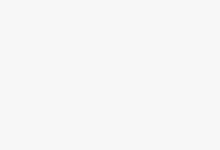
RFID asset management case
[ad_1]
After recent years of market cultivation and technical reserves, RFID technology has come out of the warehouse. In addition to real-time monitoring of the warehouse status, RFID is playing an important role in asset management and production control.
Suppliers that sell consumer products to Best Buy, Target, and Wal-Mart know that using RFID tags is an inevitable choice. These tags can help suppliers and retailers track the time it takes for goods to reach the retailer’s warehouse from the manufacturer’s warehouse through the transportation center. But the benefits of RFID are far from being as simple as inventory tracking. Enterprises can realize complex real-time asset control processes by integrating RFID tags with asset management systems. Erik Michielsen, an RFID analyst at ABI Research, said: “Asset management is one of the fastest growing areas of RFID technology.”
The use of RFID for asset management began with traditional inventory management. Later, the development of IT technology has shown that RFID can bring benefits to many aspects of the company, not just warehouse management.
Major automakers, including BMW, Toyota, and auto shippers, such as NYK, are pioneers in applying RFID to asset management. They install Active RFID tags produced by WhereNet-Transponder in their cars or in containers parked at the delivery site. By monitoring these tags in the asset management system, these companies can ensure that when a vehicle leaves the parking lot at an unscheduled time, the guard at the door can be alerted, or that a container is placed on the truck used to carry it. . Inter-frequency radar transceivers, such as products from WhereNet, usually have the size of several playing cards. They are generally used on large objects, and their prices are between 40 and 80 US dollars.
In contrast, passive RFID tags are very cheap (usually less than a dime) and small in size (only the size of a postage stamp, and not much thicker), so they can be attached to small objects, such as laptops, chemical On containers, ID cards and aviation parts, many objects can be tracked instead of only large ones.
For example, Virgin Atlantic Airways plans to use RFID tags on its aircraft parts to track the location of these parts in repair shops and save their repair data, so that its staff can determine which parts need to be repaired while the parts are still on the plane. Robert Bosch Tool recently installed RFID tags on 65 tools used by large construction companies to speed up the operation of the equipment at the operating point. Tools equipped with RFID tags are 1% to 5% more expensive than ordinary tools, and the main tool management systems used to read RFID tags come from ToolMaster Technologies and ToolWatch.
“If the price of each tool reaches $10, the construction company will choose a competitor’s product.” John Doherty, product manager of Bosch, said he hopes that hardware manufacturers can provide construction companies with RFID with the ability to write information in the future. Reader, so that it can track the maintenance and use process of the tool, and then use the tag to manage the maintenance and update cycle of the tool.

NASA: manages its chemicals
The Dryden Flight Research Center is located at NASA’s Edwards Air Force Base in northern Los Angeles. NASA and its suppliers use a large number of chemicals for the development and maintenance of aircraft, many of which are corrosive and when mixed with other chemicals. It is very likely to explode at times, and they can also cause harm to human health and the environment. However, they have to be stacked in many places, including NASA, the Air Force, the supplier’s aircraft repair garage, different sections of the runway, and the desert.
Dryden Flight Research Center Environmental and Safety Officer Tom Ambrose said that in the past, NASA used barcodes on chemical containers and used checkpoint staff to detect each chemical product and record the total number of chemical distributions and what it was distributed. Department. But due to reduced operator budgets, NASA needs a more efficient method to complete this work. Therefore, it began to apply RFID tags to various containers, and also installed readers in different storage rooms to weigh the containers to track its use and ensure that the corresponding chemical is placed in each storage room. substance. This process avoids the creation of dangerous compounds by comparing the actual weight of the chemical with the expected weight. At the entrance of the work site, NASA placed an Intermec RFID portable reader to monitor the in and out of chemical containers, and identify the operator through the RFID tag on the employee badge.
According to Ambrose, the Dryden system is connected to an Oracle database and an asset control application called the Hazardous Material Management System. The system can inspect the goods at all locations in just a few seconds and use this information to determine Which chemical containers should be placed where and with which ones, and verify this status with the process rules. This ensures that the chemicals will not end up in the wrong place, used by incompetent or unauthorized technicians, or simply moved out of the equipment. Frequent inspections can avoid occasional false alarms due to reading. At the same time, the system can also ignore certain situations, such as when a container suddenly disappears for a few seconds, unless it does not appear after a few cycles, it will issue a security officer. Early warning.
With the help of automated systems, NASA can reduce the number of employees. Currently, Ambrose is studying whether Dryden can use an automated system to allow some chemicals to pass through self-service automated kiosks, which can reduce the time it takes for technicians to recover shared chemicals from the warehouse.
Ambrose said that by combining the above-mentioned data with the weight information of the containers in the storage room, the system can detect how much each material has been used, and then can accurately determine the amount of that material to be replenished. When the expenditure for disposing of unnecessary and expired chemicals exceeds the cost of the item itself, NASA will try to reduce the total amount of chemical materials it orders and stores.
