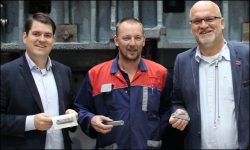
RFID helps auto parts manufacturers identify the location of stamping tools
[ad_1]
Polynorm BV, a manufacturer of auto parts and systems, is deploying RFID readers on bridge cranes to track 8,000 stamping tools in Bunschoten’s warehouses and assembly plants. The system ensures that the company can track the location of tools when required for product manufacturing, thereby preventing production delays caused by tool search.
Voestalpine Polynorm produces auto parts for new custom body orders and replacement of existing auto parts. For example, the company uses large sheets of metal to produce car covers. The production process of the car cover exceeds 6 processes, including drawing, cutting and stamping. The production of the inner and outer parts of the car cover requires more than 5 processes, and a large number of tools are required for cutting. The factory requires a total of 20 different tools for production, each weighing 30 tons.
(Volker Ruitinga, Peter Altena and Bert Koelewijn of the Voestalpine Polynorm RFID team are using passive UHF RFID tags in the handheld factory)
During the production process, the company needs to bring out more than 8,000 stamping tools in the warehouse. There are 6 production lines in the factory, and the stamping tools can be used on any production line. Each customer may order 100 customized parts every day and 100 spare parts every month.
The storage of large stampings has always been a big problem. In addition to storing these tools, transferring them from different production lines also requires some logistics planning. In the past, companies have managed these tools by recording locations on handwritten paper cards. This is a very time-consuming task. Warehouse employees need to determine the location of the tools based on the paper cards to ensure that they get the correct tools.
(Voestalpine Polynorm uses a tower crane to move heavy press tools)
A year ago, several employees of the company developed this solution with the help of a Dutch service provider. The team began attaching passive EPC Gen2 UHF RFID tags to each tool. The company also attaches tags to warehouse aisles and production lines to confirm location. In the software running on the company’s server, the tag ID number is bound to the tool information and its location. The team installed three UHF RFID readers and antennas on a crane to read tags on the sides and front of the crane. They can read tags within 15 meters, so they can cover the theoretical maximum range between the crane and the tag.
When the crane moves, the reader starts to read all the tags in the range, and then transmits these data to the server. The software on the server will analyze these data and determine the location of cranes and tools. After the software recognizes the tool position change, it updates the position information. The operator can then use the software to understand the location of the required tool.
(The crane uses a customized RFID reader antenna that can read tools and location tags within 15 meters)
The system can also know where the crane is storing tools. In addition, the system can prevent mistakes in bringing wrong tools to the scene.
For companies, there are many difficulties in using RFID systems in metal environments. Each tool reflects these signals. During more than a year of development and testing, the company tried out a variety of RFID tags and readers, and finally chose custom tags, readers and antennas to provide reliable reading rates.
Since the system was put into use, it has saved a lot of time spent searching for tools. also. The system can also provide tool usage analysis and its time and frequency. The company plans to install readers and antennas on all cranes by this fall.
(Exclusive manuscript of rfid world network, please indicate the source author for reprinting!)
[ad_2]