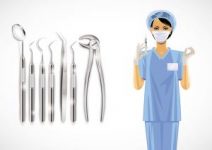
RFID technology helps the intelligent management of disinfection of surgical instruments in hospitals
[ad_1]
The operating room of the hospital is one of the busiest and most important departments. Every operation affects the hearts of many medical staff and patients. As the main tool of the operation, surgical instruments are conceivably very important. Any errors in the operation may cause immeasurable losses. The intelligent management of surgical instruments will bring great convenience. The use of RFID radio frequency identification technology for multi-tags and rapid identification and collection capabilities realizes the intelligent management of surgical instruments.
Most medical institutions have set up equipment disinfection service centers or supply departments to perform medical equipment disinfection, surgical equipment packaging, preparation of equipment needed for surgery, management and lease of medical equipment, and acquisition or purchase of equipment and implants. But the main task of these service departments is infection prevention and control. The Supply Department guarantees that all medical supplies are thoroughly sterilized and disinfected before the operation in accordance with strict standard procedures.
At the same time, ensuring the correct disinfection of trays and washing baskets is also an important task for these departments. Improper disinfection of trays and cleaning baskets is usually considered a serious medical accident, and the hospital will bear a great legal risk. The correct disinfection of the tray can reduce the patient’s risk of infection and reduce the risk of responsibility for the hospital’s surgical team.
RFID can very well help hospitals in process management. By installing electronic tags on each device, it provides a real-time, accurate and automated electronic information recording method. RFID does not require the hospital to introduce a new process system. It can seamlessly connect to the hospital’s existing system process and provide relevant document information for each link in the process. The entire system can also be automatically updated when the equipment is repaired or maintained.
RFID technology realizes the main functions:
1. Before the operation, the disinfection supply department and the cleaning of surgical instruments need to go through multiple procedures. The omission of the procedure may cause potential safety hazards, and the addition of RFID automatic identification technology supervision measures can effectively solve this problem;
2. The management and verification of the packaging and distribution of surgical instruments, and the packaging and sorting of surgical instruments can use RFID readers to detect possible omissions in the packaging process;
3. Equipment management in the operating room. The management during the operation mainly includes preoperative check, postoperative inventory, and doctor confirmation. Each link needs to be accurately identified to prevent the leakage of surgical equipment from causing serious consequences in the patient’s body;
4. Comprehensive information management, statistical query, report system.
It is also very troublesome to manage leased equipment. The hospital will rent some medical equipment and equipment that are not intended to be purchased temporarily. The hospital supply department also needs to clean and disinfect these equipment and identify them to ensure that they are well maintained and stored. Therefore, the use of RFID for these devices can also increase the utilization rate and improve management efficiency.
Preventing surgical infections is of great concern to all medical institutions. The hospital supply department can indeed reduce and avoid infections through the automated disinfection management process. All surgical instruments are strictly controlled to be disinfected and dried to ensure the proper storage and use of surgical instruments. . RFID can realize the automatic and intelligent management of the entire disinfection process. After the hospital adopts RFID to fully manage the surgical instruments, it only needs to use the RFID electronic tag reader to read all the instruments in the range within a few seconds. These data can be used to analyze the blind spots and defects in the management process and form a strong basis for quality improvement and certification.
[ad_2]