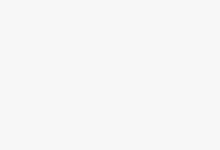
Ford applies RFID to car chargers
[ad_1]
Abstract: Ford Motor Company has begun mass production of electric forklift battery charging systems that use RFID technology in order to allow vehicles and their battery packs to transmit information to each other. To add data management capabilities based on RFID technology to the charging system, they also collaborated with ID Systems, a wireless asset tracking company based in Hackensack. With the RFID system, Ford can receive instant information about the battery and the charger itself, so that the data can be transmitted more quickly and cost-effectively.
Ford Motor has begun mass production of electric forklift battery charging systems that use RFID technology to enable vehicles to transfer information to and from their battery packs. AeroVironment, the manufacturer of the charging system, said that this plan will be environmentally friendly, and it can streamline information to vehicles through its 42 manufacturing plants.
In order to add data management capabilities based on RFID technology to the charging system, they are also cooperating with ID Systems, a wireless asset tracking company located in Hackensack (U.S. city). According to Gregory Smith, the order they have started is for 500 RFID-based data monitoring devices.
Electric forklifts are much cleaner to operate than gas forklifts, but they need to be charged frequently. In order to be able to charge from time to time, the operator of the forklift has to repeatedly drive it into a charging room, replace it with a fully charged battery, and then charge the battery without electricity.
With Aero Vironment’s PosiCharge charging system, the driver only needs to drive the forklift to the front of PosiCharge when he is resting, insert it into the forklift, and charge it during a rest or lunch. While the forklift is charging, the driver connects another wire to the power source, so that the functionality of the battery itself and the power level of the forklift can be transmitted. The charger will keep this data with Ford employees. Before installing the RFID system, the staff can connect the charger to the portable computer and retrieve the data again. However, distributing portable computers suitable for chargers to employees requires additional expenses.
For the past five years, Ford has been using an older version of the PosiCharge system in some of its factories. This year, the PosiCharge department of AeroVironment cooperated with ID Systems, and as a result, a new PosiCharger was produced, each PosiCharger has a charging monitoring point (CHAMP). In this way, an RFID device can transmit data of different frequencies through a low-power narrow ISN band from 1000 feet away from the charger.
Each CHAMP consists of a microcomputer and an RFID antenna. Moreover, each CHAMP has a unique ID number used to track its location and activities. CHAMP transfers its ID number and forklift battery data to the formation management gateway of ID Systems. These gateways, which are used to store and process data, and can also be programmed with their own firmware, will be deployed in every factory, Smith said. Through the Ethernet connection, the data is transferred to the database so that Ford employees can access it. These data can tell them the activity and location of each charger and the charging status of the forklift battery pack.
“In the past five years, Ford has foreseen the value of collecting data on chargers and battery power through the use of RFID.” said Jordan Ramer, director of Aero Vironment’s investment industry development department. With the RFID system, Ford can receive instant information about the battery and the charger itself, including the condition of the battery itself, the fault of the charger, the temperature of the battery pack, the frequency of the charger, and the charging time. By using RFID, the system can allow individual tracking of chargers and their activities and their locations. In this way, data transmission can be made more quickly and cost-effectively.
Ford is PosiCharge’s first customer and has been working with it since 2000. Steve Ache, deputy general manager of Aero Vironment’s sales department, said, “We have applied this charger to many Ford factories.” Ford decided to promote this system in factories throughout North America, thereby canceling the original Gas forklift. This process will be carried out in 2005. By using the RFID system, for the first time, Ford employees have access to the required information, so that the company can learn about the use of forklifts more quickly.
Prior to this, the Ford Motor Company of the United States has begun to apply RFID technology to the battery charging system (AeroVironment’PosiCharge) of electric vehicles. The new system combined with RFID technology can transmit vehicle operation and battery usage to the operator in time. This new system will soon be rolled out in 42 manufacturing plants owned by Ford Motor Company.
Compared with ordinary cars, electric vehicles have higher environmental performance, but the disadvantage is that they need to be charged in time. Therefore, drivers who drive such cars have to often go to a fixed charging location to charge the car, and they also need to charge the car. Remove the battery. In order to make up for the weaknesses of electric vehicles in this regard, Ford Motor Company has cooperated with AeroVironment, a manufacturer of charging system products, to develop an electric vehicle charging system based on RFID technology. The system shortens unnecessary time and greatly improves charging efficiency.
[ad_2]