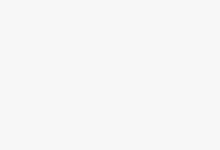
Lufthansa uses RFID to track parts
[ad_1]
Lufthansa Technik (LHT), the maintenance and overhaul department of Lufthansa, installs Mojix RFID hardware at the entrance of the repair shop, and further uses the RFID system to track the accompanying documents of the aircraft parts that need to be repaired.
At the same time, the company’s cargo transportation branch, Lufthansa Cargo, now uses RFID to track hazardous or volatile materials. When they are placed on pallets, they are transported to the aircraft for loading. Lufthansa Technik is also testing the use of RFID to track expired items-such as life jackets on Lufthansa aircraft. To further adopt this technology in the company, LHT and its Lufthansa Technik Logistik (LTL) division independently developed labels. The label accompanies the entire repair process of aircraft parts and is used in conjunction with safety equipment to track the expiration date, thereby saving the labor previously spent on testing aircraft equipment.
In order to track the maintenance of parts, Lufthansa Technik started to stick RFID tags on parts identification documents in November 2007. When items need to be inspected or repaired, they are first sent to a transfer point-LIT’s warehouses across Germany, such as Hamburg, Frankfurt, Berlin and Munich-before MRO related work. After the items are repaired, the parts and the printed documents are returned to the LTL warehouse and then returned to the aircraft. Paper records include component types, owners, and maintenance requirements. Before the RFID system was adopted, when the parts were sent for repair and returned, the staff would read such files with the naked eye, and then manually input the data into the system. The whole process was labor intensive.
In early 2007, an LHL repair center technician or LHF employee affixed an EPC Gen 2 UHF passive RFID tag to the file when the parts and their files were sent to the external repair shop. The label contains a unique ID code, which corresponds to the parts and their maintenance data in the LTL back-end system. Before the parts are repaired and returned to the central MRO factory, a desktop RFID reader reads the tags.
According to Tom Burian, Lufthansa Technik Logistik RFID project manager, in February 2009, LHT began to install a Mojix EPC Gen 2 real-time location system (RTLS)-scheduled to be launched in May-to read the same tags on aircraft parts files when they were Carsten Sowa, LTL RFID project manager, said when it was shipped to and returned from the Hamburg repair facility.
The Mojix STAR system includes 8 eNodes in a star-shaped divergence mode, providing a 20-meter-long passage from the logistics warehouse to the repair shop processing area (where the parts are folded, inspected, and then sent to the repair punch). eNodes transmit a UHF RF signal, activate the passive tag, the tag responds, and sends the ID code to a STAR reader, said Roelof Koopmans, Mojix European management director. In this way, Lufthansa automatically records each component entering or leaving the processing area. When the inspection and maintenance tasks are completed, the workers use hand or carts to transport the parts and their files through the processing area and passage. At this time, the e-Node will activate the file tag again and send its ID code to the STAR reader. The tag reading data and time data will be sent back to the back-end system again to identify the time when the parts repair shop returns to the company’s logistics warehouse.
In another RFID project launched by the company in the fall of 2009, the Lufthansa Cargo department installed a Mojix cargo tracking system to ensure that hazardous materials were not stacked together. There are strict regulations on what items should be stored and how they should be stored. For example, chemicals and fuels are forbidden to be stored together due to their volatility.
By identifying dangerous goods before loading on pallets, the company can prevent goods from loading errors, such as incompatible items being placed on the same pallet. The company installed a total of 12 Mojix RFID eNodes and 48 antennas in the 50,000-square-foot warehouse at Frankfurt Airport.
Lufthansa Cargo affixes passive EPC Gen 2 labels to all items containing volatile substances. The ID code of each tag and the item-related data, destination and user are then stored in the SAP software of Lufthansa Cargo’s back-end system. If two dangerous products are within a certain distance from each other, which means they are on the same pallet, the software sends a soft year.
At the same time, to track the expiration date of other parts on the aircraft (such as life jackets or aid kits), LTL and LHT each developed EPC Gen 2 passive tags to track the expired parts of the aircraft. The size, weight and performance of the tags are all consistent with the attached items. need. The company also plans to apply these tags (size 1.5 * 0.25 inches) to life jackets and medical equipment.
So far, the company has tested the labeling of all equipment on an aircraft. The ID code of each tag corresponds to the part batch number, description and expiration time in Silverstroke Tagpilot software (Lufthansa Technik is used to manage RFID data). Workers use Motorola’s MC9090-G handheld RFID reader to read the unique ID code of the part. If a part is about to expire, the employee receives an alert on the handheld screen. All the information read by the tag is then sent to the back-end software via Wi-Fi connection.
In the future, the company hopes to apply labels directly when parts are produced.
[ad_2]