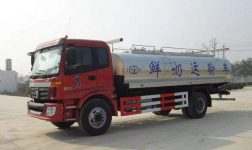
Siemens RFID technology makes the milk transportation process more transparent and easier to control
[ad_1]
Application background:
After a severe thunderstorm, the defects in the existing milk transportation system and truck delivery system were exposed, so the founder of Hansa Milch AG decided to invest in a new recording system based on industrial wireless local area network (WLAN) and radio frequency identification (RFID) . Integrating truck information flow from arrival to dispatch ensures maximum process transparency and minimizes possible problems.
Speaking of it, this seems to be some kind of providence. In 2011, for the milk transportation system and sales network, the German company Arla Foods began to look for a solution that could replace the old-fashioned truck recording system. The start of the project also originated from a summer storm.
The milk factory, which produces 600 million kilograms of milk per year, was struck by lightning, leading to errors in key components and exposing weaknesses in data exchange among gatekeepers, weighing stations, transportation lines, process control systems, and cleaning facilities. The data exchange system at the time was based on Magnetic card.
solution
A team of experts from Hansa Milch of Upahl drafted the development, implementation requirements and target statement of the new integrated truck recording system. The new system requires as few structural adjustments as possible and retains as many existing components as possible.
The core of the new scanning process is the RFID card system, which is based on the infrastructure of an industrial wireless local area network.
Siemens worked with the technical management of the dairy plant and experts from the German vehicle metering manufacturer Pfister Waagen Bilanciai to implement the system.
Coordinated by the central control system Simatic S7 controller, the new system supports the complete data exchange between the truck driver and the process control system. The truck is monitored and managed from beginning to end.
Once the truck driver logs into the system with his RFID card at the entrance, the system records transportation-related data. For example: the quality of raw milk, the type and quantity of products, etc., and the batch information will immediately (different from before) appear in the SattLine process control system of the milk factory.
Andreas Fischer, maintenance director of Arla Foods in Upahl, Germany, said, “In the past, we had to enter data not only at the entrance, but also in the process control system. Now we have a standardized data storage system. This not only saves time, but also It reduces possible errors and gives plant operators an opportunity to adjust the quantity of milk of a certain quality as early as possible.”
Fewer errors
After the truck is weighed on the calibrated vehicle scale, the process control system directs the driver to a certain route according to the type of delivery. Once the results of the rapid inhibitor test come out and the driver enters the correct transportation line via RFID, the process control system allows the truck to be unloaded.
In order to ensure that everything in the compartment is emptied, the process control system compares the weighing results with the induced flow measurement (IDM) data obtained from the production area. If the two values can match, the truck can continue to enter the cleaning-in-place (CIP) program.
In this way, the new RFID card system ensures the consistency of data throughout the process (the truck comes and goes), and provides valuable support in batch traceability and process transparency.
Fischer concluded, “Through this solution, we can guarantee that organic products and conventional products will not be mixed together. It also helps us meet the requirements of the US biological standard NOP (National Organic Program) and is certified in the IFS (International Food Standard). Services were provided in the process.”
Effective communication
Through the introduction of new solutions, the communication between truck drivers and the factory has become more systematic and efficient, and the sources of errors, such as manually entered data or verbal descriptions, have been greatly reduced. The factory not only benefits greatly from the production process and product safety, but also can provide a reliable source of products at any time, thanks to the integrated electronic signature authentication function.
[ad_2]