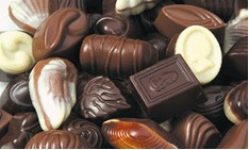
Application of RFID in the food industry
[ad_1]
Application background
Santa Claus made of chocolate, Easter bunny filled with nougat, or chocolate candy in the shape of a policeman-many of these delicious sweets are produced in Lungesdorf, Rhineland-Palatinate, Germany. In this small town near Neuwied, Winkler und Dünnebier Sü?warenmaschinen GmbH (WDS) provides processing machinery for the confectionery industry. At the same time, the company is also committed to developing new pouring/precipitation processes and optimizing existing technologies.
Over the years, the ever-increasing international demand of the confectionery processing industry has ensured the reputation of WDS machinery in the global industry. The company has a wide range of product production lines, which include: hard candy and toffee pouring production lines, filled and solid chocolate shell pouring systems, large starch pouring workshops, flat chocolate equipment, and general-purpose piston extruders for syrup pouring. In addition, the company also provides laboratory-use jellybean depositing machines for product development in the confectionery processing industry to meet broader market needs.

Chocolate production process
The production process of filled chocolate is somewhat complicated. The first step is the so-called mold injection molding, where the molds are loosely placed in the supply chain, and their “production workshop journey” begins. Moulds will move intermittently or continuously according to the operation of the supply chain, starting their journey.
Once the mold is sufficiently heated by hot air or infrared rays, the first pouring machine will inject a precise amount of chocolate syrup into the mold to produce the shell of the candy. Then, the mold is shaken to evenly distribute the syrup, thereby eliminating air bubbles. Then, the mold is turned upside down to separate the chocolate shell from the mold while cooling. The so-called chocolate crust is left in a cooled container waiting to harden.

The second step of the pouring line provides typical fillings such as butter almonds or soft syrup. The principle is the same: heating, filling, cooling. The smooth bottom of chocolate candies-or the “lid” of the chocolate-is made by melting and removing excess syrup, and finally cooling. At the end of the production line, an air hammer is used to gently tap the back of the mold to peel the candy from the mold. The conveyor belt sends the finished product to the packaging line, while the mold is left in the chocolate production cycle. They are sent to the mold transfer station to remove the residue and become a new empty mold for backup. The entire system is controlled by PLC and servo motors, and PC control terminals or customer service terminals connected to the central server are all over each pouring machine.
All molds are clear at a glance
Considering that the processes and sequences of many manufacturing industries are optimized and managed by non-contact RFID transponders (tags), WDS decided to also introduce this innovative NFC (Near Field Communication) technology into its confectionery production line.

In order to complete this project, thousands of plastic pallets in the production workshop were equipped with RFID code carriers. The read-write heads on the production line, as well as the remote data acquisition system in the warehouse and production area, are permanently installed, so that each mold can be effectively tracked by the central control station during the operation of the system. The database-oriented RFID system can ensure the best tracking of molds and products in the production process. In addition, it can also optimize the process and help production data analysis.
The RFID experts from Mülheim, Germany integrated Turck’s read-write heads into the fieldbus system through the BL ident I/O module, so that the WDS control system can view the latest data at any time to achieve real-time monitoring. The read-write head is installed on the mold transfer station and the pouring/precipitating machinery, and is optionally installed in the weighing and other control links.
All data collected by the control system is transmitted to the local database of the factory server, where the real-time data of all molds throughout the production cycle are stored. The information is generated synchronously by the server and used for the overall management and tracking of the mold. A complete RFID system includes not only the reading points on the production equipment, but also the reading heads in the mold cleaning station and the storage system. In accordance with the wishes of customers, WDS allows third parties to use Turck RFID products to transform their old systems.
High value-added data
Today, Turck’s RFID system can ensure that the central server database of each WDS device contains valuable information, which can be used to optimize factory production and product quality. The data pool may have a wide range of applications, including optimizing logistics. With a light click of the mouse, the system can display the real-time position of any mold or its running track on the entire assembly line. In this way, potential sources of errors can be easily pinpointed.

Production-specific data can also be determined from this. For example, the system can detect that the residue content of a single mold or even the entire mold group exceeds the standard, and then automatically pick it out. Another application is the ability to compare the production characteristics of a mold set and a specific batch.
The data pool is also very useful in quality control and sanitation supervision within the factory, especially in quality management. The system can easily identify whether the current production process is clean. At present, the system can closely track the production process, such as pushing the mold collectively into the freezer, or replacing the mold with a special test mold during the operation of the system, all of which benefit from RFID technology. If the implanted mold is not suitable for the currently running production process, the system will immediately issue an alarm. “Rapid” product replacement is also feasible under this technical condition: when the old mold is picked out, the new mold is implanted into the system. Even if the mold group is randomly mixed production plan is also possible, which increases the flexibility of production.
Win-win
“In a batch of competitive products of the same kind, we finally selected Turck. The BL ident system provides hardware with standardized interfaces suitable for industrial sites.” explains Bernd Plies, head of electrical engineering and automation technology at WDS “We have successfully combined Turck’s RFID system and bus systems, such as Profibus, DeviceNet and Modbus IP, among the various bus protocols currently being used in our production workshop, and it is also suitable for future bus systems.” Another important factor is the broad application prospects of the read-write head in the industrial field.
As expected, the system integration in the factory was ready to go online, and no problems were found. “The system is running very smoothly and smoothly.” Plies recalled, “All components were quickly integrated into the first WDS application, enabling Step7 debugging. One or two problems will also emerge, but communication via phone is very fast. It’s all solved.”
According to Plies, another advantage of this project is the close cooperation between the two companies: “Cooperating with Turck is always constructive.” Turck’s technicians are good at innovation and try to match customer expectations. Put it into practice or develop alternatives. “We have benefited a lot from maintaining close contact with Turck’s R&D staff.” Plies added.
[ad_2]