV movement, and reliably identify the position information of the tag at a speed of 1m/s;
2. The label data is easy to modify, easy to replace, and simple to maintain;
3. It can adapt to the modification and resetting of the transportation route, with better flexibility and adaptability.
◆Case
The high-speed AGV UHF RFID identification and positioning system of an enterprise in Jiangsu has been operating reliably for one year.
[ad_2]