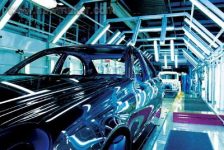
Application of Barcode Technology in Automobile Manufacturing
[ad_1]
1. Social background
The development of social economy and the intensification of market competition have presented a series of challenges to industrial production. The goals of efficiency, quality, and cost pursued by industrial production in the age of industrialization have been given new content. The number of products produced per unit of time has no longer become the main symbol of corporate competitiveness. The time from product development to product launch is The key for enterprises to win the market and customers, information has become the decisive factor for the survival and development of enterprises, and the production technology and organization management of enterprises are undergoing profound changes.
Product production (inventory, delivery, sales, after-sales information) is related to a single product, so the amount of information is large, the information is widely distributed, and the source of information is complicated. If these materials are collected manually, it will greatly increase the number of information collection personnel and information input personnel, and reduce the accuracy of information. In order to achieve product tracking, manufacturers are constantly looking for new solutions.
As barcode technology matures and is widely used, barcodes can be printed quickly and with high quality (such as using DATAMAX special barcode printers); barcodes can be quickly and accurately identified by various scanners (such as using Welch Allyn barcode readers). Manufacturers use bar codes to identify their products, collect product information during production, inventory, delivery, sales, and after-sales, use computer networks to collect product tracking data from different distributions, and establish data collection and tracking management information systems.
With the continuous development of my country’s automobile industry, some related systems have been introduced one after another. This year, my country will formally implement the “Automobile Recall System”. Therefore, some automobile and spare parts suppliers must pay attention to the traceability of parts and components. In this traceability process, Barcode technology has played a key role-by sticking barcode labels on parts to realize the tracking and tracing of these retail parts.
2. User needs
At present, most automobile manufacturing companies have implemented ERP systems, in order to further build a unified enterprise management information system with ERP as the core, and comprehensively improve the company’s production management level and efficiency. Therefore, these companies will seek a set of management methods combined with ERP systems to facilitate the improvement of workshop production management.
-Provide ERP system interface, and can easily share relevant data in ERP system
-The system interface display is intuitive and clear, easy to operate, reflects comprehensive content, and can simulate operation through the interface to adjust the daily production plan
-With strong data statistics, analysis, tabulation, and query functions
-Accurate and fast information transmission
-Make full use of the bar code information source to realize the traceability of parts
Three, system design
Manufacturing Execution System (MES) is a management information system oriented to the shop floor between the plan management system at the upper level and the industrial control system at the bottom level. It provides operators/managers with the execution and tracking of plans and the current status of resources (people, equipment, materials, customer needs, etc.). Its architecture is shown in the figure:

The main relationship of the functional structure:
1. The relationship between MES and ERP/MRP-II is two-way data exchange. MES receives ERP/MRP-II production instructions and product data and configuration, and MES returns process reports and completion reports to ERP/MRP-II.
2. MES receives the work-in-process production process parameters generated by the industrial equipment control system as part of the work-in-process production file.
3. Workshop configuration and product data management provide the basis for the formulation of job plans and dispatch of job scheduling in job management.
4. Job management provides scheduling lists and sources of work-in-progress for production process management, and at the same time reflects production instructions or job scheduling production process information through production process management.
5. Collecting data provides a data source for the production process of the work-in-progress for the production process management, and at the same time provides bad work-in-progress for maintenance management operations. Maintenance management is also provided to production process management as production process data.
6. Perform process statistics on production process management, provide quality management for quality statistics and quality control; archive production process management, and provide product file query and product list query for product data management.
Four, function
Function diagram:

