
Detailed explanation of automatic guided vehicle positioning and guidance design based on RFID technology
[ad_1]
0 Preface
For the AGV (Automated Guided Vehicle) for object handling, guidance and positioning are the key research parts.Commonly used guidance methods are magnetic guidance[1], Visual guidance[2], Laser guidance[3]Etc. There are two-dimensional code positioning[4], RFID radio frequency identification positioning[5], Ultrasonic positioning, etc. Among them, the magnetically guided magnetic stripe is convenient to lay, the path is easy to change, the radio frequency identification is not easy to pollute, and has no interference with sound and light. Therefore, the magnetically guided AGV with integrated RFID technology is widely used in automated production and transportation.
Many scholars have conducted research on RFID technology in magnetic guidance.Gu Jiawei and others[6]AGV navigation is realized by writing the tag number and motion control parameters in the electronic tag.Li Ji[7]Use RFID to assist positioning and use the transverse magnetic strip to complete vehicle turning, parking and other actions.Luo Yujia[8]The AGV turning action mode is fixed, and the tag information is used to realize turning 90° and 180°.
Most of the above-mentioned documents write action instructions in electronic tags. Because the stored instruction information is single and the tag utilization rate is low, more tags need to be arranged when the actual path is complicated, which is not conducive to path planning and guidance. Based on previous studies, this paper aims to solve the AGV guidance problem under complex paths, and proposes a vehicle action command algorithm. The action command is generated according to the scheduling task and stored in the on-board control system. The label is only used as position recognition to improve the vehicle. Driving flexibility.
1 Driving map modeling
1.1 Map composition
The map is composed of guiding magnetic strips and stations, as shown in Figure 1, which are represented by lines and rectangles respectively. g represents workstations, the number is h, and number them according to formula (1) (the number on the right side of the small rectangle in the figure), the set of workstations can be expressed as G={g1, g2, g3,…, gh}. l represents the line, the number is n. It is stipulated that the horizontal and vertical line numbers are represented by even and odd numbers and numbered according to formula (2) (the number in the circle in the figure). The line set is L={l1, l2,…, ln}.

The application scenario based on this article stipulates that the AGV travels backwards in all other situations except for the forks when entering the station, and slows down when entering the station.
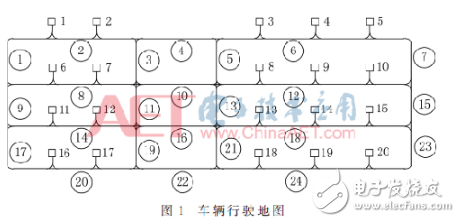
1.2 Arrangement of electronic labels
1.2.1 Arrangement of relevant labels for workstations
In Figure 2, pi1, pi2,…, pi7 represent the position of the electronic tag. Figure 2(a) shows that the AGV enters the station gi from the left when it goes straight. It is stipulated to decelerate at pi3, pi5, pi4, and pi7 respectively, change from backward driving to forward, forward, turn right, and stop. Figure 2(b) shows that the AGV retreats and turns left out of the station. It goes straight, backwards, and accelerates at pi7, pi6, and pi1 respectively. The entry and exit of the AGV from the right side of the station is similar to that of the entry and exit from the left side. Define pik as the k-th label (k∈{1,2,…,7}) related to the station gi, arranged as shown in Figure 2, and its composition is represented by the matrix S1 as:
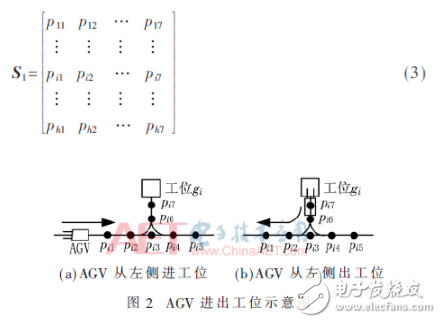
1.2.2 Line label layout
Place two electronic labels at each end of each line. Sja represents the ath label on the line lj, a={1, 2, 3, 4}. It is stipulated that Sj1, Sj2, Sj3, and Sj4 are sequentially arranged along the positive direction of the coordinate axis on lj, and the line segment between Sj1 and Sj4 is the range of line lj. The vehicle executes turning instructions at Sj1, Sj4 to enter other lines, executes acceleration or deceleration instructions at Sj2, Sj3 to accelerate when entering lj, and decelerate when leaving lj. The labels on all lines are represented by the matrix S2 shown in equation (4), and the layout of all labels in the final map is shown in Figure 3.
