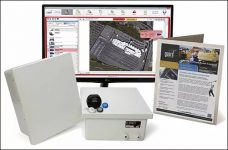
Linder Industrial Machinery deploys RFID system to prevent human error in the equipment leasing process
[ad_1]
The Florida-based Linder Industrial Machinery Company is using the RFID-based active system provided by GuardRFID to track the movement of high-value equipment to improve production efficiency. The company also uses these RFID data to better manage equipment cleaning or maintenance services. At present, the system has been put into use in the company’s 9 storage areas, reducing the time-consuming inventory tracking and ensuring that high-value assets are not lost.
The AllGuard Yard Management solution was put into use in August 2017. Since then, Linder can better manage the equipment that leaves or returns to the warehouse and the workshop. The system can also track the users of the equipment and the length of rental time.
AllGuard Yard Management Solution
Eric D. Strid, IT director of Linder Industrial Machinery Company, said that the company was founded in 1953 and mainly leases and sells equipment for residential and commercial applications and highway construction. The company’s customers are located in Florida, North Carolina, South Carolina and Georgia. Its subsidiaries store and maintain equipment such as milling machines, pavers, crushers, and disassembly systems.
Inventory management is a challenging task, and the company used to manage it manually. Some equipment is worth hundreds of thousands of dollars and frequently and in large numbers enter and exit the storage location, so the equipment is very easy to lose. Strid said that when business is busy, there are usually six or seven trucks waiting to pick up the goods. Therefore, item loss is inevitable. In fact, the company has to write off equipment worth $70,000 each year on average.
Sometimes, after the equipment is returned, it is not formally entered into the system, which means that there will be no available machines in the system during the next rental. A more serious situation is that a piece of equipment leaves the storage site and the company does not know where it is.
The GuardRFID system uses active RFID tags, with a tag attached to each item. To date, the equipment company has purchased 1,800 tags. Around 6 GuardRFID 433 MHz Solar Tag Readers (SPTRs) are installed around each storage area. Four solar powered tag actuators (SPTE) are also installed at the exit gate to activate tags through 125KHz transmission. Then, the tag will send its own ID number and the ID number of the exciter to a nearby card reader. The SPTE’s response will then indicate the direction of departure of the device (both entrance and exit doors are equipped with an exciter).
SPTR transfers data to GuardRFID’s cloud-based software via a Wi-Fi connection. Then. GuardRFID software reads inventory data from Linder ERP system and modifies it based on RFID data. If there is an abnormality, the system can also issue a warning.
The working steps of the system are as follows: First, the staff receives a lease transfer order or sales order. Then, employees use GuardRFID software to confirm whether the requested item is on the spot, and the RFID reader data will show the location of the tag on the map. When the equipment is shipped out, the status of the item will be updated. When the device returns, the system works similarly. When returning, the actuator at the door wakes up the tags again, and then the software updates the status of each tag ID to received.
This process can also run when equipment is transferred from one RFID warehouse in Linder to another warehouse. In this way, the company can know the specific warehouse location where the equipment is placed.
Although the main function of the system is to identify the arrival and departure of equipment, it can also manage tagged items on-site to provide real-time data and analysis. Strid said: “Now, we can understand the trend of each device.”
The system reduces the time spent by staff looking for equipment in the warehouse and also provides historical data. These data can be used to analyze equipment maintenance and lease preparation time.
Strid said that since the system was put into use, it has prevented at least one costly error. He explained that when a customer was taking the wrong equipment out of the warehouse, the software found the error and issued an alarm. In the future, the company intends to cooperate with some equipment manufacturers to establish a system so that they can put RFID tags on themselves before selling the equipment to Linder Industrial Machinery.
[ad_2]