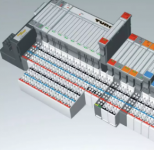
Factory automation based on CODESYS modular system and RFID technology
[ad_1]
Austrian factory designers use Turck’s RFID radio frequency identification system to provide automatic cleaning services for animal transport vehicles. After using RFID technology, when the driver uses a high-pressure cleaning device, a powerful solution can record water consumption, detergent consumption and Data such as cleaning time.
Whether it is a cable car ticket, a hotel room card or a hot spring bath admission card, the application of radio frequency identification technology is very common in daily life.This convenient identification technology is also used more and more in the industrial field. For this reason, Turck has developed a modular system based on CODESYS, Independent of the PLC manufacturer, can be connected to almost all control systems. When providing automatic cleaning services for animal transport vehicles, the type of transport and the time registration of the cleaning process are automatically identified by the RFID key. Only when the chip is considered “yes”, the water pump can be started. Ness-Schneider was founded in 1994 and is located in Grünau, Vienna, Austria. The company was originally a trading company providing sewage treatment components, but over the years it has developed into a manufacturing enterprise. In 2004, the company was acquired by NTA, a factory manufacturer specializing in the food industry. Since then, the business has been privately owned by the Steinmaurer family. Today, Ness-Schneider is a research-oriented company that provides services to drinking water supply plants, mainly providing environmental protection equipment and components for sewage purification systems. Ness-Schneider’s customers mainly come from the food industry. “We provide a complete set of design solutions for sewage treatment plants-from biological treatment technology to project management, development and construction, and provide specific machinery and equipment and on-site installation and commissioning services. “In this process, we act as the general contractor.” Managing Partner Walter Steinmaurer explained, “Only in the construction process (such as concrete works) do we hire partners. All other work comes from us.” He emphasized that “we rarely build for the community. Sewage treatment plants are more focused on industrial wastewater treatment. “
Powerful recognition system
“Satisfying the needs of customers is our daily work, and then usually generate solutions, these solutions will then be incorporated into our standard product series.” Steinmaurer said: “We often encounter scenarios that need to perform identification tasks, this is Why we have been looking for a suitable identification system, the system has been used as a mature solution, and is also expanding. After all, we will establish a long-term good partnership with suppliers. The company finally found Turck For many years, factory designers have purchased various components for measurement and control technology from automation experts in Mülheim. After a complete test phase, Turck’s modular RFID radio frequency identification system has proven to be perfect , And can meet all requirements. The first project of Turck system application is to upgrade the automatic cleaning station of slaughterhouse animal transport cleaning vehicles. According to the EU Sanitation Directive, the transport vehicles must be cleaned immediately after the animals are unloaded, and The generated sewage must be discharged into the sewage treatment plant. The operator of the slaughterhouse must provide cleaning facilities, although these facilities are costly, so the cleaning station is designed to be unmanned operation. The engineers of Ness-Schneider use Turck’s RFID technology has carefully designed a set of self-service high-pressure cleaning devices. The RFID tags used in this solution are very small, and each driver loads the “pass with time stamp” on the data carrier. If the RFID tag is placed on the RFID In front of the read/write head, the recognition begins. “All the data in the tag will be automatically read, such as the name of the driver and the transportation company, the license plate number, and any other data that you want to add. The system software checks whether the owner is authorized to use the cleaning station. “Steinmaurer said. If the recognition is passed, the lock on the hose box door will automatically open, and the driver can pick up the cleaning gun and start cleaning the vehicle, and the system will automatically record the water consumption, detergent usage and usage time. After use, You must roll up the hose and lock the door, and then place the label in front of the read/write head again to end the process. At this time, the driver will re-authorize the user, otherwise the cleaning station will not be available next time.
Industrial solutions that can be applied outdoors
This is an advantage of Turck’s RFID system, and it also allowed Walter Steinmarel to make the final decision. The RFID component shell is sturdy and meets IP20 and IP67 standards. The application temperature range is -25 to +85°C, which guarantees outdoor use. In addition, different FRAM data carriers (labels) provide different sizes and styles, and a well-designed modular system provides a fully encapsulated magnetic head that can be used to protect IP69K, RFID I/O modules and gateways, and other expansion hardware. “For us, an open control scheme is particularly important. Our factories are located all over the world, so we must be very flexible in terms of control hardware. Currently, we are using four different PLC systems.” Steinmaurer explained. “The Turck system can accurately connect these four PLC systems through standard fieldbus or through Ethernet. These gateways are developed based on the CODESYS development platform and use CODESYS IDE for unified programming. Because the interface is very open, the software can be directly connected. Integrated into the Ness-Schneider system. “I am very satisfied,” Steinmaurer praised. “Turck’s solution is very effective. We also received strong support from Alfred Frost, Sales Manager of Turck in Austria. We found a reliable partner. The system was developed in just a few days, and the invested work time was less than 100 hours. “The company is already considering the application of radio frequency identification systems to other industries. Walter Steinmarel finally admitted: “For example, in the process of delivering milk to a dairy plant, providing relevant documents and a traceable transport truck cleaning certificate is necessary”.
[ad_2]