Ambrose expects to use second-generation RFID tags in the next phase. With its authentication function, NASA can determine who is authorized to read the specific information on the tags. But he is worried that when chemicals are transported into NASA or on highways after they are transported out of NASA, terrorists may read the previous-generation tags to determine what chemicals the truck contains. Through authorization, the NASA system will have full access to information, while public safety officials like the police will only have access to basic information, such as how to isolate chemical materials from other items in an accident. No access will be granted.
![]() |
To prevent dangerous chemicals from mixing together during storage or handling, NASA tags them with RFID tags. |
HP: Improve the production efficiency of the assembly line
When the product is moved off the assembly line, the manufacturer usually creates a large amount of data for it to ensure that the product is defect-free, the system is functioning normally, and the parts are safely placed in the correct location. Hewlett-Packard Global Operations Manager Greg Edds said that the complex network built for this purpose will be difficult to maintain. If the network is overloaded or down, the entire assembly line will be paralyzed. As a result, Hewlett-Packard has adopted new second-generation RFID tags and readers in its printer factory in Brazil. Compared with the previous generation tags, the second generation tags can be read by multi-brand readers while storing more information.
However, HP did not connect every link to the network, but connected a device that can read RFID tags to each machine on the production line to obtain its production records and status, and when it moved to the next Write the updated status to the tag during the link.
Edds said: “Only when the last link of the production line is connected to this network, these uploaded complete product production records can be used for tracking and analysis of the production process, thereby reducing server infrastructure. In order to reduce network losses, the results can be Store on-site until the network is backed up to avoid interrupting the production process.”
Edds predicts that the use of RFID tags can reduce the cost of production line management and increase the efficiency of the assembly line, but he did not disclose how much money can be saved. HP has also begun to use RFID readers in other links of its production equipment to meet the requirements of some retailers that all product boxes must be equipped with RFID tags. For example, at its scanner and printer assembly plant in Memphis, Tennessee, HP also marks product boxes and foam trays to monitor their locations in production equipment and warehouses.
![]() |
U.S. Social Security Administration uses RFID readers to accelerate data collection |
U.S. Social Security Administration: reorganizing asset management
The US Social Security Administration often registers its office equipment to ensure that resources purchased with taxpayers’ money can be used wisely. Gary Orem, the head of its logistics department, said that in the past, the agency’s auditors scanned the bar code marks on each device, which was a long process because the bar code must be placed on the device first. But now, due to the use of RFID tags in the warehouse, management has become simple and easy.
The department’s IT team quickly realized that RFID technology could do more than track the distribution and use of brochures and stationery. It helps to actively control access to the device. Now, they are experimenting with a system that tracks equipment when it is removed from somewhere. The experiment started at the IT department office in Washington, DC. It also includes creditor equipment. The access rights to this area are quite public, because office doors are often unlocked, and it is easy for people to go in and borrow some equipment without going through formal procedures. The department’s programmer Matthew Anderson said that they installed an RFID reader on the door to monitor the entry and exit of the device, and then observe whether it is appropriate to place the reader in such a location. Next, they will install a motion detector to determine whether the device is brought in or out of the office. In this way, the data in the RFID reader can be linked with the SQL database of the Social Security Administration and the Oracle Asset Management System to achieve real-time tracking of creditor equipment and IT equipment.
Orem said that its ultimate goal is to track all the equipment in the entire office building and discover the exact time when the equipment leaves the office building in time. This requires installing a reader at the exit of the office building and connecting it with the asset management system of the entire organization to confirm whether the device is allowed to move. If permission is not obtained, an alert is issued to the security officer and the exit is automatically closed. . At the same time, RFID tags are installed on employees’ badges to track who is on the mobile device and confirm whether the employee is authorized to do so. This means reaching an agreement with the security department of the administration, because it is necessary to install RFID tags on the badges of employees and connect the whole system to the systems in the logistics department. In September 2005, the security department had indicated that it would consider doing so.
![]() |
U.S. Social Security Administration applies RFID to fuel tanks |
The US Social Security Administration also uses RFID tags to manage access to its fuel centers. Until recently, employees of the bureau had been using fuel cards, that is, inserting the card into the fuel pump to get the fuel allocated to his public vehicle. But the old system cannot ensure that the vehicle being refueled must belong to the authority. Orem recalled that in the past, the bureau used manual methods, that is, employees filled out forms to obtain mileage and other vehicle status information, and employees often made some mistakes when filling out the forms. Now they have installed RFID tags on the nozzles of the oil pumps, and they have also installed readers on vehicles belonging to the administration. The sensor of the RFID reader is placed at the neck of the gas tank/fuel tank, and is connected to the reader placed on the car body through a cable.
Anderson said that when the nozzle of the fuel pump is inserted into the fuel tank of the car, the reader will first confirm the condition of the fuel pump and then send a wireless signal to it to start the fuel delivery. The reader is also connected to the computer on the vehicle that is responsible for counting mileage and operating status. These data will be uploaded to the system at the same time, so that the bureau can obtain accurate mileage records and automatically know the information that the vehicle needs to be repaired or maintained. Orem said that the cost of using the above-mentioned system is $200 per vehicle, and there are 65 vehicles in total. In fact, this is only a small expenditure compared with the cost saved by using RFID tags. (Translated from “Infoworld”)
[ad_2]