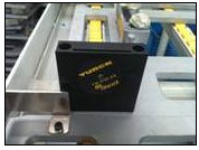
Automobile engine assembly companies adopt RFID technology to improve production efficiency
[ad_1]
The engine is the most technologically intensive key component of the automobile. In the assembly process of the automobile engine, due to the diversity of the assembled parts and the cumbersome process, the engine assembly line is particularly important. The engine assembly line is an assembly line for sequential assembly of engines. The sequence between stations is irreversible, and the control of each link requires both reliability and flexibility. Only in this way can the continuity and stability of production be guaranteed. Therefore, integrating RFID technology into the engine assembly line can achieve high-precision, high-efficiency, high-flexibility and high-quality production.
Since the customer adopts the balanced production method of multiple types of engines and assembles different equipment in the same process, it is required to automatically identify the engine type (hereinafter referred to as the “model”) through RFID technology, so as to automatically call the corresponding correct assembly The program must not be assembled by mistake.
Because the engine assembly line adopts the part supply logistics method that combines the catering and the line-side material rack. There is a dedicated catering area in the workshop to distribute parts. Therefore, the final assembly line needs to transmit the model ID to the catering area via RFID and display it on the parts rack with indicator lights according to the current model of production. The operator selects the correct parts according to the vehicle card and puts them on the catering truck, and finally, a dedicated person puts the catering truck into the production line. The parts that are transported to the side racks of the production line correspond to different models. The customer hopes to identify the current production model through RFID, so as to guide the operator to pick the correct model parts, and whether the operator has already picked it up The action signal is fed back to the assembly line to form an interlock. When the operator does not take it or the feedback signal is wrong, the station shall not be released or the assembly line shall be stopped.
In the automatic measurement and tightening stations of each assembly area, the customer needs to collect the measurement data, and send it to the PC by RFID for sorting and evaluation, and then make corresponding statistical reports and quality analysis.
In addition to the above requirements, in order to ensure that the data and assembly status during the engine assembly process are reliably collected, RFID read-write heads must be configured at each assembly station. When the tray with the code carrier enters the induction magnetic field of the read/write head, the data of the code carrier is automatically written/read by the read/write head. The entire control system associates the code carrier with the corresponding engine through the ANDON system to realize the full tracking of the assembly process.
Digitized tray
The pallet embedded with the code carrier is called the digital pallet, which is widely used in all current applications.RFIDTechnical logistics online. Through the digital pallet, the code carrier and the objects on the pallet can be bound one-to-one on this logistics conveyor line. In this way, the object has a unique identification before it is separated from the pallet, so that a high degree of flexible production can be realized on a complex mixed assembly line, and storing the data in the code carrier of each pallet can also simplify the central database and information system The logical relationship is easy to maintain.
Compared with traditional pallets with barcodes, digital pallets are easier to read, and the code carrier is suitable for harsh environments. Even if there are scratches or stains on the surface, normal reading will not be affected. Since the pallet is used in a closed loop inside the workshop, the code carrier can be reused. In addition, the storage capacity of the 8K byte code carrier is much greater than that of the barcode.
BLident solution
The assembly line adopts the field bus control method, and the operation of the assembly line is uniformly controlled through on-site distributed I/O and the communication between each station is completed. The on-site information monitoring system adopts the Ethernet method to complete the functions of information collection, production scheduling, station monitoring and assembly prompts on the assembly line. According to these requirements, we provide customers with two different communication protocol gateways. One gateway communicates with MITSUBISHI PLC through Profibus DP to achieve fieldbus control; the other gateway directly connects with PC through Modbus/TCP to achieve field information Real-time monitoring, as well as retrieval and traceability of important parts.
Because in this project, the customer needs to store a large amount of data including engine ID, all parts ID, torque of each shaft tightening, rotation angle, etc. in the code carrier, so we provide customers with 8K byte code carrier. In this way, customers can have sufficient storage area to record the required data. In addition, customers worry that due to uncertain factors, the data in the code carrier may be lost or the read-write head cannot read normally. To this end, we provide customers with handheld readers. The operator can flexibly perform read and write operations on the code carrier fixed on the pallet, thereby ensuring a high-efficiency assembly cycle and avoiding the assembly line from stopping for a long time.
Customer Reviews
The system integrator for this project is Tianyong Machinery Electronics (Shanghai) Co., Ltd. When talking about BLident products, the project leader Rong Chuanhua said: “Turck’s modular design of couplers is very convenient. For different communication protocols, only the gateway needs to be replaced. In the same project, modules, The bottom plate, read-write head, code carrier and BLident cable can all be selected the same. And it is very flexible to use, each gateway can connect up to 8 read-write heads, in addition, you can also connect other digital and Analog input and output modules. If you need to add new points on site, you only need to add modules and backplanes. This can save the cost of gateways and reduce on-site wiring. In addition, the read-write distance between 0~200mm is completely To meet the application needs; the working status of the read-write head and the RFID module can be clearly seen through the LED lights; the pre-cast cable reduces the difficulty of installation; the standard PIB function module simplifies the program development.”
Summarize
The benefits that RFID technology brings to enterprises are not just the sum of the code carrier and the read/write head. These two devices alone can only obtain a more effective means of reading and writing than bar codes, and cannot bring long-term competitiveness to the enterprise, and cause fundamental changes and innovations in the enterprise itself.
The introduction of RFID technology is a stage in the continuous improvement process of an enterprise. To achieve this fundamental change and innovation, in addition to effective data collection, the company’s own control system must be upgraded and transformed, the company’s existing resources, processes optimized, and the useful value of information effectively utilized. Only in this way can the value of RFID technology be maximized and bring greater benefits to enterprises.
[ad_2]