1. Receive ERP data
Receive BPCS production instructions:
MES receives monthly production instructions from ERP through database sharing, adds system production instructions, and revises production instructions without production.
The received data includes the production order and its corresponding product production configuration. There is no production order number in the ERP system, and it needs to be automatically generated by the MES system.
The production instruction data is: ERP project number, model type, quantity, planned production date;
Product production configuration data are: project notes (including BPCS project numbers or part numbers and notes for engines, frames, axles, body, etc.), and the amount of units.
Receive BPCS material inventory:
MES receives monthly inventory data of BPCS materials through database sharing (received once at the beginning of each month). This data is used to count the monthly balance reports of materials.
Receive BPCS parts catalog:
MES receives BPCS parts catalog data through database sharing, including part number, part name, part price and other information. This data is used for statistical material monthly inventory reports.
2. Material preparation
The preparation of materials includes the preparation of the body (which can be expanded). The body is directly entered by the body factory, so the body is received in the assembly plant and stored in two warehouses to establish a body material preparation inventory (part number, quantity).
Material preparation: Collect the part number of the car body and designate the storage warehouse to accumulate the material inventory.
Material allocation: According to the material preparation inventory, it is allocated to the detailed operation plan.
Reduce material inventory: The production instruction starts job scheduling, and the required material preparation inventory is deducted.
3. Detailed operation plan
The detailed operation plan includes a complete vehicle supporting operation plan and a separate operation plan for the chassis and interior trim.
Complete vehicle supporting operation plan:
Prepare inventory according to materials, arrange production quantities of production instructions, and establish detailed daily operation plans in batches.
The cumulative production order has been planned. When assigning materials, specify the contractor and its specific distribution quantity to reduce the material preparation inventory of the corresponding contractor.
Assign the VIN of the job plan product.
Chassis individual operation plan:
Arrange the production quantity of production instructions, and establish detailed daily operation plans in batches.
The cumulative production order has been planned.
Assign the VIN of the job plan product.
Individual interior work plan:
Arrange the production quantity of production instructions, and establish detailed daily operation plans in batches.
The cumulative production order has been planned.
4. Job planning and scheduling
Arrange the production sequence of the detailed operation plan.
According to the processing center (interior, engine, chassis, final assembly), the job plan is broken down, the production job plan sequence table is printed, and the job scheduling points are notified.
The production schedule sorting table is as follows:
The production schedule of the assembly plant of the automobile company
The interior is online (chassis online, engine online, final assembly online) Date: April 3, 2001
order |
ERP project number |
Model variety |
Modification number |
quantity |
Part Number |
Job plan batch |
Remark |
1 |
123B62A1000003 |
NJ1037AEB |
|
10 |
|
200104001 |
|
2 |
|
|
|
|
|
|
|
3 |
|
|
|
|
|
|
|
instruction:
-This table is used for the on-line production scheduling of interior trim, engine, chassis, and final assembly
-In the table, the ERP item number, model type, part number and modification number are ERP data
-When scheduling the production operation, the ERP project number must establish a corresponding relationship with the operation plan batch
-The quantity data is the quantity of the detailed operation plan and the quantity of allocated materials
-Remarks refer to the air conditioner type code
5. Job scheduling
Machining center job scheduling report. Carry out job scheduling in accordance with the scheduling plan and report the job scheduling process. The Planning Department clearly understands the detailed production status of the operation plan and controls the production of the operation plan according to the operation scheduling report of each processing center.
The interior trim and engine separately report the completed number of job scheduling. When the interior and engine go online, the operator arranges the online order according to the production schedule of the production department, confirms the type of online one by one, records the online time, and reduces the number of plans for the corresponding items in the operation plan batch.
Chassis and final assembly job scheduling report the work-in-process VIN that the job scheduling started production. When the chassis and final assembly go online, the operator arranges the online order according to the production schedule of the production department, scans the VIN number, records the online time, and the system automatically reduces the planned number of corresponding items in the operation plan batch.
6. Large screen control
Monitor the production status of the final assembly processing center in real time, and output the planned and completed quantities of the final assembly processing center on a large screen on the day; monthly planned quantities, monthly completed quantities, annual planned quantities, and annual completed quantities.
7. Production process management
Work-in-process management in the production process and statistics on the distribution of work-in-process processes.
Query the completion of the tasks of each line and prepare for the next task. Through real-time data collection and network communication, we can understand the completion of the operation plan batch in time and prepare for the next task.
Query the execution status of production instructions. Through the formulation of detailed operation plans, the cumulative production order plan number is provided, and the production order execution status query function is provided.
Query the assembly model of each parking space of the interior, chassis, engine, and final assembly lines. Through the job scheduling report of each online point, the assembly model information of each parking space is displayed in the order of parking spaces. Until the number of online parking reaches the total number of parking spaces on the entire line, the next online task will be counted again. This information is dynamic, ensuring that the production department can check the assembly model information of each parking space on each line at any time.
Query daily, weekly, and monthly inventory status records. The number of completed models is counted by time period (day, week, month).
8. Product data management
Product file query and product file maintenance functions. Query the product assembly component identification (SN number) according to the product VIN number; query the product VIN number according to the component identification (SN number).
9. Data collection
Data collection is carried out on the production line, off-line and component assembly points to provide convenience for product tracking.
The data collection flow chart is as follows:

Collection process description:
(1) On-line collection of chassis
Work in progress is online. The barcode printer prints the vehicle VIN number according to the chassis schedule, scans the vehicle VIN number, the system automatically generates the online serial number, and drives the cutting plotter to engrave the corresponding VIN number on the chassis. It needs to be integrated with the cutting plotter software.
(2) Collection of key pieces
Work-in-process assembly. Collect vehicle VIN number and component identification number (SN number) (body, front and rear axle, engine, gearbox, etc.), and establish the corresponding relationship between vehicle VIN number and component identification number.
(3) The interior is online
Collect the body assembly number, and the system automatically generates the online serial number to track the batch of safety parts on the body.
(4) Final assembly goes online
Collect the vehicle’s VIN number, retrieve relevant information from the system (product catalog number, engine model, etc.), and drive the carving machine to engrave the nameplate and label, and process the finished product offline according to the total number of assembly stations, send a message, and confirm the big screen show. It needs to be integrated with the cutting plotter software.
(5) Final assembly off-line diversion
Collect the vehicle VIN number to distinguish between vehicle test diversion and vehicle modification.
(6) Test collection
Collect the vehicle VIN number and retrieve relevant information from the system so that the vehicle test system (supplied by Tsinghua Unigroup) can perform comparison tests.
(7) Print the certificate
Collect or input the vehicle VIN number, retrieve relevant information from the system, and drive the printer to print the relevant information on the certificate.
(8) Inspection and adjustment completed
Collect the vehicle VIN number and confirm the completion of the product.
(9) Collecting in and out of the factory
Entering the factory: The whole vehicle enters the parking lot of the assembly plant. Collect the vehicle’s VIN number and establish the vehicle’s entry file.
Factory: The whole vehicle leaves the factory and is ready to enter the Wanshou warehouse. Collect the vehicle VIN number and the driver’s barcode label, and establish the vehicle factory file.
(10) Inbound collection
Collect vehicle VIN number, establish vehicle warehousing record, and print warehousing list.
Five, implementation effect
1. Through the collection of bar code data, the work efficiency of workers is improved, and at the same time, some man-made recording errors are reduced.
2. It is convenient for the planning personnel of the assembly plant to schedule production and improve work efficiency.
3. The production management personnel can grasp and deal with the situation of the workshop site in time.
[ad_2]