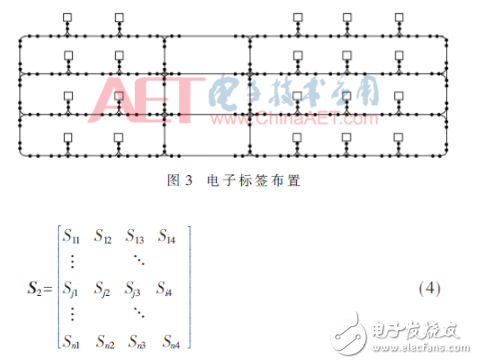
2 Action command algorithm
First encode the tags, then determine the order of passing each tag according to the scheduling path, and finally generate action instructions according to the tag ordering.
2.1 Electronic label coding
The electronic label coding format is shown in Figure 4, where x and y represent the coordinates of the label in the map,’pro’ represents the attribute, that is, the type of action instructions that the vehicle can execute at the label,’line’ represents the line where it is, and’sit’ Indicates the relevant station number. According to the driving mode of the AGV on the line, it is stipulated that the’pro’ bit of Sj1 and Sj4 is ’01’, which means turning, and the’pro’ bit of Sj2 and Sj3 is ’02’ which means acceleration and deceleration. The’line’ bit of Sja is the line number j, and the’sit’ bit is represented by zero. The’pro’ bit of the label pik is represented by Table 1 according to the way the AGV enters and exits the station. The’line’ bit is the line number where pi1 is located, and the’sit’ bit is the related station number i.
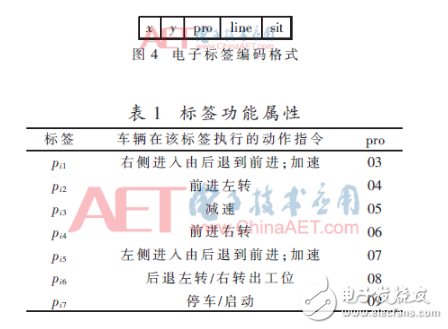
2.2 Path establishment and selection
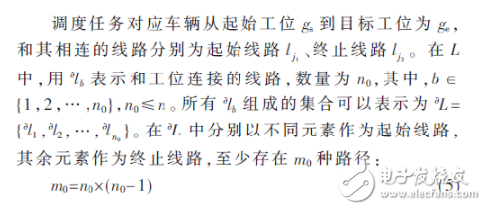
Among them, w represents the path, the number is m (m≥m0), then the matrix composed of all paths can be expressed as W=[w1,w2,…,wm]T. ltx represents the xth route of the path wt, where wt={lt1, lt2,…,ltx,…}, t∈{1,2,…,m}, ltx∈L, set the route included in the tth path If the number is the largest and is n1, then W is an m×n1 order matrix. For the number of lines less than n1, the insufficient part is represented by 0, and the path matrix is represented by formula (6):
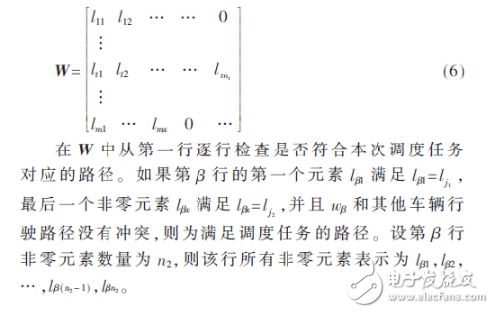
2.3 Dispatching path label sorting method
For the labels on any two connected lines, the first and second lines are represented by lu and lv respectively. The labels on lu are Su1, Su2, Su3, Su4, and the labels on lv are Sv1, Sv2, Sv3, and Sv4. r0 represents the sequence of tags passed from lu to lv. Suppose the coordinates of Su1 are (x1, y1) and the coordinates of Sv1 are (x2, y2). After comparing the two coordinates, the relative position relationship between lu and lv can be inferred:
The first case: x1》x2, y1》y2, as shown in Figure 5(a) and Figure 5(b), r0={Su4, Su3, Su2, Su1, Sv4, Sv3, Sv2, Sv1}.
