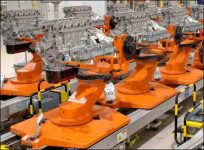
Ford uses Omni-ID’s new RFID tag to monitor engine production
[ad_1]
Ford is the first company to use Omni-ID’s new large-memory passive UHF RFID tags. Ford asked Omni-ID to design a passive tag with a frequency of 860-960MHz to trace engine components in the manufacturing process. Ed Nabrotzky, Chief Solutions Officer at Omni-ID, said that Adept 850 is the result of this collaboration. Adept 850 has 64Kb of internal memory and can encode within 4 meters, with a reading distance of up to 8.5 meters. The size of this EPC Gen 2 RFID tag is 65mm*45mm*8mm. It is sealed in a hard IP68 ceramic casing, which is dust-proof and water-proof.
Ford has used this tag to track engine work in progress, and another automaker also uses it to track transportation. Nabrotzky said that since the release of this label, potential customers in the automotive and energy sectors have expressed great enthusiasm. He said: “The most typical comment is: I have never imagined that metal tags can have such a large memory and read distance.”
This label is designed to help automakers build a more agile manufacturing system. Due to the inconsistency of each vehicle and part, the tracking of parts and vehicles during the production process has also become very critical.
Many automobile manufacturers have used passive high frequency 13.56MHz RFIDTags track items during the production process. This is because high-frequency tags have higher reading reliability in metal environments and have relatively large memory.
The memory size of the automobile manufacturing industry is very important, and the data is generally stored in the tag rather than in the software on the server. This is because parts often move from one factory to another, and at the same time, not every company can access the same server. In addition, Nabrotzky added: “Even if the network crashes, the car factory will continue to operate.”
The high-frequency tag has strong reliability and large memory, but the reading distance is short. Employees need to bring readers to read tags on the production line, or use robots to read tags within the reading range. In either case, the production process will be interrupted.
With more personalized order requests, the production process is no longer linear. The assembly direction of the parts may also be different. Due to the short reading distance of the HF tag, the reading of the tag becomes very difficult.
Adept 850 can read and write within a certain distance, so the reader can be placed in other areas of the factory to read and write tags. Since the tag has a different UHF frequency band, it can also be used on a global scale. To achieve these functions, the tag uses a cross-polarized antenna to achieve multiple frequency bands. There is a line on each side of the label to meet the requirements of their respective frequencies. One side antenna can transmit 916MHz signal to meet the needs of North America. The antenna on the other side can transmit 860MHz signals to meet the needs of Europe and Asia.Users can AndroidReaderRead the signals on both sides of the tag or directionally receive the signals on a specific side.
In addition to having 64Kb of memory, the tag also supports up to 240-bit Electronic Product Code (EPC). However, Nabrotzky refused to disclose the maximum reading distance of the metal tag.
Adept 850 stores a unique ID number, and when the engine is assembled, the staff can write any information. In this way, Ford can know the engine model, manufacturing steps and prevent errors (such as missing a certain step) by reading the label. In the autumn of 2014, this label was officially put into the engine production process to trace back.
Nabrotzky said that this label will be put into other projects soon, and many companies have begun to order samples. Companies in the energy industry are very interested in the tracking and use of labels in pipeline inspections and maintenance. In these application scenarios, because HF tags are difficult to locate and cannot be approached by people, HF tags are not suitable.
Due to the special requirements of the energy industry for hardness, Omni-ID also plans to develop a special version of Adept 850 for the energy industry.
(Exclusive manuscript of rfid world network, please indicate the source author for reprinting!)
[ad_2]