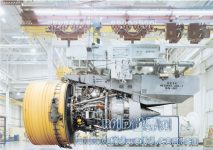
GE Aviation introduces RFID order tracking system to achieve accurate tracking of product delivery
[ad_1]
GE Aviation-GE’s civil and military jet engine manufacturing division-recently introduced an RFID order tracking system into production, according to Trey Keisler, GE Aviation Planning and Logistics Information Management Director.
According to Keisler, the RFID system simplifies the supply chain process of the company’s internal warehouses and container plants (referring to warehouses in Erlanger, Ky and container plants in Durham, NC), while also improving the accuracy of the supply chain. Considering that GE Aviation has received orders for new engines from Boeing and Airbus in recent quarters, the introduction of this system is just in time.
In Erlanger, workers put the small components of the manufactured engine in a plastic suitcase, the size of which varies according to the size of the loaded parts.
Prior to this, GE Aviation had been accurately recording the type and quantity of parts prepared to be shipped from the warehouse every day. However, GE Aviation cannot quickly check the actual number and types of plastic boxes sent to the Durham plant every day.
E Aviation is a professional manufacturer of civil and military jet engines
When the plastic suitcases are loaded on pallets and ready to be shipped away, workers paste a bar code on each plastic box, and then scan the bar code. The barcode contains a number called a license plate by GE. The number is stored in the warehouse management software and used to generate the shipping day list. In an ideal situation, Keisler said, all pallets in a delivery mission would be loaded onto a truck and arrive in Durham the next day.
However, there are often missed shipments in a freight task. Because the list received by Durham reflects the goods that the warehouse is preparing for shipment, rather than the goods actually delivered by the truck, the records often make mistakes. In order to understand the actual shipping situation, Keisler said, Durham employees often had to spend a lot of time carrying clipboards around to check each pallet. After adopting the RFID system, Durham was able to get rid of this manual process and also saved the time of Durham employees receiving parts and bringing them to the production line.
Workers in the Erlanger warehouse now use RFID tags with barcodes printed on plastic boxes. Each tag is embedded with a passive, ultra-high frequency RFID chip, which conforms to EPC Gen 2 and ISO 18000-6C standards, and includes a pre-programmed ID number. When the RFID printing and encoding machine reads this ID number, it will print a bar code on the label. The bar code contains the license plate number generated by the WMS (Warehouse Management System). In WMS, this license plate number corresponds to the ID code of the label. Because the license plate number will be used in other transportation and production processes, GE Aviation also retains this number.
According to the specific size of the plastic box, each pallet is loaded with 2-4 plastic boxes. Before placing each plastic box on the pallet, workers attach a printed RFID label to the plastic box and use a handheld scanner to collect the license plate number from the barcode on the label. When each pallet is loaded onto the truck, the truck passes through an RFID portal reader, which collects the unique number of each RFID tag. Once the truck is full, WMS generates an electronic freight bill based on the RFID read data. Based on the results of the barcode scanning, the system determines which plastic boxes are not loaded on the truck although they are labeled.
In Durham, unloaded pallets are moved through an RFID portal reader. WMS then compares the tag ID number collected by the reader with the number of goods on the electronic shipping list to confirm the accuracy of the shipment.
Because the label is stuck on the plastic box, Keisler claims that enough buffering is created between the chip and the metal parts to eliminate RF interference.
When the plastic boxes were delivered to Durham, they were stored in a special room. When the plastic boxes are brought into the room, they pass through a door reader, which reads the RFID tag ID number of each tag. When the plastic box is finally moved out of the room, the tag number is read again, providing Durham with a real-time inventory of the labeled plastic box in the room. The empty boxes returned to Erlanger must have their old labels removed before being reused.
GE Aviation began testing this system in the second half of 2006 and officially launched the system in December of the same year. Keisler declined to disclose the name of the RFID hardware and software provider.
This is just one of many RFID systems tested or adopted by GE Aviation. The company began labeling idle parts at its aircraft support center in Massachusetts in 2005.
Keisler said the company has begun testing the use of active RFID systems to track expensive tools in the Cincinnati R&D center, and this project may be officially launched in the second half of this year.
[ad_2]