The second case: x1 “x2, y1 “y2, if lu is an odd number, r0={Su1, Su2, Su3, Su4, Sv4, Sv3, Sv2, Sv1}, corresponding to Figure 5(c); otherwise r0={Su4 , Su3, Su2, Su1, Sv1, Sv2, Sv3, Sv4}, corresponding to Figure 5(d). In the same way, the arrangement of r0 elements can be inferred in the other cases.
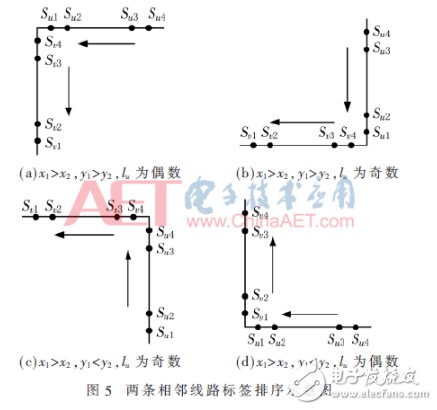
For the path wβ, first select the labels on each section of the route according to formula (4), and then arrange them in the order in which the vehicles pass each label on the route. The steps are as follows:
(1) Regard lβ1 and lβ2 as the first and second lines respectively, and determine the positional relationship between the two based on the coordinate relationship. Sort according to the two line label sorting rules, and put the sorting result in the array r1;
(2) Regard lβ2 and lβ3 as the first and second lines respectively for sorting, and add the sorting result of the lβ3 label to the array r1;
(3) Arrange the tags for the lines lβ3, lβ4, lβ4, lβ5,…, jsj3-t6-s1.gif in sequence similar to step (2).
According to the way the AGV enters and exits the station, delete the tags in r1 that have not passed on lj1 and lj2. At this time, the number of elements in r1 is represented by b1.
2.4 Action instructions
The action instruction format is shown in Figure 6, the first 5 bits are the electronic label code, and the’ins’ bit is the action instruction executed by the AGV at the label corresponding to the first 5 bits, which is coded according to its function, as shown in Table 2. During the process of the AGV from the start station gs to the target station ge, it travels in the order of leaving the station, driving on the path, and entering the station. The RFID reader continuously reads the ground tag information and transmits it to the on-board control system. The instructions are executed sequentially according to conditions to complete the scheduling task, and the condition is that the currently read tag information is consistent with the tag code bit of the instruction to be executed.
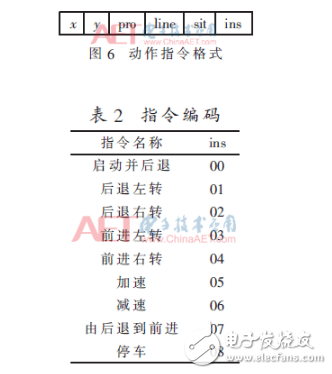
2.4.1 Out of station action instruction
R1 represents the set of station motion instructions. If the AGV exits the station from the left, add ’00’, ’01’ and ’05’ after the label code of ’09’, ’08’, and ’03’ in the’pro’ bit of S1 row S, respectively, otherwise Add ’00’, ’02’ and ’05’ after the tag code with the’pro’ bits in the S row of S1 as ’09’, ’08’, and ’07’ respectively, and they will be used as the first, second, and third place in R1 in turn Action instructions.
2.4.2 Path Action Instructions
Respectively determine the action instructions for the b1 tags in r1 by pressing the’pro’ bit. R2 represents the path action instruction set, and Figure 7 is its judgment flow.
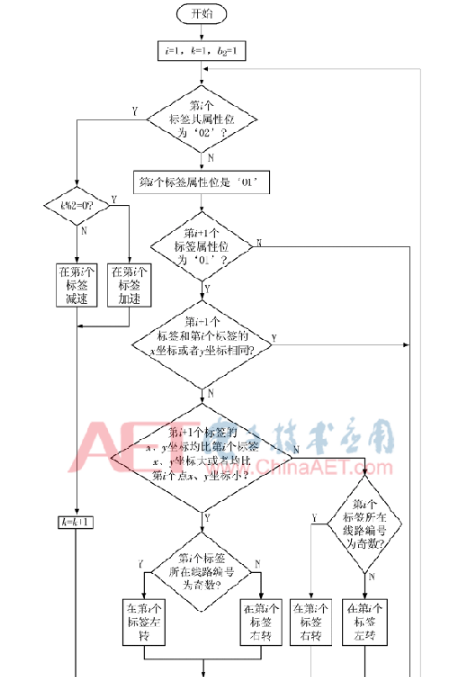
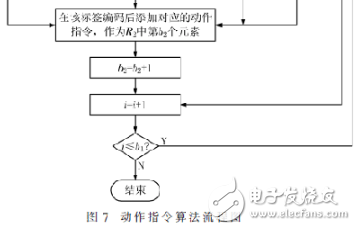
2.4.3 Into the station action instruction
R3 represents the set of station motion instructions. AGV enters the station from the left, and add ’06’, ’07’, and ’04’ after the label codes with ’05’, ’07’, ’06’, and ’09’ in the’pro’ position of row e of S1 , ’08’; otherwise, add ’06’, 07′, ’03’, and ’08’ after the label encoding where the’pro’ bit of the line is ’05’, ’03’, ’04’, and ’09’ respectively, And as the first 1, 2, 3, and 4 instructions in R3 in turn.
The complete instruction set of each execution task is represented by R, then:

3 Test results and analysis
In Figure 7, select stations 12, 13, 17, and 18 for testing. The label code is shown in Figure 8. The first two digits are the x-coordinates, the 3rd to 4th digits are the y-coordinates, the 5th to 6th digits are attributes, the 7th to 8th digits are the line numbers where they are located, and the last two digits are related to it. Station number.

The vehicle action instruction program was written in VC++6.0, and the model car based on the ARM architecture and integrated with the RC522 radio frequency identification module was selected as the test object. Figure 9 is the actual vehicle operation diagram after laying the guide wire and placing the label. The test shows that the vehicle can complete the dispatch task according to the expected purpose. Figure 10 shows the guidance method for writing action instructions into the tag. The AGV completes acceleration and deceleration by executing the instructions in the tag. Since the internal command information of the ground tag has been determined after the placement of the ground tags, the vehicle can only complete a certain fixed action when passing each tag, and the guidance method is relatively simple and the flexibility is poor.

Select different starting station and target station to combine to represent different scheduling tasks. In C++6.0, the result of each operation is shown in Figure 11. The first 10 digits of each action instruction are the electronic label code, and the last two The bit is the action performed by the AGV on the tag.
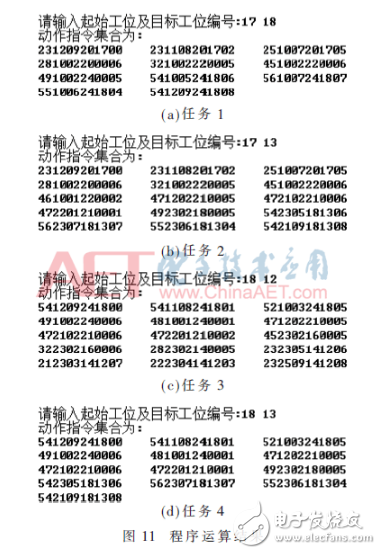
From Figures 11(a) and 11(b), it can be seen that the driving routes of tasks 1 and 2 are 20→22→24, 20→22→21→18, respectively. The AGV has passed the label 4610012200, and there is no corresponding label in task 1. Instruction, the AGV does not execute any instructions here, and keeps going straight from line 22 to line 24; the instruction corresponding to this label in task 2 is 461001220002, and the last two digits ’02’ indicate that the AGV is here to turn right back and turn right by the line 22 enters line 21. The comparison can be obtained: AGV only executes the instruction at the tag that meets the execution conditions of the action instruction.
From Figures 11(c) and 11(d), it can be seen that the driving routes of tasks 3 and 4 are 24→21→16→14, 24→21→18, respectively. The AGV has passed the label 4722012100, and the AGV in task 3 corresponds to this label. The command is 472201210002, the last two digits ’02’ means that the AGV is here to turn right back and enters the line 16 from line 21; the command corresponding to this label in task 4 is 472201210001, and the last two digits ’01’ indicate that the AGV is here Go back and turn left, take line 21 and enter line 18. Comparison can be obtained: AGV can execute different instructions on the same label when completing different tasks, which increases driving flexibility.
4 summary
In this paper, electronic tags are used as location recognition, and the action instructions are generated by algorithms based on specific tasks and stored in the on-board control system, so that the vehicle can execute different action instructions when passing the same electronic tag in the process of performing different tasks, which makes up for the traditional In the navigation mode, the driving route is fixed and the execution instruction at the label is single. This method solves the problem of vehicle guidance under complex paths, improves driving flexibility and tag utilization, and has certain application value.
[ad_2]